Mu-Metall-Folie mit hervorragenden magnetischen Eigenschaften
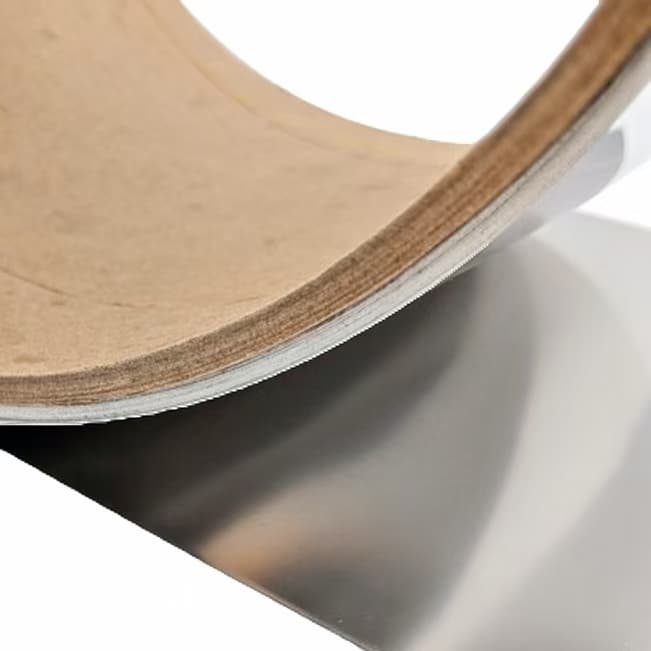
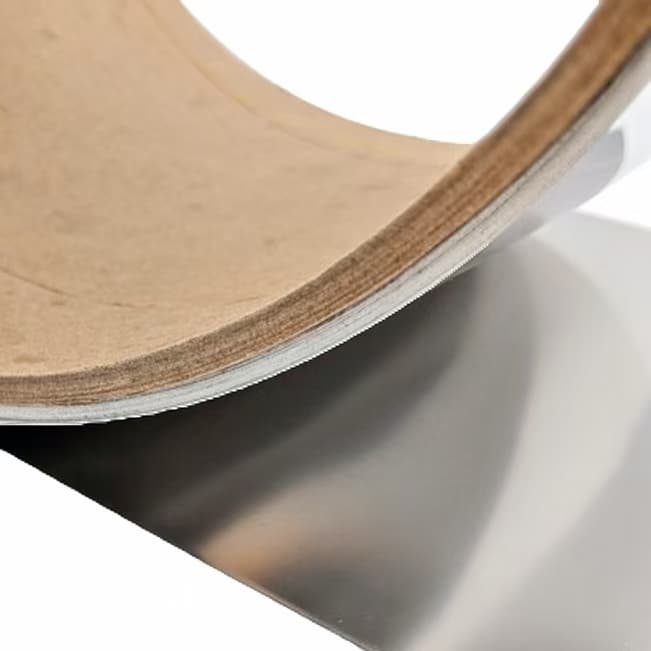
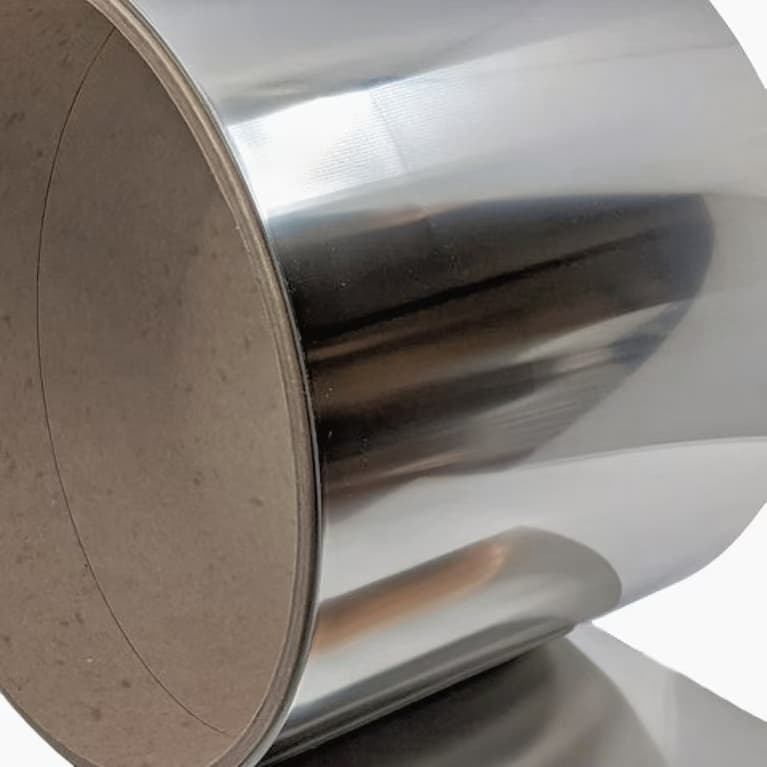
Mu-Metall-Foliespielt als Präzisionsmaterial mit hervorragenden magnetischen Eigenschaften eine unersetzliche Rolle in zahlreichen High-End-Bereichen wie der elektronischen Kommunikation, der Luft- und Raumfahrt und der medizinischen Ausrüstung. Seine Eigenschaften wie hohe magnetische Permeabilität und niedrige Koerzitivfeldstärke machen es zu einer idealen Wahl für die Herstellung leistungsstarker magnetischer Komponenten und elektromagnetischer Abschirmungsmaterialien.
Abstrakt: Dieser Artikel befasst sich mit dem Produktionsprozess von Mu-Metall-Folien und deckt den gesamten Arbeitsablauf von der Auswahl der Rohstoffe bis zur Herstellung des Endprodukts ab. In der Phase der Rohstoffaufbereitung werden hochreines Eisen, Nickel und andere Rohstoffe einer strengen Kontrolle unterzogen, um eine genaue Dosierung zu gewährleisten. Im Schmelzprozess werden fortschrittliche Technologien wie das Vakuum-Induktionsschmelzen eingesetzt, um die Einheitlichkeit der Legierungszusammensetzung zu gewährleisten. Warm- und Kaltwalzen werden in geordneter Weise durchgeführt, um die Materialstärke schrittweise zu verringern und die Struktur zu optimieren. Durch die kritische Wärmebehandlung bei bestimmten Temperaturen und Atmosphären werden die magnetischen Eigenschaften deutlich verbessert. Die Oberflächenbehandlung gewährleistet die Korrosionsbeständigkeit und die Oberflächenqualität der Folie, und schließlich werden durch die Endbearbeitung und das Schneiden qualifizierte Produkte erzielt. Alle Glieder sind eng miteinander verbunden, und jede noch so kleine Änderung kann erhebliche Auswirkungen auf die magnetischen und physikalischen Eigenschaften der Mu-Metall-Folie haben. Eine strenge Kontrolle der Prozessparameter ist das Kernstück der Herstellung hochwertiger Mu-Metall-Folien.
Inhaltsübersicht
Mu-Metall-Foliespielt als Präzisionsmaterial mit hervorragenden magnetischen Eigenschaften eine unersetzliche Rolle in zahlreichen High-End-Bereichen wie der elektronischen Kommunikation, der Luft- und Raumfahrt und der medizinischen Ausrüstung. Seine Eigenschaften wie hohe magnetische Permeabilität und niedrige Koerzitivfeldstärke machen es zu einer idealen Wahl für die Herstellung leistungsstarker magnetischer Komponenten und elektromagnetischer Abschirmungsmaterialien. Um diese herausragenden Eigenschaften zu erreichen, ist ein komplexer und präziser Produktionsprozess erforderlich. Im Folgenden wird der Herstellungsprozess von Mu-Metall-Folie ausführlich erläutert.
1. Vorbereitung des Rohmaterials
- Auswahl von Rohstoffen: Die Hauptbestandteile der Mu-Metall-Folie sind Eisen (Fe) und Nickel (Ni). Um die hervorragende Leistung zu gewährleisten, sind hochreine Rohstoffe erforderlich. Der Reinheitsgrad von Eisen und Nickel muss im Allgemeinen über 99,9% liegen. Bei der Herstellung von Mu-Metall-Folien des Typs 80Ni-20Fe muss der Reinheitsgrad des Nickels beispielsweise mindestens 99,95% und der des Eisens mindestens 99,9% betragen. Zusätzlich können Spurenelemente wie Molybdän (Mo), Kupfer (Cu) und Chrom (Cr) je nach den spezifischen Leistungsanforderungen hinzugefügt werden. Zum Beispiel kann die Zugabe von 0,5%-2% Molybdän die Widerstandsfähigkeit und Härte der Legierung verbessern.
- Batching-Berechnung: Die Dosierung der einzelnen Rohstoffe wird nach genauen Berechnungsmethoden auf der Grundlage der angestrebten Legierungszusammensetzung bestimmt. Bei der Herstellung von 1J79 mu-Metallfolie (mit einem Nickelgehalt von 78,5%-79,5%, wobei der Rest aus Eisen besteht und eine geringe Menge Molybdän usw. enthält) ist es beispielsweise erforderlich, die Eingangsmenge jedes Rohstoffs entsprechend der Legierungsmasse und dem Anteil jedes Elements genau zu berechnen, um eine minimale Abweichung in der Zusammensetzung zu gewährleisten. Zum Wiegen der Rohstoffe werden hochpräzise elektronische Waagen mit einer Genauigkeit von ±0,001 g verwendet, um die Genauigkeit der Dosierung zu gewährleisten.
2. Schmelzen
- Verhüttungsmethoden: Das Vakuum-Induktionsschmelzen oder das Lichtbogenschmelzen werden häufig eingesetzt. Beim Vakuum-Induktionsschmelzen werden die Rohstoffe in einen Ofen mit einem Vakuum von 10-³ - 10-⁴Pa gegeben und durch Induktionserwärmung geschmolzen. Beim Schmelzen von 80Ni-20Fe-Legierungen zum Beispiel kann die Vakuumumgebung im Ofen die Einbindung von Verunreinigungsgasen wie Sauerstoff und Stickstoff wirksam reduzieren und die Bildung von Oxid- und Nitrideinschlüssen verhindern, wodurch nachteilige Auswirkungen auf die magnetischen Eigenschaften vermieden werden.
- Kontrolle des Schmelzprozesses: Die Schmelztemperatur wird genau kontrolliert und liegt im Allgemeinen zwischen 1500 und 1600 °C. Zum Beispiel wird die Schmelztemperatur von 80Ni-20Fe-Legierungen meist auf etwa 1550℃ geregelt, um sicherzustellen, dass die Rohstoffe vollständig geschmolzen sind und die Zusammensetzung gleichmäßig vermischt ist. Die Schmelzzeit wird je nach Legierungsmenge und Ofentyp eingestellt und beträgt in der Regel 1 bis 3 Stunden. Während dieser Zeit ist kontinuierliches Rühren erforderlich, und zur Förderung der Homogenisierung der Zusammensetzung kann elektromagnetisches Rühren eingesetzt werden.
- Gießen und Umformen: Nach dem Schmelzen wird die flüssige Legierung in eine spezielle Form gegossen, um einen Barren zu bilden. Die Dicke des Barrens beträgt im Allgemeinen 10 - 50 mm. Der Barren, der für die Herstellung von Mu-Metall-Folie mit herkömmlicher Dicke verwendet wird, hat zum Beispiel eine Dicke von 20 - 30 mm. Die Abkühlungsgeschwindigkeit während des Gießens wird kontrolliert, und es wird eine langsame Abkühlungsmethode angewandt (z. B. eine Abkühlungsgeschwindigkeit von 5 - 10℃/min), um innere Spannungen, Lunker, Porosität und andere Defekte im Barren zu reduzieren.
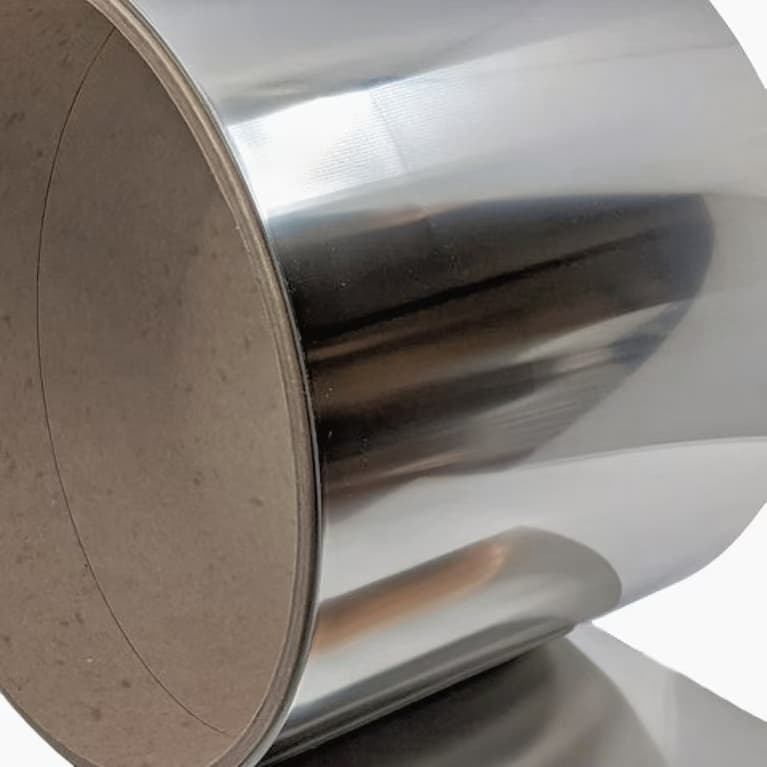
3. Warmwalzen
- Wärmebehandlung: Der Barren wird auf 800 - 1000℃ erhitzt. Die spezifische Temperatur hängt von der Zusammensetzung der Legierung ab. So erfordert beispielsweise Mu-Metall, das mehr Legierungselemente wie Molybdän enthält, eine etwas höhere Erhitzungstemperatur von 900 - 1000℃, um die Plastizität des Materials zu erhöhen und das anschließende Walzen zu erleichtern.
- Rollender Prozess: Das Warmwalzen erfolgt in mehreren Durchgängen, um die Dicke des Blocks schrittweise zu verringern. Die Reduktion pro Stich wird auf 10% - 30% gesteuert. Der erste Walzstich kann z.B. auf 20% eingestellt werden, und die nachfolgenden Stiche werden entsprechend der Materialverformung und der Kapazität der Walzanlage angepasst. Durch mehrere Stiche des Warmwalzens wird die Dicke des Barrens von ursprünglich 10 - 50 mm auf 1 - 5 mm reduziert, wodurch ein Rohling für das Kaltwalzen entsteht.
- Optimierung des Walzprozesses: Die Walzgeschwindigkeit wird kontrolliert und liegt im Allgemeinen zwischen 0,5 und 2 m/s. Eine zu hohe Geschwindigkeit kann zu einer übermäßigen Walzkraft führen, die Materialrisse verursacht; eine zu niedrige Geschwindigkeit beeinträchtigt die Produktionseffizienz. In der Zwischenzeit werden die Oberflächenrauheit der Walzen und die Schmierbedingungen angepasst, und zur Schmierung wird spezielles Walzöl verwendet, um die Walzkraft zu verringern und die Oberflächenqualität des Blechs zu verbessern.
4. Kaltwalzen
- Zweck und Ausrüstung des Kaltwalzens: Beim Kaltwalzen wird die Dicke des warmgewalzten Blechs weiter auf die angestrebte Foliendicke (in der Regel 0,01 - 0,1 mm) reduziert und die Körnung verfeinert, um die Materialdichte zu verbessern. Hochpräzisionswalzwerke, wie z. B. 20-Rollen-Walzwerke, werden eingesetzt, um eine genaue Kontrolle der Foliendicke zu erreichen.
- Multi-Pass-Kaltwalzverfahren: Das Kaltwalzen erfolgt in mehreren Durchgängen, wobei die Reduzierung pro Durchgang auf 5% - 20% gesteuert wird. Die Reduzierung eines 1 mm dicken warmgewalzten Blechs auf eine 0,05 mm dicke Folie kann beispielsweise 10 bis 15 Walzstiche erfordern. Mit zunehmender Anzahl der Walzstiche nimmt der Grad der Kaltverfestigung des Materials zu, so dass es notwendig ist, die Walzkraft und -geschwindigkeit angemessen anzupassen.
- Zwischenglühbehandlung: Während des Kaltwalzens wird eine Zwischenglühung eingelegt. Die Glühtemperatur beträgt 400 - 600℃ und wird im Vakuum oder in einer wasserstoffgeschützten Atmosphäre durchgeführt. Das Zwischenglühen kann Arbeitsspannungen beseitigen und die Plastizität des Materials wiederherstellen. Das Zwischenglühen wird beispielsweise alle 3 bis 5 Kaltwalzstiche durchgeführt, um günstige Bedingungen für das anschließende Kaltwalzen zu schaffen.
- Kontrolle von Dicke und Oberflächenqualität: Die Foliendicke wird in Echtzeit mit einem hochpräzisen Dickenmessgerät überwacht, wobei die Dickentoleranz innerhalb von ±1μm liegt. Zur Gewährleistung der Oberflächengüte der Folie mit einer Oberflächenrauheit Ra ≤ 0,1 μm werden fortschrittliche Technologien und Geräte zur Oberflächenbehandlung eingesetzt.
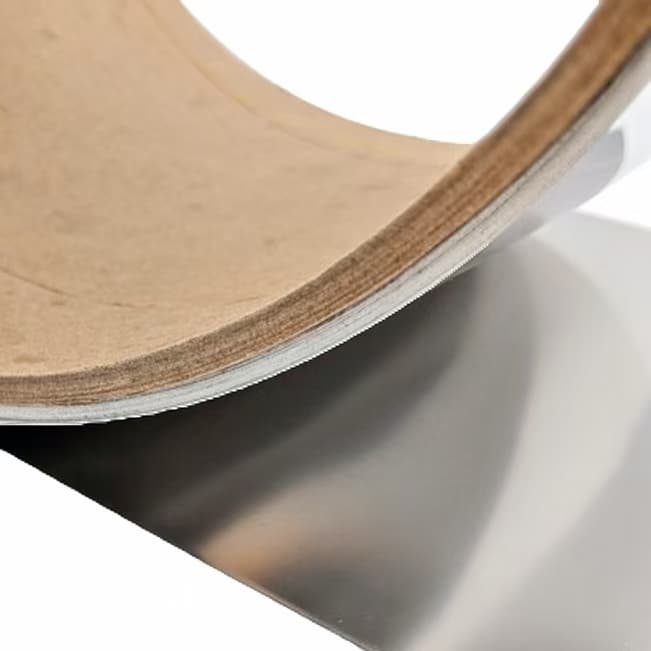
5. Wärmebehandlung
- Zweck und Rolle des Glühens: Die Wärmebehandlung ist ein wichtiges Element zur Optimierung der magnetischen Eigenschaften von Mu-Metall-Folien. Durch Glühen wird die Kristallstruktur der Legierung angepasst, um die magnetische Permeabilität zu verbessern und die Koerzitivfeldstärke zu verringern. Beispielsweise kann eine geeignete Glühbehandlung die magnetische Permeabilität von 80Ni-20Fe-Mu-Metallfolien um ein Vielfaches erhöhen.
- Parameter des Glühprozesses: Die Glühtemperatur wird je nach Zusammensetzung der Legierung festgelegt. Zum Beispiel beträgt die Glühtemperatur einer 80Ni-20Fe-Legierung im Allgemeinen 1000-1200℃, mit einer typischen Temperatur von 1100℃. Das Glühen erfolgt in einer Atmosphäre aus hochreinem Wasserstoff (Taupunkt ≤ -60℃) oder im Hochvakuum, um eine Oxidation der Legierung zu verhindern. Die Abkühlgeschwindigkeit ist langsam, in der Regel 5 - 10℃/min. Einige Legierungen müssen bei einer Abkühlung auf etwa 500℃ einer isothermen Behandlung unterzogen werden, um die Struktur weiter zu optimieren.
- Einfluss der Wärmebehandlung auf die magnetischen Eigenschaften: Eine geeignete Wärmebehandlung kann die Bildung geordneter Phasen (z. B. Ni₃Fe) in der Legierung fördern, Kristalldefekte reduzieren und den Widerstand gegen die Bewegung der Domänenwände verringern, wodurch die magnetische Permeabilität erheblich verbessert wird. Studien haben gezeigt, dass die anfängliche magnetische Permeabilität von Mu-Metall-Folien, die einer optimierten Wärmebehandlung unterzogen wurden, von 50 mH/m auf über 100 mH/m erhöht werden kann.
6. Oberflächenbehandlung
- Entfernung der Oxidschicht: Durch Beizen (z. B. mit einer gemischten Lösung aus Salpetersäure und Flusssäure) oder Elektropolieren wird die Oxidschicht entfernt, die nach der Wärmebehandlung zurückbleiben kann. Beim Beizen werden die Beizzeit und die Temperatur so gesteuert, dass die Oxidschicht entfernt wird, ohne das Grundmaterial anzugreifen. Beim Elektropolieren wird durch genaue Steuerung der Stromdichte und der Elektrolytzusammensetzung eine glatte und ebene Folienoberfläche erzielt.
- Korrosionsbeständigkeit Behandlung: In einigen Anwendungsszenarien wird die Mu-Metall-Folie zur Verbesserung der Korrosionsbeständigkeit einer Oberflächenbeschichtung (z. B. Vernickelung, Verchromung) oder einer Passivierungsbehandlung unterzogen. Die Dicke der Vernickelungsschicht beträgt im Allgemeinen 0,5 - 5μm und kann durch Galvanisieren oder stromloses Beschichten aufgebracht werden. Die Passivierungsbehandlung bildet einen Passivierungsfilm auf der Folienoberfläche, um die Korrosionsbeständigkeit in feuchten Umgebungen zu verbessern.
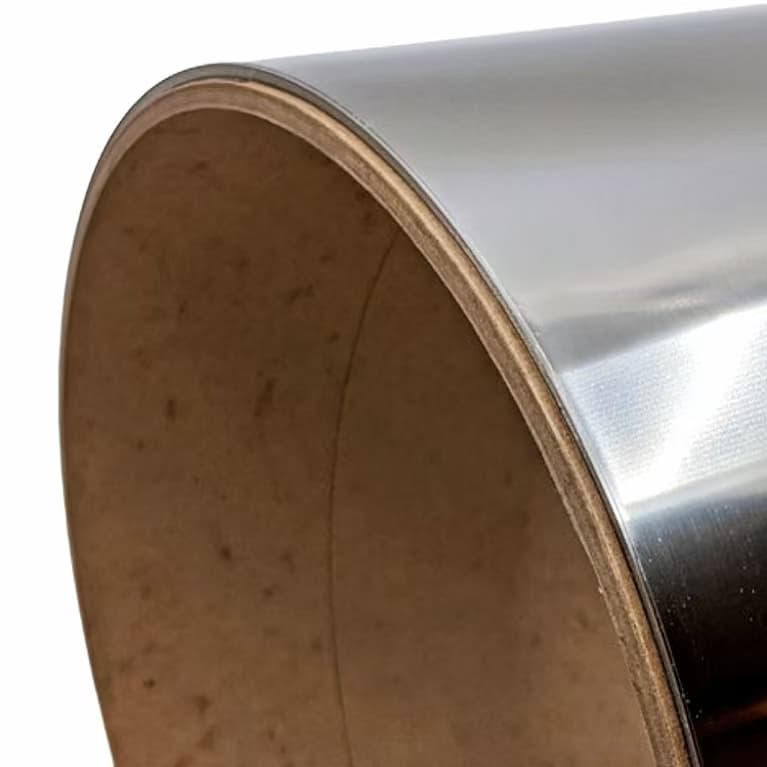
7. Endbearbeitung und Schlitzen
- Abflachende Behandlung: Eine Präzisionsrichtmaschine wird verwendet, um die Folie zu glätten und Fehler wie Verformungen und Welligkeit zu beseitigen und die Ebenheit der Folie zu gewährleisten. Während des Richtens werden der Druck und der Abstand der Richtwalzen genau eingestellt, um den Ebenheitsfehler der Folie innerhalb eines minimalen Bereichs zu kontrollieren.
- Schlitzverfahren: Je nach Kundenwunsch werden große Folienrollen in Coils oder Einzelblätter mit bestimmten Breiten zerschnitten. Es werden hochpräzise Spaltanlagen eingesetzt, deren Spaltgenauigkeit auf ±0,1 mm kontrolliert wird, um die genauen Abmessungen der geschnittenen Folie zu gewährleisten.
Zusammenfassend lässt sich sagen, dass die Produktion von Mu-Metall-Folie ist ein eng verknüpfter Prozess mit extrem hohen Anforderungen an die Details. Von der sorgfältigen Auswahl der Rohstoffe bis hin zur präzisen Kontrolle der einzelnen Prozesse wirkt sich alles direkt auf die Leistung des Endprodukts aus. Mit der kontinuierlichen Entwicklung von Wissenschaft und Technik werden die Leistungsanforderungen an Mu-Metall-Folien zunehmend steigen, was unweigerlich zu einer kontinuierlichen Innovation und Optimierung des Produktionsprozesses führt und den Fortschritt verwandter Industriezweige maßgeblich unterstützt.
Das könnte Ihnen auch gefallen
-
EMI-Bänder, EMC-Folien, leitfähige Textilien und halbleitende Vliese
Glasfaser-Aluminium-Folien-Band
🔧 Produktübersicht📌 Hauptmerkmale & Benefits⚙️ Technische Daten🎯 Anwendungen🛠 Anpassungsmöglichkeiten📦 Verpackung & Lieferung🧩 Warum Handa wählen?📞 Angebot oder Muster anfordern Das Glasfaser-Aluminiumfolienband von Handa ist eine hochleistungsfähige Isolier- und Dichtungslösung, die für anspruchsvolle industrielle, ......
-
EMI-Bänder, EMC-Folien, leitfähige Textilien und halbleitende Vliese
Leitfähiges Aluminiumband
Was ist leitfähiges Aluminiumband?Hauptmerkmale von leitfähigem AluminiumbandGängige Anwendungen von leitfähigem Aluminiumband1. Abschirmung gegen elektromagnetische Interferenzen (EMI) und Hochfrequenzstörungen (RFI)2. Kabelummantelung und Kabelbaumschutz3. Elektrische Erdung4. Abschirmung von gedruckten Schaltungen (PCB)5. HVAC-Kanalabdichtung6. Kfz-Elektronik7.......
-
Lösungen und Materialien für Abschirmdichtungen
Drahtgestrickte Dichtungen
Handa Shielding TCS Dual-Wing Wire Mesh Core Technology: TCS MaterialinnovationDual-Wing-StrukturdesignTechnische SpezifikationenAnwendungen1. Luft- und Raumfahrt und Verteidigung2. Medizinische Geräte3. Telekommunikation4. IndustrieelektronikAnpassung und IntegrationLeistungsvorteilePrüfung und KonformitätWarum Handa Shielding wählen? Handa Shielding's TCS Dual-Wing Wire Mesh ist ein hochmodernes elektromagnetisches Interferenz (EMI)......
-
Fingerabdrücke
Beryllium-Kupfer-Fingerstrips-Serie
Versilberte Beryllium-Kupfer-Fingerstockdichtungen zur EMI/RFI-Abschirmung 1. Überblick über versilberte Beryllium-Kupfer-Fingerstock-Dichtungen2. Material und Oberflächenbeschichtung3. Arten von Fingerstock-/Fingerstrip-Dichtungen von Handa Shielding4. Leistungsmerkmale von versilberten Beryllium-Kupfer-Fingerstock-Dichtungen5. Anwendungen von versilberten Beryllium-Kupfer-Fingerstock-Dichtungen6. Anpassungsmöglichkeiten7. Einhaltung......
-
Fingerabdrücke
Rechtwinklige Abschirmung Fingerstrip
Handa Berylliumkupfer-Fingerstrips/Fingerstrümpfe für Hochleistungs-EMI/RFI-Abschirmung 1. Einführung2. Materialeigenschaften von Berylliumkupfer2.1. Mechanische Festigkeit2.2. Elektrische und thermische Leitfähigkeit2.3. Korrosions- und Umweltbeständigkeit2.4. Konformität und Sicherheit3. Konstruktion und Fertigungsverfahren3.1. Werkstoffauswahl3.2. Umformtechniken3.3. Oberflächenveredelung3.4. Qualitätskontrolle4.......