EMI Shielding Spiral Tubes: An In‐Depth Technical Report
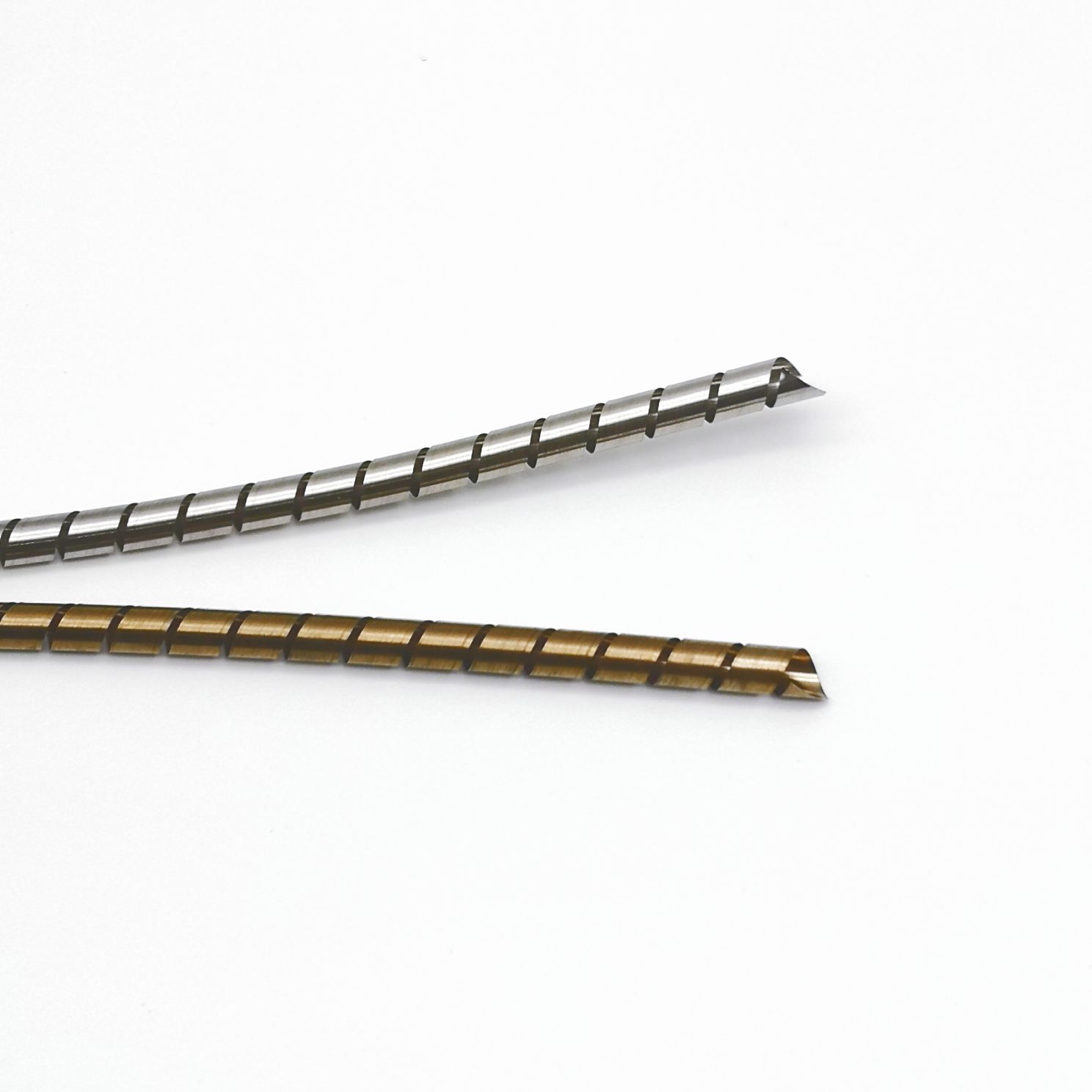
EMI Shielding Spiral Tubes-Handashielding
目次
1. Introduction
Electromagnetic interference (EMI) has long been a critical challenge for high-performance electronic systems. The miniaturization of devices, coupled with increasing operating frequencies and higher integration densities, has driven the need for effective EMI management solutions. EMI shielding spiral tubes have emerged as an essential component in modern electronics, providing robust electromagnetic protection while maintaining mechanical flexibility and durability.
This report examines EMI shielding spiral tubes in great detail. It explores how innovations in materials such as beryllium copper and advanced alloys like Elgiloy, combined with optimized spiral designs and specialized plating processes, have enabled these components to meet the stringent demands of modern technology sectors. Whether in communications, medical devices, semiconductor manufacturing, industrial automation, aerospace, or consumer electronics, the importance of high-performance EMI shielding cannot be overstated.
In the following sections, we provide an extensive analysis of the design, manufacturing, application, and future prospects of EMI shielding spiral tubes. Our discussion is enriched with insights from industry leaders including Handashielding, ensuring that the report reflects both the state-of-the-art technology and the practical challenges faced in various applications.
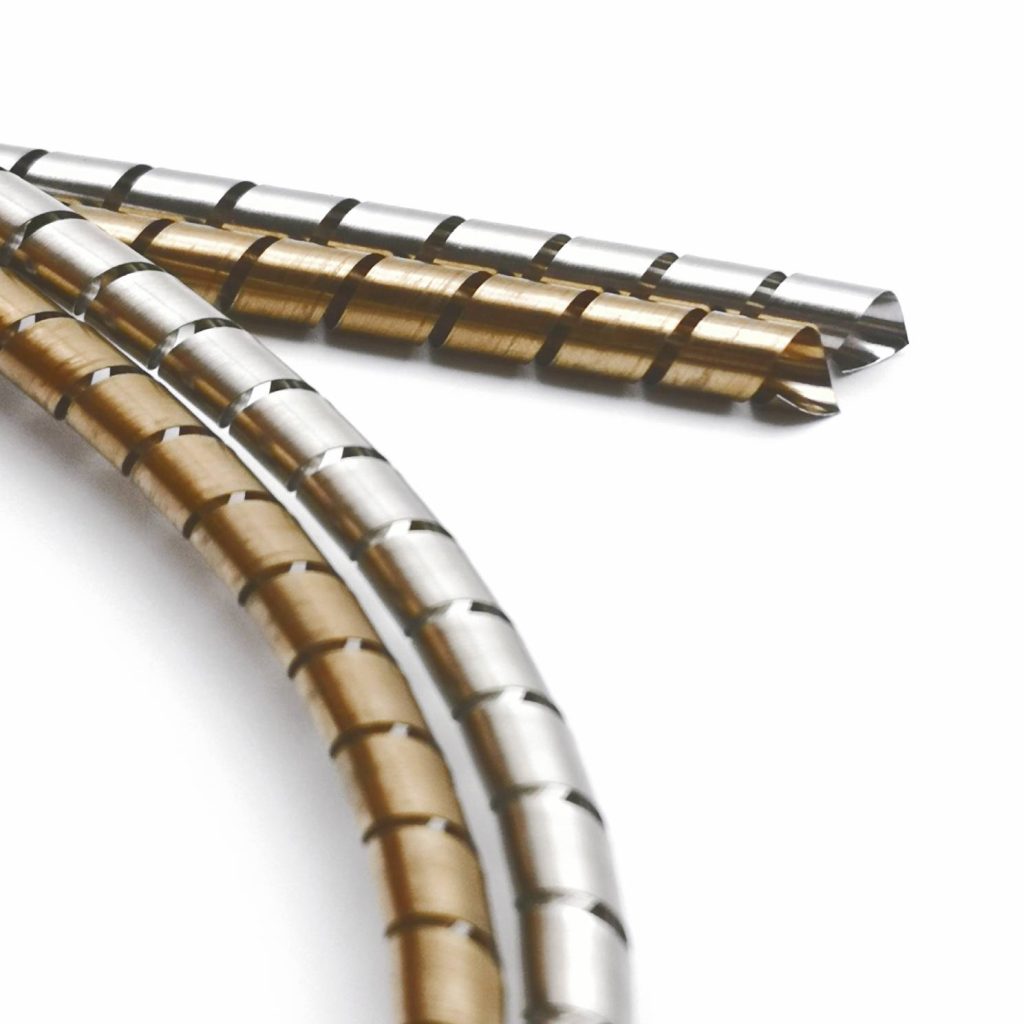
2. Historical Background and Technological Evolution
Early EMI Shielding Techniques
In the early days of electronics, EMI was managed using simple metal enclosures and basic conductive coatings. As radio frequency (RF) communications and early computers emerged in the mid-20th century, designers realized that unshielded circuits could easily pick up unwanted signals. Conventional shielding methods—often bulky and inflexible—provided limited protection, especially as operating frequencies increased.
The Emergence of Spiral Tube Technology
By the 1980s and 1990s, research in material science and electromagnetic theory led to the development of more sophisticated EMI shielding solutions. Among these, the concept of forming metallic materials into spiral tubes proved revolutionary. The spiral design offered several advantages:
- Increased Surface Area: The helical geometry maximizes the surface area available for reflection and absorption of electromagnetic waves.
- 柔軟性: Spiral tubes can bend and adapt to different shapes, making them ideal for applications with tight spatial constraints.
- Enhanced Mechanical Properties: The unique structure provides excellent resistance to mechanical fatigue and compression, ensuring long-term durability.
Technological Advancements Through the 21st Century
In recent decades, technological advancements have focused on further miniaturization and improved performance of EMI shielding components. The advent of 5G and the anticipation of 6G technologies necessitated shielding solutions capable of handling wide frequency bands—from a few kilohertz to tens of gigahertz. At the same time, the growing demand in medical and aerospace applications drove the development of materials that could withstand extreme environments, including wide temperature ranges and high radiation levels.
Pioneering companies, notably Handa Shielding and Spira, have played a crucial role in this evolution. Their continuous investment in research and development has led to new materials, such as advanced beryllium copper alloys and corrosion-resistant stainless steels, as well as innovations in plating processes that dramatically enhance EMI shielding effectiveness.
Summary of Historical Impact
Today, EMI shielding spiral tubes are recognized as a mature technology that not only meets the challenges of high-frequency interference but also provides design flexibility and robust performance in harsh environments. Their evolution reflects a broader trend toward smarter, more resilient electronic systems that can operate reliably under a multitude of conditions.
3. Fundamental Principles of EMI Shielding
Understanding Electromagnetic Interference
Electromagnetic interference occurs when unwanted electromagnetic energy disturbs the normal operation of electronic equipment. This interference can arise from external sources (e.g., radio transmissions, power lines) or from internal sources (e.g., switching power supplies, high-speed digital circuits). The effects of EMI range from minor signal degradation to complete system failure, particularly in sensitive applications such as medical imaging or satellite communications.
Mechanisms of EMI Shielding
The primary mechanisms through which EMI shielding functions include:
- Reflection: Conductive materials reflect incoming electromagnetic waves, preventing them from entering sensitive regions of a device.
- Absorption: Certain materials can absorb electromagnetic energy, converting it into heat that is then dissipated.
- Multiple Reflections: In complex structures like spiral tubes, the geometry creates multiple internal reflections that further attenuate the energy of incident waves.
- Edge and Gap Effects: Special design features, such as overlapping joints or O-ring seals, help prevent leakage at connection points.
Role of Spiral Tubes in EMI Shielding
EMI shielding spiral tubes embody these principles by combining a helical geometry with high-conductivity materials. Their design ensures that electromagnetic waves encounter several layers of attenuation as they travel along the spiral. The structure’s flexibility allows it to conform to the contours of various electronic assemblies, while its durability ensures that the shielding effect is maintained over long operational lifetimes.
Theoretical Models and Simulation
Recent advancements in computational electromagnetics have enabled detailed modeling of spiral tube performance. Finite element analysis (FEA) and other simulation tools are used to predict the behavior of EMI shielding components under various conditions. These models help designers optimize key parameters such as:
- Spiral Pitch: The distance between adjacent coils, which influences the number of reflections.
- Wall Thickness: Thicker walls provide greater attenuation but may reduce flexibility.
- Plating Thickness: The choice and thickness of the plating material (e.g., silver, gold, or nickel) significantly affect surface conductivity and, hence, shielding effectiveness.
Through simulation, researchers and engineers can fine-tune these parameters to achieve the desired performance across a wide frequency range—from low-frequency power line noise to high-frequency millimeter waves.
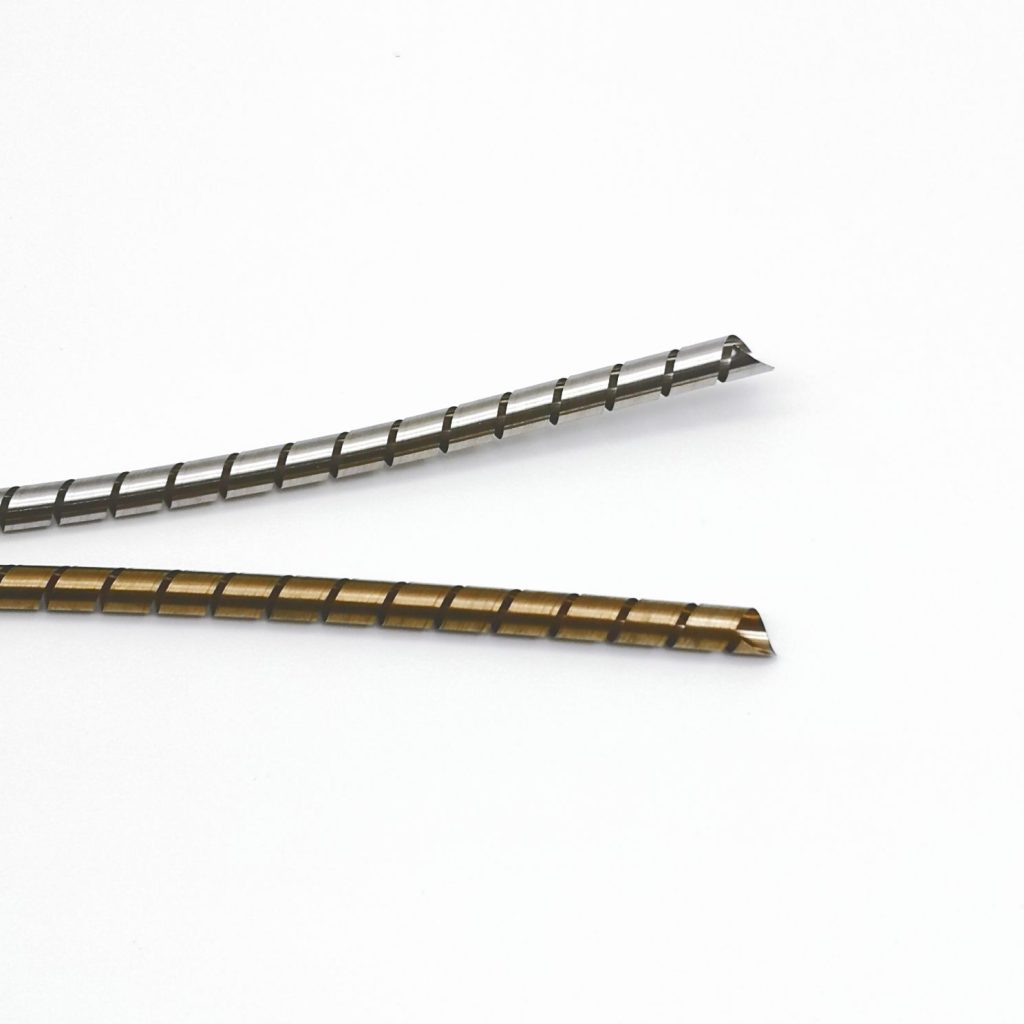
4. Material Innovations and Structural Designs
The effectiveness of EMI shielding spiral tubes is largely determined by the choice of materials and the structural design. In this section, we delve into the most common materials used, discuss the impact of plating technologies, and explain how multi-layered and miniaturized designs contribute to overall performance.
4.1 Beryllium Copper and Alloy Innovations
Beryllium copper (BeCu) has been a cornerstone of EMI shielding solutions due to its excellent combination of electrical conductivity, mechanical strength, and elasticity. Key features include:
- High Conductivity: Enhances the reflection of electromagnetic waves.
- Excellent Elasticity: Enables the tube to maintain its shape even after repeated bending.
- Resistance to Permanent Deformation: Ensures long-term reliability, even under cyclic loading conditions.
Advanced BeCu alloys have been developed to further improve these properties. For instance, modifications in alloy composition can enhance corrosion resistance and thermal stability, making these tubes suitable for extreme environments such as space and military applications.
4.2 Stainless Steel and Alternative Alloys
Stainless steel variants (e.g., 304, 316, and 301) are also widely used in EMI shielding spiral tubes. Their advantages include:
- Superior Corrosion Resistance: Ideal for harsh chemical and high-humidity environments.
- Robust Mechanical Strength: Withstand high compression forces and mechanical shocks.
- Thermal Stability: Remain stable over a wide range of temperatures.
In applications where weight is a critical factor (such as in aerospace), stainless steel tubes are sometimes plated with nickel or tin to enhance conductivity while reducing mass. Additionally, exotic alloys like Elgiloy and Hastelloy are used in applications that demand both high corrosion resistance and high mechanical strength, especially under extreme temperatures.
4.3 Plating Technologies and Their Impact
Plating plays a crucial role in enhancing the EMI shielding performance of spiral tubes. Common plating techniques include:
- Tin Plating: Improves conductivity and offers good solderability.
- Nickel Plating: Provides a robust barrier against corrosion and mechanical wear.
- Silver and Gold Plating: Although more expensive, these metals offer superior conductivity and can dramatically improve shielding effectiveness in high-frequency applications.
Plating thickness is a critical parameter; a thicker plating layer can provide additional shielding but may also impact flexibility. Recent innovations allow manufacturers to control plating thickness with high precision, ensuring that the tubes deliver optimal performance without compromising mechanical properties.
4.4 Multi-Layered and Miniaturized Structures
As electronic systems become increasingly compact, the need for miniaturized EMI shielding solutions has grown. Multi-layered spiral tubes are designed to:
- Enhance Shielding Performance: Multiple layers create additional barriers, ensuring that even very high-frequency interference is effectively attenuated.
- Improve Mechanical Resilience: Layered designs can distribute mechanical stresses more evenly, reducing the risk of fatigue and deformation.
- Enable Customization: Manufacturers can tailor the number of layers and overall dimensions to suit specific applications, from tiny smartphone components to larger industrial systems.
Miniaturization challenges include maintaining shielding performance while reducing the tube’s diameter. Advanced manufacturing processes such as precision rolling and micro-forming techniques are employed to create tubes with diameters as small as 0.5 mm, ensuring that even the most space-constrained devices can benefit from effective EMI protection.
5. Manufacturing Processes and Quality Control
The production of EMI shielding spiral tubes is a highly specialized process that combines advanced metallurgy, precision engineering, and rigorous quality control. In this section, we outline the key manufacturing steps and the quality assurance measures that ensure each product meets stringent performance standards.
5.1 Material Selection and Preprocessing
The process begins with the careful selection of raw materials. Manufacturers typically choose high-purity ベリリウム銅, ステンレス鋼, or alternative alloys based on the application requirements. Preprocessing steps include:
- Annealing: Heat treatment processes are applied to optimize the material’s mechanical properties, such as ductility and elasticity.
- 表面処理: The raw metal is cleaned and polished to remove impurities and ensure proper adhesion of plating layers later in the process.
5.2 Forming the Spiral Tube: Techniques and Methods
Forming the EMI shielding spiral tubes involves bending the preprocessed metal strip into a helical shape. This step is critical, as it determines the final geometry and, therefore, the EMI shielding performance. Common forming techniques include:
- Roll Bending: The metal strip is passed through a series of rollers that gradually form it into a spiral. Precision control of the roller speed and gap is essential to achieve uniformity.
- Mandrel Forming: In some cases, a mandrel (a cylindrical tool) is used to shape the tube. This method is particularly useful for achieving very tight spiral pitches and small diameters.
Throughout the forming process, manufacturers monitor critical parameters such as the spiral pitch, wall thickness, and overall dimensional accuracy. Any deviation from the specified design can lead to suboptimal EMI shielding performance.
5.3 Surface Treatments and Plating Operations
Once the EMI shielding spiral tubes are formed, it undergoes surface treatment and plating. The key steps include:
- Electroplating or Electroless Plating: Depending on the desired properties, the tube is plated with metals such as tin, nickel, silver, or gold. Advanced plating techniques ensure a uniform and defect-free coating.
- Passivation: This step further protects the surface from corrosion, especially in harsh environments. Passivation layers are particularly important for applications in aerospace and medical devices.
- Inspection of Plating Quality: Automated optical and X-ray inspection systems are used to verify the thickness and uniformity of the plating. Any defects are corrected through re-plating or additional surface treatments.
5.4 Testing, Inspection, and Quality Assurance
Rigorous testing is a hallmark of EMI shielding spiral tubes production. Quality assurance measures include:
- Electrical Conductivity Testing: Verifies that the plating and underlying material provide the required level of conductivity to reflect and absorb electromagnetic waves.
- Mechanical Testing: Includes bending fatigue tests, compression tests, and cyclic loading assessments to ensure long-term durability.
- Environmental Testing: Samples are subjected to extreme temperature cycles, humidity, and corrosive environments to verify their performance in real-world conditions.
- Dimensional Inspection: High-precision measurement tools are used to ensure that the spiral tube conforms to the specified tolerances. This is critical for applications in which even slight deviations could compromise EMI performance.
These quality control measures ensure that every EMI shielding spiral tubes leaving the factory is capable of performing reliably under the most demanding conditions.
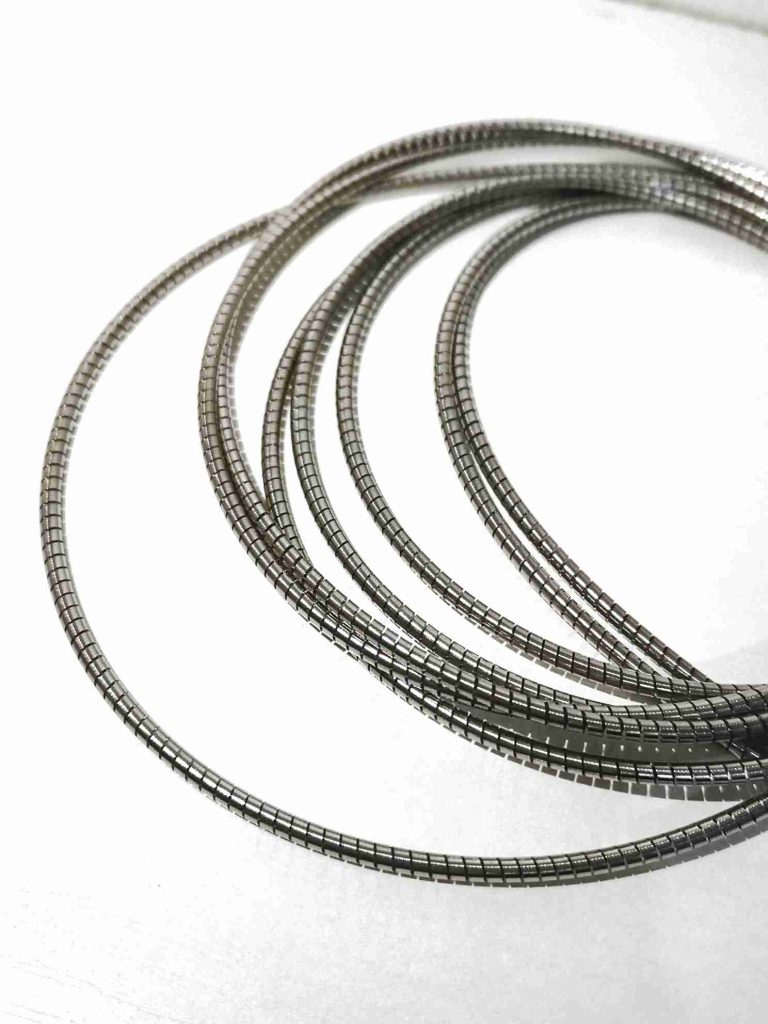
6. Application Fields of EMI Shielding Spiral Tubes
EMI shielding spiral tubes are employed across a wide range of industries. In this section, we provide an exhaustive review of the key application fields, detailing the specific requirements and challenges in each domain.
6.1 Communications and RF Equipment
6.1.1 5G/6G Base Stations
Modern cellular networks—especially those incorporating 5G and future 6G technologies—operate across a broad spectrum of frequencies. Spiral tubes in these applications are used to:
- Shield Antenna Interfaces: Preventing high-frequency interference (2.5 GHz to 28 GHz) from degrading signal quality.
- Maintain Signal Integrity: By reducing crosstalk and reflection within RF connectors, these tubes ensure that high-speed data is transmitted with minimal loss.
- Enhance System Reliability: High-performance plating (silver, gold) and multi-layer designs contribute to shielding efficiencies exceeding 90 dB.
6.1.2 Satellite Communication Modules
Satellite systems require EMI shielding solutions that can operate under extreme conditions:
- Thermal Extremes: Components must remain functional between –60 °C and 120 °C.
- Vibration Resistance: During launch and in orbit, satellites experience significant vibration; EMI shielding spiral tubes are designed to maintain performance despite these stresses.
- Data Transmission Stability: Shielding is crucial to prevent electromagnetic leakage, thereby ensuring reliable communication links with ground stations.
6.1.3 Microwave Devices
Spiral tubes in microwave devices serve to:
- Suppress Parasitic Coupling: By reducing unwanted noise within waveguide assemblies, they improve the performance of filters, amplifiers, and other microwave components.
- Optimize Frequency Response: Precise dimensional control and multi-layer construction help tailor the tube’s performance to specific frequency bands.
Industry Insight:
半田シールド’s product line is widely recognized in the RF market for its customization options, which allow engineers to specify the exact plating, dimensions, and core configurations needed to meet specific frequency and mechanical demands.
6.2 Medical Electronics and Life Sciences
6.2.1 MRI Equipment
Magnetic Resonance Imaging (MRI) systems demand extraordinarily clean electromagnetic environments:
- ケーブル・シールド: Spiral tubes are used to shield control and sensor cables from EMI, thereby reducing image noise in high-field MRI machines (typically 1.5T or higher).
- Material Biocompatibility: Components must meet strict standards for biocompatibility and sterilization, with many products adhering to ISO 13485 requirements.
6.2.2 Implantable Medical Devices
Implantable devices, such as pacemakers and neural stimulators, rely on effective EMI shielding to:
- Isolate Sensitive Circuits: Prevent external interference that could disrupt critical functions.
- Ensure Patient Safety: Maintain device reliability and longevity in the harsh environment of the human body.
- Achieve Regulatory Compliance: Adhere to stringent medical device standards.
6.2.3 Endoscopes and Surgical Robots
Modern surgical instruments require EMI shielding to ensure:
- Electromagnetic Stability: Shielding high-frequency noise (300 kHz to 3 MHz) produced by electrosurgical devices.
- Mechanical Flexibility: Spiral tubes must bend and conform to complex shapes without compromising shielding performance.
- Extended Lifespan: Materials such as Elgiloy alloys combined with silicone cores offer exceptional resistance to fatigue and compression set.
Technical Note:
Medical applications often demand components with over 100,000 bending cycles. Manufacturers like 半田シールド have achieved this by combining advanced materials with precision engineering, ensuring that the tubes remain reliable over extended periods.
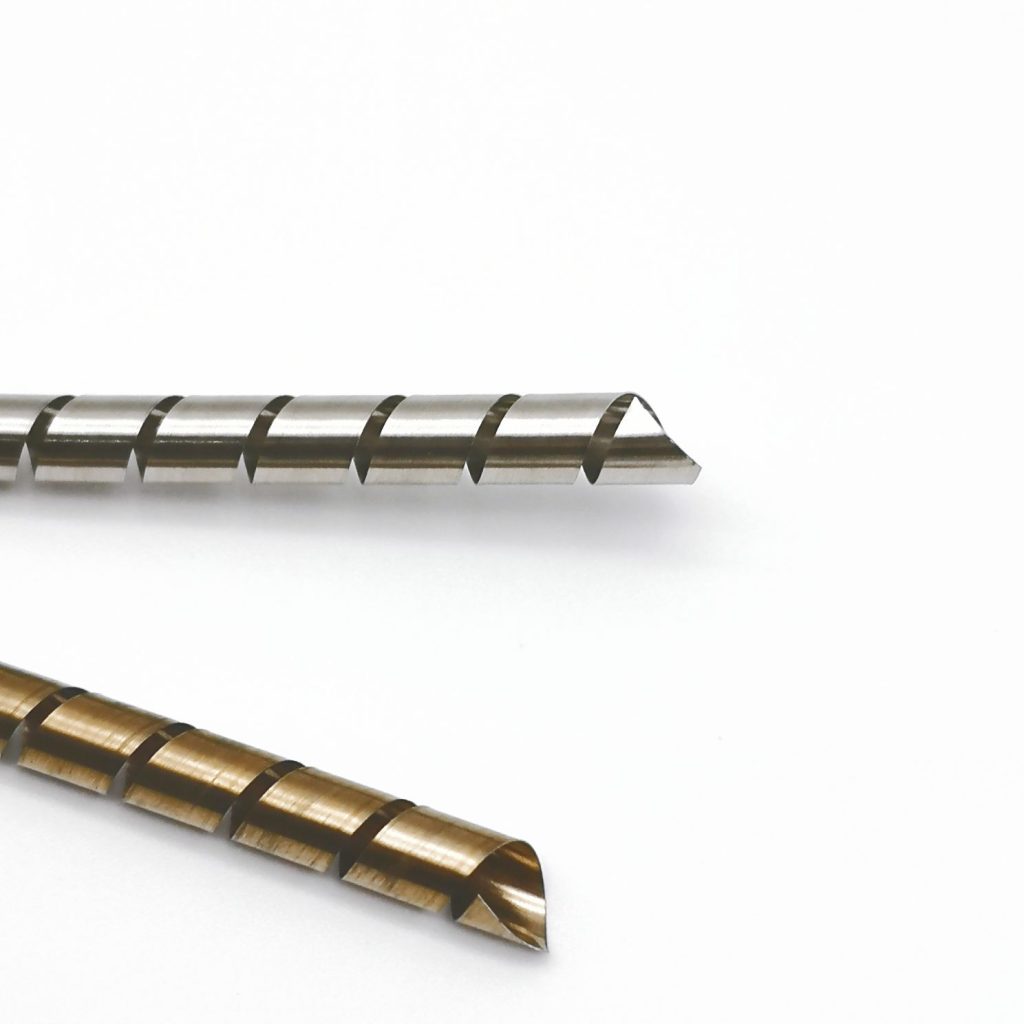
6.3 Semiconductor and Integrated Circuit Manufacturing
6.3.1 Photolithography and Exposure Systems
In semiconductor fabrication:
- Precision Shielding: Spiral tubes are used in photolithography control cables to suppress harmonic interference from power modules (100 kHz to 10 MHz), ensuring nanometer-level exposure accuracy.
- Cleanroom Compatibility: The manufacturing processes for these tubes are designed to comply with Class 1 cleanroom standards, preventing contamination in critical fabrication environments.
6.3.2 Probe Stations and Testing Equipment
For IC testing:
- Miniature Dimensions: Spiral tubes with diameters as small as 0.5 mm help reduce high-frequency crosstalk (up to 20 GHz) in probe stations.
- Enhanced Test Yields: By minimizing interference, these tubes contribute to higher yields and better overall performance of semiconductor devices.
6.3.3 Etching and Deposition Equipment
During the semiconductor manufacturing process:
- 耐食性: Spiral tubes made from Hastelloy or similarly resistant alloys are used to block interference from RF power (e.g., 13.56 MHz) in etching and deposition systems.
- Material Purity: High-purity materials and no-dust processing ensure that the tubes meet the stringent requirements of semiconductor fabrication.
6.4 Industrial Automation and Robotics
6.4.1 Servo Motor and Drive Systems
In industrial automation:
- Precise Motion Control: EMI shielding spiral tubes in servo motor wiring protect sensitive control signals from inverter harmonics (10 kHz to 1 MHz), enabling precision movement with tolerances as tight as ±0.02 mm.
- 耐久性の向上: The tubes are engineered to resist mechanical stress and repeated bending, ensuring reliable operation in high-vibration environments.
6.4.2 Collaborative Robotics (Cobots)
For collaborative robots:
- Compact Design: Ultra-thin spiral tubes (with wall thickness down to 0.1 mm) are used where space is at a premium.
- Low-Fatigue Performance: The material and structural design ensure that the tubes can flex repeatedly without fatigue, essential for dynamic robotic systems.
- Integrated EMI Protection: These components shield sensitive control circuits and sensor arrays from both internal and external electromagnetic disturbances.
6.4.3 Industrial Internet of Things (IIoT)
In the IIoT realm:
- シグナル・インテグリティ: EMI shielding spiral tubes protect sensor and communication signal chains from the wide-band noise (50 Hz to 2.4 GHz) common in factory environments.
- Robust Performance: The tubes help maintain reliable data transmission even in harsh industrial settings with significant electrical noise.
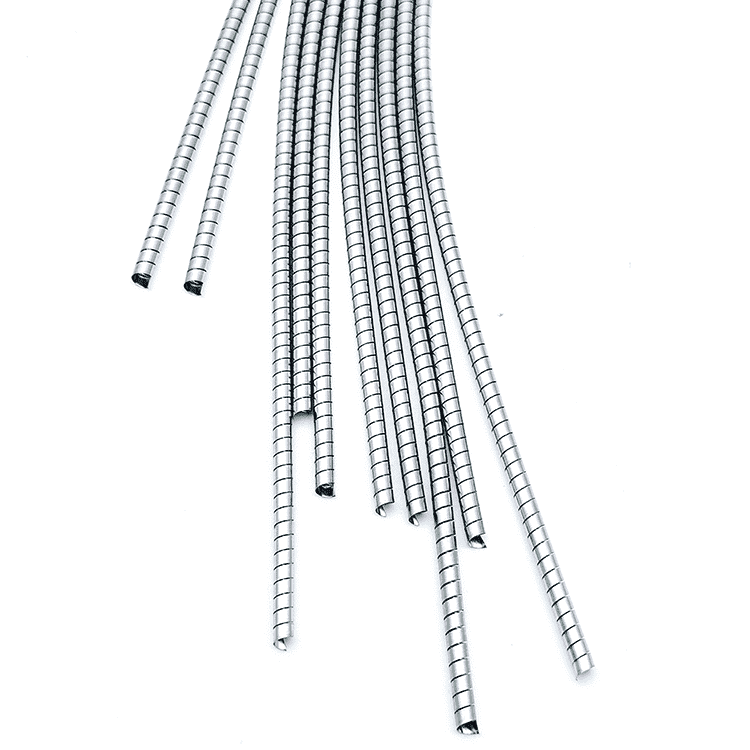
6.5 Aerospace and Defense
6.5.1 Avionics Systems
In modern aircraft:
- EMI Control: Spiral tubes are used to shield wiring and connectors in avionics systems, ensuring that navigation and communication signals are not compromised by engine ignition noise.
- Compliance with DO-160G: The tubes meet rigorous environmental standards set by DO-160G, including vibration, shock, and thermal cycling tests.
6.5.2 Satellite Payloads
For satellite applications:
- Radiation Resistance: EMI shielding spiral tubes made from Hastelloy C-276 and other radiation-resistant materials protect sensitive electronics from high-energy particles in space.
- Extended Operational Lifespan: Robust design features help extend the service life of satellite systems by preventing electromagnetic leakage that could lead to data loss.
- 熱管理: Advanced plating and multi-layer designs ensure stable performance even under rapid thermal fluctuations.
6.5.3 Military Radar and Electronic Warfare
In defense systems:
- High-Frequency Shielding: Spiral tubes are critical in suppressing X-band (8–12 GHz) signal leakage in radar systems, enhancing stealth and anti-jamming capabilities.
- Rugged Durability: These components are built to withstand extreme operational conditions, from high-impact shocks to sustained vibration, meeting MIL-STD-810G standards.
- カスタマイズ: Specific configurations, including the addition of internal cores, are available to handle situations where high compression forces are present.
6.6 New Energy Vehicles and Power Electronics
6.6.1 On-Board Chargers (OBC)
In electric vehicles:
- High-Frequency Noise Suppression: EMI shielding spiral tubes are used to isolate high-frequency switching noise from SiC/GaN power devices (operating between 100 kHz and 1 MHz). This prevents false triggering of the battery management system (BMS).
- Optimized Signal Integrity: By shielding sensitive communication circuits, these tubes help maintain the stability of vehicle-to-grid (V2G) communications.
6.6.2 Battery Management Systems (BMS)
For battery management:
- High-Voltage Isolation: Spiral tubes ensure that high-voltage wiring is properly shielded, enhancing the accuracy of battery state-of-charge (SOC) estimations to within ±1%.
- Reliability Under Stress: The robust design protects the circuitry from EMI even during rapid power fluctuations and high current loads.
6.6.3 Charging Station Communication
At EV charging stations:
- Lightning and Surge Protection: EMI shielding spiral tubes defend against RF interference and transient surges (30 MHz to 1 GHz), ensuring stable communication links.
- Environmental Durability: Enhanced plating and heat-resistant materials ensure that these tubes function reliably in outdoor and industrial settings, where temperature extremes and moisture are common.
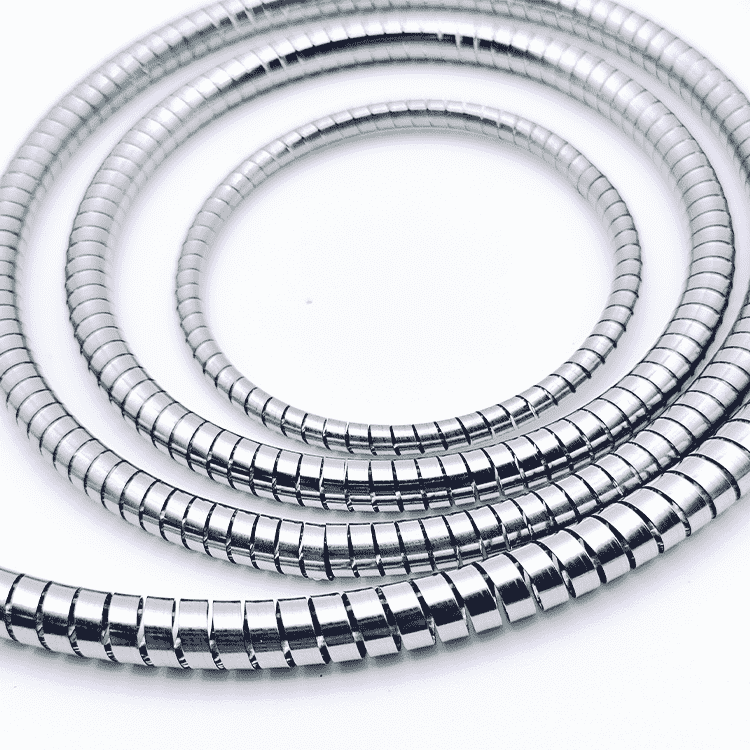
6.7 Consumer Electronics and Wearable Devices
6.7.1 Smartphone and Tablet Antennas
In mobile devices:
- Minimizing Signal Attenuation: Micro-scale spiral tubes, with diameters as low as 0.5 mm, are integrated into antenna assemblies to reduce signal loss, particularly in the millimeter-wave band (around 28 GHz).
- Design Flexibility: Their compact form factor allows integration into the slim profiles of modern smartphones and tablets.
6.7.2 AR/VR Headsets
For augmented and virtual reality systems:
- Dynamic Shielding: Flexible EMI shielding cables, incorporating spiral tubes, adapt to head movements to ensure continuous protection against high-frequency EMI, reducing display flicker and enhancing user experience.
- Comfort and Durability: Ultra-light designs (<5 g/m) ensure that the components add minimal weight, crucial for wearable devices.
6.7.3 Smartwatches and Wearable Sensors
In wearable technology:
- Extended Battery Life: Nano-silver coated spiral tubes block interference in Wi-Fi and Bluetooth frequency bands, leading to improved energy efficiency and a battery life boost of around 10%.
- Ergonomic Integration: The flexibility and lightweight nature of these components allow for seamless integration into curved surfaces and small form factors without compromising shielding performance.
7. Case Studies and Real-World Applications
To illustrate the practical benefits of EMI shielding spiral tubes, this section reviews several case studies from diverse industries.
7.1 Telecommunications Infrastructure
Case Study: 5G Base Station Optimization
A leading telecommunications company integrated advanced EMI shielding spiral tubes into its 5G base station designs. By selecting a multi-layered, silver-plated beryllium copper design, engineers achieved:
- A reduction in signal crosstalk by over 90 dB.
- Improved RF connector reliability in outdoor, high-vibration environments.
- Enhanced network stability, leading to fewer dropped calls and data errors.
Field tests conducted under extreme weather conditions confirmed that the upgraded shielding components provided consistent performance even under rapid temperature fluctuations and high humidity.
7.2 Advanced Medical Imaging Systems
Case Study: MRI Cable Shielding
A major medical equipment manufacturer faced persistent challenges with image noise in its MRI systems. The integration of EMI shielding spiral tubes into the cable assemblies resulted in:
- A significant reduction in electromagnetic interference, leading to clearer images.
- Improved diagnostic reliability, as the devices produced consistently high-quality scans.
- Compliance with strict regulatory standards (ISO 13485) and successful passing of all electromagnetic compatibility tests.
Clinical evaluations reported a measurable improvement in diagnostic accuracy and patient outcomes, highlighting the importance of EMI shielding in high-stakes medical environments.
7.3 Semiconductor Fabrication Equipment
Case Study: Probe Station Enhancement
In a high-precision semiconductor fabrication facility, probe stations used for testing integrated circuits were experiencing reduced yields due to high-frequency crosstalk. The installation of miniaturized spiral tubes (diameter ≤0.5 mm) in the probe wiring led to:
- An increase in IC test yields by over 15%.
- Improved measurement accuracy, enabling finer process control.
- Compatibility with Class 1 cleanroom standards, ensuring that contamination levels remained within acceptable limits.
The success of this initiative underscores the critical role that EMI shielding plays in modern semiconductor manufacturing.
7.4 Aerospace and Satellite Systems
Case Study: Satellite Payload Protection
A satellite operator required EMI shielding components capable of withstanding the harsh conditions of space. By using radiation-resistant spiral tubes made from Hastelloy C-276 and applying advanced nickel plating, the following benefits were realized:
- Stable performance in the face of high-energy particle interference.
- Extended operational lifespan of the satellite’s sensitive payload.
- Compliance with stringent aerospace standards, including DO-160G and MIL-STD-810G.
The improved shielding resulted in more reliable data transmission and reduced in-orbit anomalies, demonstrating the effectiveness of spiral tubes in aerospace applications.
7.5 Automotive and Electric Vehicle Systems
Case Study: On-Board Charger and BMS Integration
An electric vehicle manufacturer faced challenges with electromagnetic interference in its on-board charging systems and battery management circuits. The integration of EMI shielding spiral tubes into these subsystems resulted in:
- Effective suppression of high-frequency noise from SiC/GaN power electronics.
- Enhanced reliability of battery state-of-charge estimations.
- Improved overall vehicle performance and safety through stable communication between charging stations and onboard systems.
Long-term testing confirmed that the EMI shielding components maintained their performance even under continuous dynamic loading and thermal cycling.
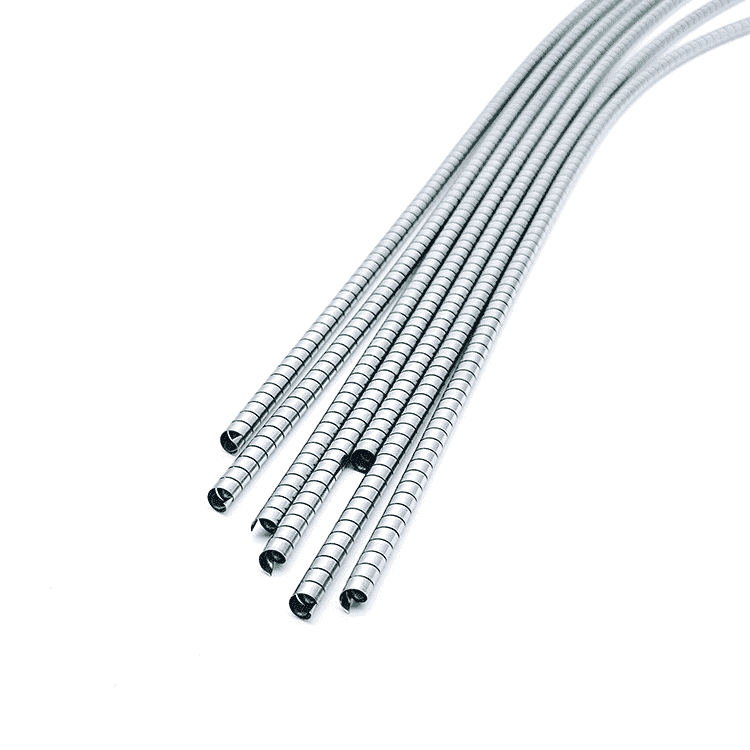
8. Comparative Analysis: Spiral Tubes vs. Alternative EMI Shielding Solutions
While EMI shielding spiral tubes offer many advantages, it is important to compare them with other EMI shielding approaches to understand their relative benefits and limitations.
8.1 Alternative EMI Shielding Technologies
Some of the common alternatives include:
- Conductive Fabrics: These materials are lightweight and flexible but often lack the robust mechanical properties and high-frequency performance of metallic spiral tubes.
- Metal-Coated Polymers: While these can provide adequate shielding for certain applications, they may not withstand high compression forces or extreme temperatures as effectively.
- Solid Metal Enclosures: These offer excellent EMI protection but are typically bulky and inflexible, making them unsuitable for many modern, miniaturized applications.
8.2 Advantages of EMI Shielding Spiral Tubes
Key advantages include:
- Design Flexibility: Their spiral geometry allows them to conform to various shapes and sizes.
- Mechanical Robustness: They offer superior resistance to bending fatigue and compression, even in dynamic environments.
- Customizability: Manufacturers can tailor material choices, plating options, and geometric parameters to meet specific application requirements.
- Broad Frequency Range: With proper design, these tubes provide effective shielding across a wide frequency spectrum, from low-frequency power line noise to high-frequency millimeter waves.
8.3 Limitations and Considerations
Despite their many benefits, spiral tubes also have limitations:
- Complex Manufacturing: High-precision manufacturing processes are required to maintain dimensional accuracy and consistent performance.
- Cost Factors: Advanced materials and plating processes can increase production costs, though these are often offset by the improved performance and reliability.
- Integration Challenges: In some applications, integrating a spiral tube into an existing design may require significant re-engineering.
A balanced evaluation shows that for high-performance and high-reliability applications—especially in aerospace, medical, and semiconductor fields—EMI shielding spiral tubes often provide the best overall solution despite their higher production costs.
9. Future Trends and Research Directions
9.1 Emerging Materials and Nanotechnology
Research continues to explore new materials that can enhance EMI shielding performance while reducing weight and cost. Nanomaterials, such as graphene and carbon nanotubes, are being studied for their potential to provide ultra-thin, high-conductivity layers that can be integrated with traditional metallic tubes. These developments could lead to next-generation EMI shielding solutions with even higher performance metrics.
9.2 Integration with Smart Manufacturing and IoT
As the industrial Internet of Things (IIoT) expands, the need for real-time monitoring of EMI shielding performance is growing. Future designs may incorporate embedded sensors within the spiral tubes to monitor parameters such as temperature, mechanical stress, and electromagnetic performance in real time. This “smart EMI shielding” could provide valuable data for predictive maintenance and performance optimization.
9.3 Miniaturization and High-Frequency Challenges
With the continuous push towards smaller electronic devices and higher operating frequencies (e.g., mmWave communications), manufacturers face challenges in maintaining effective EMI shielding as component sizes shrink. Advances in micro-forming techniques and precision plating are critical to overcoming these challenges. Research is also focusing on new geometries and multi-functional designs that combine EMI shielding with other roles such as thermal management and structural support.
9.4 Sustainability and Environmental Considerations
Sustainability is becoming an increasingly important factor in manufacturing. Future research may focus on developing EMI shielding materials that are more environmentally friendly, with lower energy consumption during production and improved recyclability. Compliance with evolving environmental regulations will drive innovation in both materials and production techniques.
9.5 Expanded Applications and Interdisciplinary Research
The evolution of EMI shielding technology is closely linked to advances in other fields such as materials science, nanotechnology, and electronics design. Interdisciplinary research is paving the way for new applications—ranging from wearable medical devices to high-speed autonomous vehicles—where robust EMI shielding is critical. Collaboration among academic institutions, industry leaders like Handa Shielding and Spira, and governmental agencies will likely yield even more innovative solutions in the coming years.
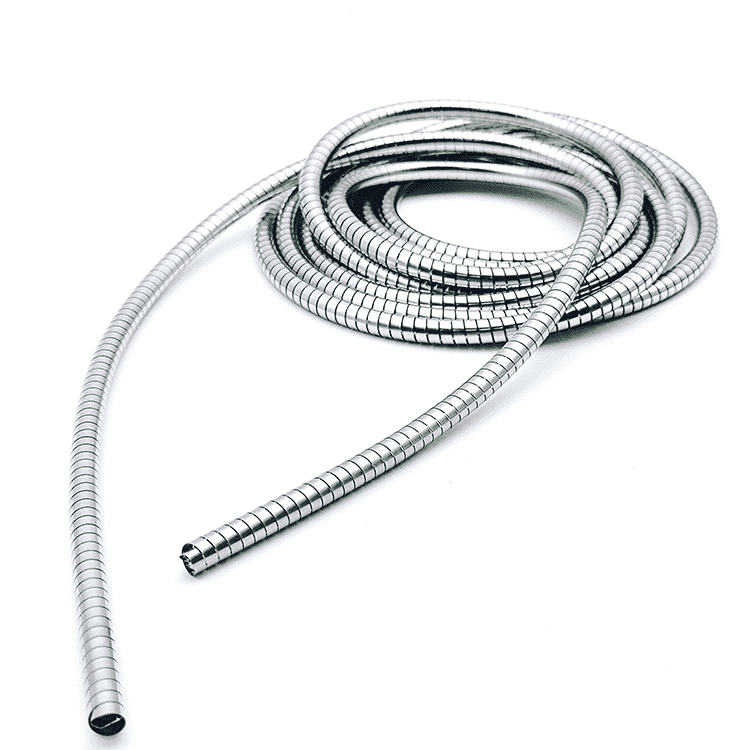
10. Conclusion
EMI shielding spiral tubes represent a critical advancement in the field of electromagnetic compatibility. Through decades of innovation—from the early days of simple metal enclosures to the state-of-the-art multi-layered, miniaturized designs of today—these components have evolved to meet the diverse and demanding requirements of modern technology.
This report has provided an extensive review of:
- The historical context and evolution of EMI shielding technologies.
- The fundamental principles underlying effective EMI shielding.
- Material innovations and structural designs that contribute to high performance.
- The sophisticated manufacturing processes and quality control measures that ensure reliability.
- The wide range of applications across communications, medical electronics, semiconductor manufacturing, industrial automation, aerospace, automotive systems, and consumer devices.
- Detailed case studies that demonstrate real-world benefits.
- A comparative analysis with alternative EMI shielding solutions.
- Future trends and research directions that promise to push the boundaries of what EMI shielding can achieve.
By combining high-performance materials, advanced manufacturing techniques, and precise design optimization, EMI shielding spiral tubes continue to be an indispensable solution for ensuring the reliability and integrity of sensitive electronic systems in increasingly challenging environments.
As industries continue to demand smaller, faster, and more robust electronic devices, the role of EMI shielding spiral tubes will only become more critical. Ongoing research, interdisciplinary collaboration, and continuous technological innovation will further enhance their performance, ensuring that future systems are well-protected against the ever-present challenges of electromagnetic interference.