EMIシールド用カンテッドコイルスプリングが長期高温用途の課題を克服する方法
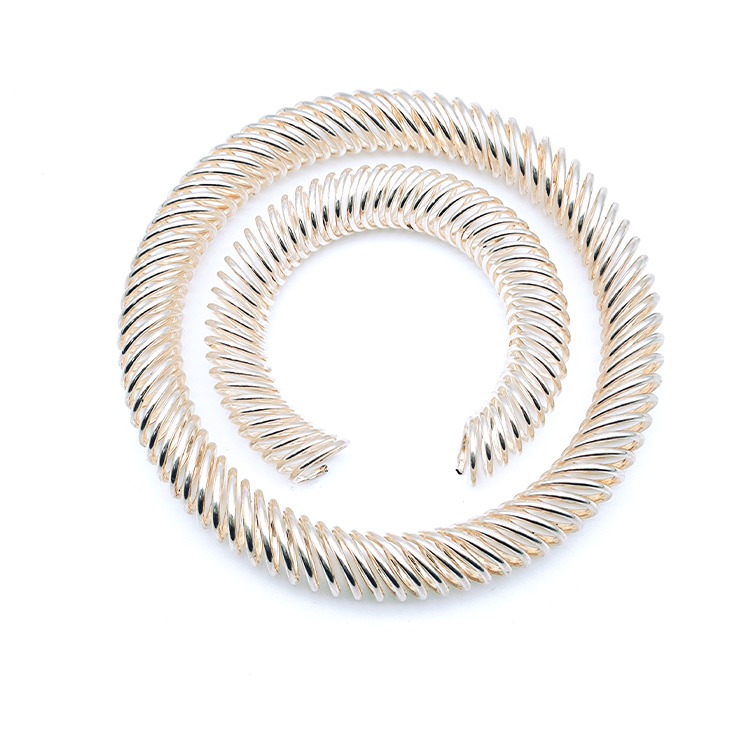
EMIシールド用コイルスプリング
目次
1.はじめに
今日の高性能電子システムでは、シグナル・インテグリティを維持し、電磁干渉(EMI)を防止することが極めて重要です。 コイルスプリング EMIシールド用コイルは、堅牢なEMI/RFIシールドを提供するだけでなく、機械的ラッチ、電気伝導、および接地機能を提供する革新的なソリューションとして登場しました。個々のコイルが正確な角度に設定された独自の傾斜コイル構成により、複数の接触点が確保され、広い偏向範囲にわたってほぼ一定の力が伝達されます。
1.1.EMIシールド用キャントコイルスプリングの概要
EMIシールド用カントコイルスプリング は従来のスプリングとは著しく異なります。ベリリウム銅、ジルコニウム銅、タングステン銅のような高品質の合金で設計され、電気的性能と耐腐食性を高めるために高度なメッキオプション(銀、金、ニッケル、スズ)が施されています。この多機能部品は、以下のように設計されています:
- 敏感な電子機器をシールドする: 連続的で低抵抗の電気経路を提供することにより、これらのスプリングは広い周波数範囲にわたって放射と伝導の両方のEMIを減衰させます。
- 機械的完全性を維持する: スプリング作用により、衝撃、振動、ミスアライメント下でも安定した接触圧が得られ、これは高負荷のかかる用途に不可欠です。
- 効率的な接地と導通を可能にする: EMIシールド用カンテッドコイルスプリングは、シグナルインテグリティとシステム信頼性の両方をサポートする優れた電気的性能を提供します。
1.2.長期高温運転の課題
高温環境(多くの場合、最高200℃以上)では、材料と設計に厳しい要求が課せられます。時間の経過とともに、部品には以下のような問題が生じます:
- 素材の劣化: 酸化、脆化、導電性の損失。
- 熱膨張: 膨張の差は、隙間や一貫性のない接触圧につながります。
- 電気抵抗の増加: 高温はメッキや芯材の性能に悪影響を及ぼす可能性がある。
- 機械的疲労: 熱サイクルを繰り返すと永久変形を起こし、寿命が短くなる。
この記事では、EMIシールド用キャントコイルスプリングが、これらの課題を克服し、信頼性の高い長期的な性能を確保するために、どのように綿密に設計され、設計されているかについて詳しく説明します。
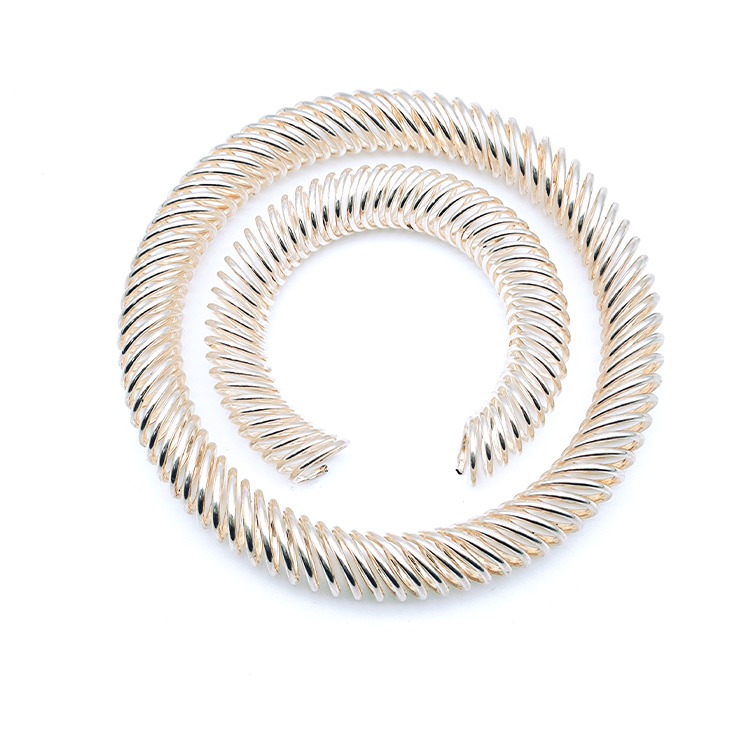
2.EMIシールド用コイルスプリングの用途
EMIシールド用キャントコイルスプリングの汎用性は、多くの産業で不可欠なものとなっています。以下では、その主な応用分野について説明します:
2.1.高圧電源装置
ガス絶縁開閉装置(GIS)や高電圧サーキットブレーカでは、キャントコイルスプリングは大電流負荷や動的条件下で可動部品間の安定した接触を維持するために使用されます。広い撓み範囲での動作が可能なため、電力機器の静的接点と動的接点の両方を管理するのに理想的です。
2.2.鉄道輸送
高速列車や地下鉄を含む最新の鉄道システムでは、車載電気システムに信頼性の高いEMIシールドが必要です。EMIシールド用カンテッドコイルスプリングはコネクターやアース部品に組み込まれ、高速輸送中に発生する高い振動、衝撃、急激な温度変化にも安定した性能を発揮します。
2.3.新エネルギー自動車
電気自動車やハイブリッドプラットフォームは、バッテリーパック接続部、モーターコントローラーインターフェイス、その他の重要な電気接続部におけるEMIシールドのためにカントコイルスプリングを統合することで恩恵を受けます。その堅牢なEMIシールド特性は、頻繁な熱サイクルや機械的衝撃に耐えながら、大電流を効率的に伝導することを保証します。
2.4.石油探査と医療機器
石油探査では、ダウンホールツールは高圧、高温環境下で中断のない電気接続を維持する必要があります。同様に、手術器具や診断機器のような医療機器では、EMIシールド用カントコイルスプリングは、滅菌サイクルの繰り返しや過酷な化学薬品にさらされた後でも、信頼性の高いEMIシールドと電気伝導を提供します。
3.材料の選択とコーティング設計
EMIシールド用キャントコイルスプリングで最適な性能を達成するには、コア材と表面メッキのバランスを慎重に取る必要があります。エンジニアはいくつかの主要な合金を比較し、高温でEMIが重要な用途に最適な合金を決定します。
3.1.コア素材の比較
素材 | 電気伝導率 | 機械的強度 | 耐熱温度 | 代表的なアプリケーション |
---|---|---|---|---|
ベリリウム銅 | 高い | 非常に高い | 200℃まで | 高電圧スイッチ、高周波EMIシステム |
ジルコニウム銅 | 中程度 | 中程度 | 150℃まで | 自動車用バッテリーコネクター、中負荷用途 |
タングステン 銅 | より低い | 極めて高い | 300℃まで | 超高温用途、高摩耗 |
ベリリウム銅はその優れた導電性と強度の組み合わせから広く使用されており、高温下でのほとんどのEMIシールドのニーズに理想的です。ジルコニウム銅とタングステン銅は、それぞれ適度な温度耐性か極端な高温性能を必要とする特殊な用途に選ばれます。
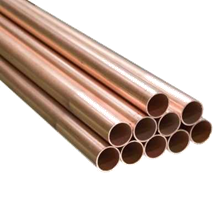
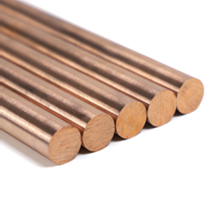
3.2.コーティングの選択肢と推奨事項
表面めっきは、導電性を維持し、芯材を酸化や摩耗から保護する上で重要な役割を果たしている。
- 銀メッキ: 超低接触抵抗(<0.5 mΩ)と卓越した導電性により、高周波EMIアプリケーションに最適。
- 金メッキ: 耐食性に優れ、医療機器や高湿度環境に適しています。
- ニッケルめっき: 他のメッキの密着性を高めるために下地層として使用されることが多く、全体的な耐久性も向上する。
- 錫メッキ: あまりアグレッシブでない環境において、導電性と腐食保護のバランスをとる経済的なオプション。
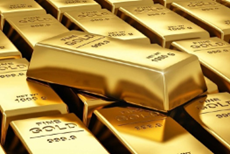
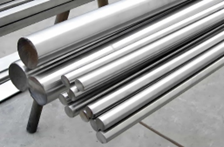
4.複雑な環境に対するエンジニアリング・デザイン・ソリューション
長期間の高温環境下で信頼性の高い性能を確保するために、EMIシールド用カントコイルスプリングは、材料と構造の両方を考慮して設計する必要があります。
4.1.高温環境 (≤200℃)
素材とコーティングの最適化
- コア素材: 200℃までの温度では、高い導電性と機械的弾力性を持つベリリウム銅が一般的に選択される。
- メッキ戦略: 二重層システム(例えば、ニッケル下地と銀めっき)は、優れた表面導電性を確保し、コアを酸化から保護する。
構造設計の強化
- 複数のコンタクトポイント: 傾斜したコイル構成は、複数の独立した接点を提供し、電気的負荷を分散させ、局所的な発熱を最小限に抑える。
- 熱シミュレーション: 有限要素解析(FEA)を用いて熱応力をモデル化し、熱膨張にもかかわらず接触圧を一定に保つためにコイル形状(傾斜、幅、間隔)を最適化する。
- 放熱機能: スプリングの設計にマイクロフィン構造と追加の導電経路を組み込むことで、効果的な熱放散を助けます。
4.2.高周波と大電流の安定性の最適化
13MHzまでの周波数と16Aの電流での動作を必要とするアプリケーション向け:
- 銀メッキ: 表皮効果による損失を最小限に抑え、高周波で有効伝導面積が最大になるようにする。
- 平行伝導経路: 独立したコイルは並列に動作するように設計されており、均一な電流分布を確保し、局所的なホットスポットを減少させる。
- インピーダンス・チューニング: スプリングの形状(コイルの角度、幅、間隔)は、最適なシグナル・インテグリティのために望ましいインピーダンスを達成するように細かく調整されている。
4.3.長期にわたる変形と疲労の防止
長期的な信頼性を確保するためには、厳しい疲労試験と設計の改良が必要である:
- 挿抜サイクル試験: プロトタイプは、永久変形が3%を下回ることを保証するために、10万回以上のサイクルが行われる。
- CAEシミュレーション 高度なコンピュータ支援エンジニアリング(CAE)モデルは、繰り返し荷重下での応力分布と変形を予測します。
- マテリアル・トリートメント: 最適化された熱処理と制御されたアニール処理により、内部応力を低減し、クリープや永久変形を防ぎます。
5.試験方法と性能検証
長期の高温条件下でのEMIシールド用カンテッドコイルスプリングの性能を検証するためには、堅牢な試験プロトコルが不可欠です。
5.1.機械的性能試験
接触圧測定
- 力センサー: 精密センサーは、接触点ごとに力を測定し、コイルあたり0.5~1Nの目標値を±1Nの公差で保証します。
- 均一性試験: すべての接点が均一な圧力を保つようにすることは、局所的な故障を防ぐために非常に重要である。
サイクルテスト
- 挿抜サイクル: 力の減衰と永久変形を監視するため、10万サイクル以上の模擬運転試験が実施される。
- 振動・衝撃試験: スプリングは、機械的安定性と耐久性を検証するために、制御された振動と衝撃荷重にさらされる。
5.2.電気性能試験
接触抵抗測定
- 4線式ケルビン法: 低接触抵抗を正確に測定するために採用され、銀メッキ条件下でも1mΩ以下を維持する。
- 周波数応答テスト: EMIシールド効果を確認するため、100MHzから10GHzの周波数でスプリングの性能をテスト。
温度上昇と熱サイクル
- 赤外線サーモグラフィ 全負荷状態(例:16A)での温度上昇を監視し、30℃以下の上昇を目標とする。
- 熱サイクル試験: 加熱と冷却のサイクルを繰り返すことで、実際の使用条件をシミュレートし、長期的な信頼性を検証します。
5.3.ミスアライメントと公差変動への対応
アダプティブ・デザインの特徴
- 公差補償: 独立したコイル設計により、わずかなズレや表面の凹凸を本質的に補正し、安定した接触を維持します。
- CAEの検証: 詳細なシミュレーションにより、±0.5mmまでの公差があっても性能を維持できることが確認されている。
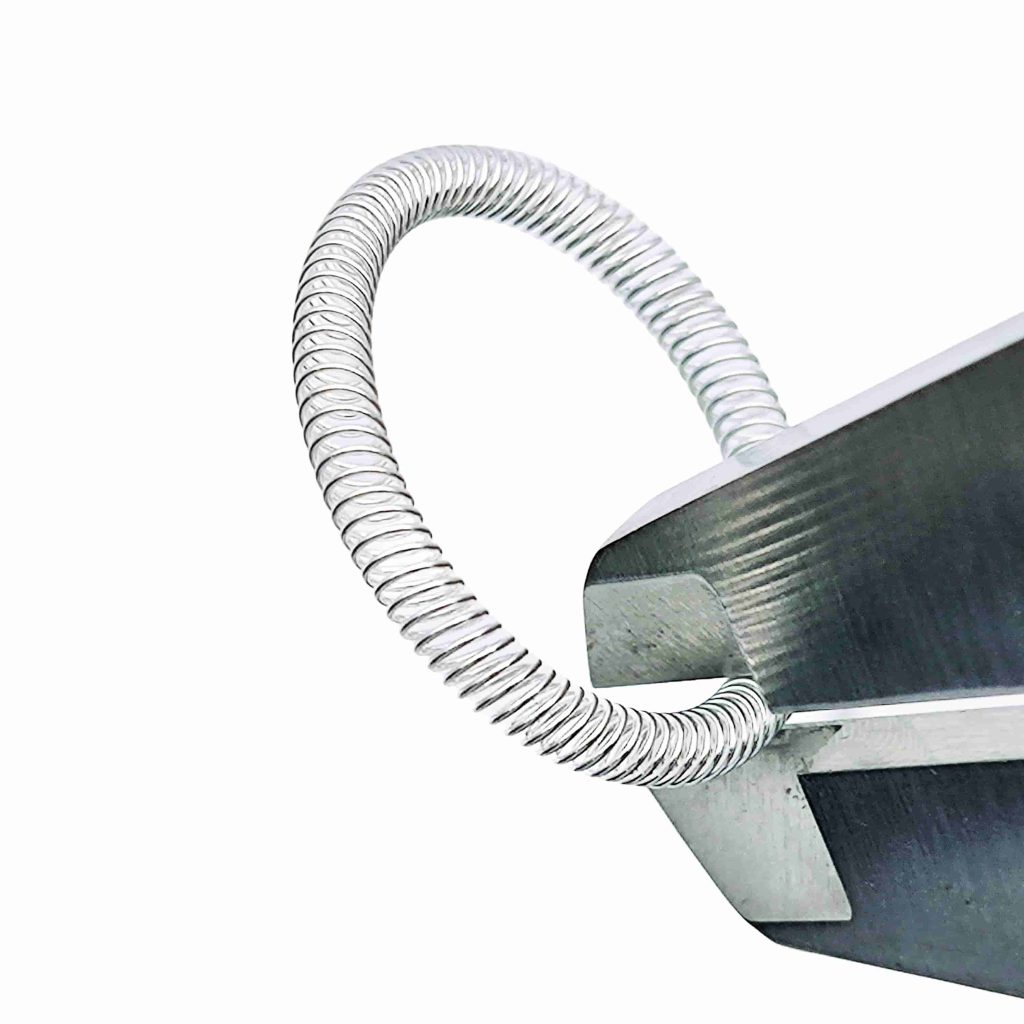
6.ケーススタディと現場での応用
実際の事例がその有効性を示している。 EMIシールド用カントコイルスプリング 長時間の高温環境下で
6.1.変電所の高圧開閉装置
概要
高電圧開閉器では、可動部と固定部の確実な接触が安全性と性能に不可欠です。ベリリウム銅に銀メッキを施したEMIシールド用カントコイルスプリングは安定した電気接触とEMIシールドを提供します。
結果
- 広範な熱的・機械的サイクル試験後も、接触抵抗は1mΩ以下を維持した。
- FEAモデルでは、熱膨張による隙間形成が最小限に抑えられ、10万サイクルにわたって安定した性能を維持できることが確認された。
6.2.高速鉄道システムにおけるEMIシールド
概要
鉄道輸送システムは部品が高い振動と衝撃荷重にさらされます。コネクタアセンブリに統合されたEMIシールド用カントコイルスプリングは、重要な制御システムに安定したEMIシールドとアースを提供します。
結果
- このスプリングは、高速の動的テストでも安定した性能を維持し、EMI減衰の劣化はごくわずかであった。
- 詳細な熱解析の結果、マルチポイント接触設計が効果的に熱を分散させ、局所的なホットスポットを防いでいることがわかった。
6.3.新エネルギー自動車における熱的・機械的安定性
概要
電気自動車はバッテリーパックとモーターコントローラー間の強固な接続を必要とします。EMIシールド用カンテッドコイルスプリングは、繰り返される熱サイクルや機械的衝撃に耐えながら、低抵抗で信頼性の高い電気経路を維持するために使用されます。
結果
- 実環境をシミュレートした10万サイクル試験では、永久変形は3%未満であった。
- 高周波テストでは、インピーダンスが規定の範囲内に収まっていることが確認され、最適な性能が保証された。
6.4.繰り返し滅菌における医療機器の信頼性
概要
手術器具や診断機器などの医療機器は、電気的接続とEMIシールドを維持しながら、厳しい滅菌サイクルに耐えなければなりません。金メッキを施したベリリウム銅製のEMIシールド用カンテッドコイルスプリングはこれらのシステムに組み込まれています。
結果
- 100,000回の滅菌サイクル(高温オートクレーブと化学薬品への暴露を含む)の後、スプリングは2mΩ以下の接触抵抗を維持した。
- EMIテストでは、シールド効果が一定であることが確認され、患者の安全と機器の信頼性が確保された。
7.顧客の懸念への対応と品質保証
OEMやエンドユーザーの期待に応えるには、性能、耐久性、信頼性に関する特定の懸念に対処する必要がある。
7.1.接続安定性の検証
- CAEと実証データ: 包括的なシミュレーション・レポートと経験的なテスト・データ(挿入/引き抜きサイクル、接触力の減衰など)を組み合わせることで、安定した一貫した性能を明確に証明することができます。
- テスト資格: 第三者機関による試験報告書(MIL、SAE、IEC規格)は、設計が厳しい業界要件に準拠していることを証明します。
7.2.高温性能保証
- 素材とコーティングの相乗効果: 銀(または金)メッキを施したベリリウム銅の使用により、スプリングは200℃までの温度で確実に作動し、実際のテストでは全負荷条件下で50℃以下の温度上昇しか示していない。
- サーマルイメージングの検証: 赤外線サーモグラフィは、スプリングの表面全体に均一な温度分布を確認し、局所的な過熱を防ぎます。
7.3.長期変形制御
- 疲労試験とライフサイクル試験: 厳密な疲労試験(100,000サイクルを超える)により、永久変形は3%未満にとどまり、長期信頼性が確保されていることが実証されている。
- 最適化された設計パラメータ: コイルの形状と材料処理(制御されたアニールなど)を継続的に改良することで、クリープを最小限に抑え、弾力性を高めることができる。
7.4.高周波適応性とインピーダンス・チューニング
- カスタマイズ可能なデザイン: エンジニアは、コイルの角度、間隔、メッキの厚さを調整することで、特定の高周波アプリケーション(例えば、抵抗変動5%未満で13MHz動作)に必要なインピーダンスを達成することができる。
- 安定したパフォーマンス: テストでは、スプリングが広い圧縮範囲でほぼ一定の力を発揮することが確認されており、変動荷重下で安定した電気特性を維持するために重要である。
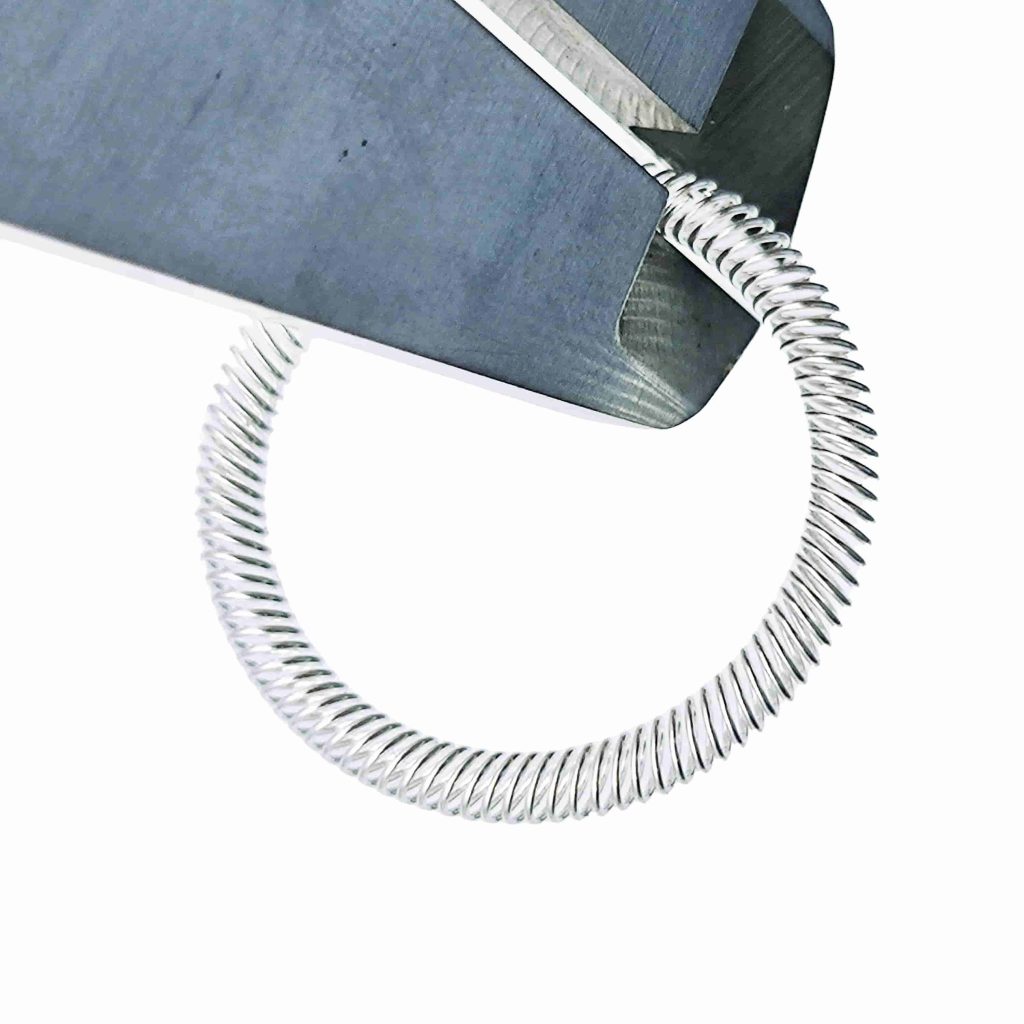
8.今後の動向と研究の方向性
技術と業界の要求が進化するにつれて、継続的な研究開発により、EMIシールド用キャントコイルスプリングの性能はさらに強化されるでしょう。
8.1.EMIシールドのための材料科学の進歩
- 新しい合金と複合材料: 先進的な銅合金と複合材料の研究により、EMI シールド用のキャントコイルスプリングの熱特性と電気特性の両方が改善されることが期待されます。
- ナノ材料の統合: ナノマテリアルを組み込むことで、導電性と耐摩耗性を向上させながら、軽量化できる可能性がある。
8.2.スマート・センシングの統合
- 組み込みセンサー: 将来の設計では、バネ構造内にマイクロセンサーを組み込んで、接触抵抗、温度、機械的応力をリアルタイムでモニターできるようになるかもしれない。
- 予知保全: このようなスマートな統合によって予知保全が可能になり、故障が発生する前に性能低下の可能性をユーザーに警告することができる。
8.3.持続可能でリサイクル可能な素材ソリューション
- 環境に優しい素材: 環境規制が強まるにつれ、持続可能でリサイクル可能な素材(リサイクル可能なクリーン銅の代替品など)の開発が優先されるようになるでしょう。
- グリーン製造プロセス: 製造技術の進歩は、高性能を維持しながら環境への影響を減らすことに焦点を当てるだろう。
8.4.カスタマイズとモジュラー設計
- アプリケーションに特化した設計: モジュラー設計により、独自の環境要件や性能要件に迅速に対応できるようになる。
- 統合ソリューション: EMIシールドと他の機能(シーリング、アースなど)を単一の部品で組み合わせることで、設計を簡素化し、システムの複雑さを軽減することができる。
9.結論
EMIシールド用カンテッドコイルスプリングは、現代の電子システム、特に長期の高温アプリケーションにおいて最も要求の厳しい課題に対応する洗練された多機能ソリューションです。高性能材料の慎重な選択、高度なコーティング技術、最適化された構造設計により、これらのスプリングは、過酷な条件下でも信頼性の高いEMI/RFIシールド、堅牢な電気伝導、安定した機械的接続を実現します。
包括的な試験とシミュレーションデータは、広範囲な熱サイクルと機械的ストレスに対して一貫した性能を維持する能力を裏付けています。高電圧の電力機器、鉄道輸送システム、新エネルギー自動車、重要な医療機器など、EMIシールド用カントコイルスプリングは、今日の高度な電子機器が要求する信頼性と精度を提供します。
産業界が性能の限界に挑戦し続ける中、スマートセンシング、持続可能な材料、モジュラー設計の統合は、これらのスプリングの能力をさらに高め、将来にわたってEMIシールドソリューションの最前線に留まることを保証します。