EMI Shielding Spiral Tube Gaskets
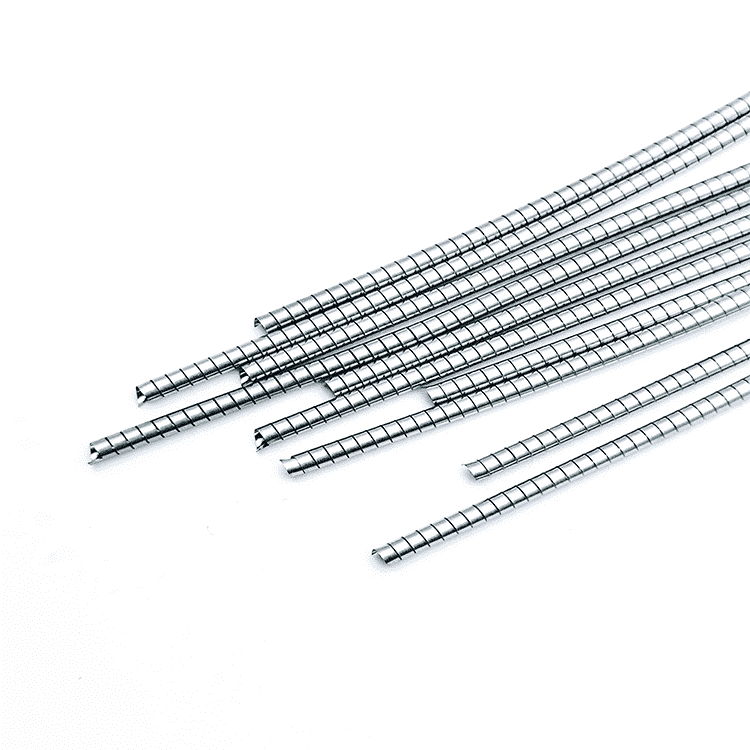
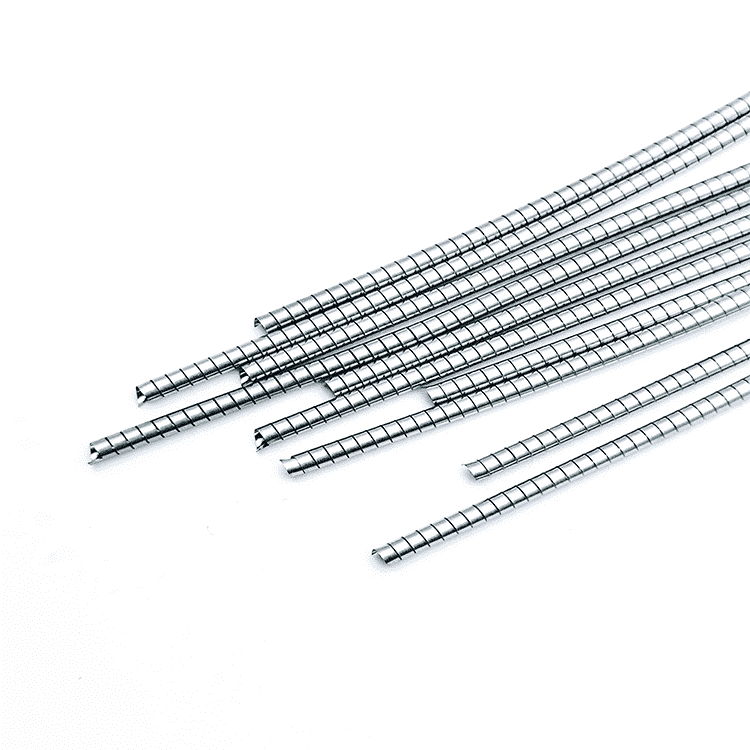
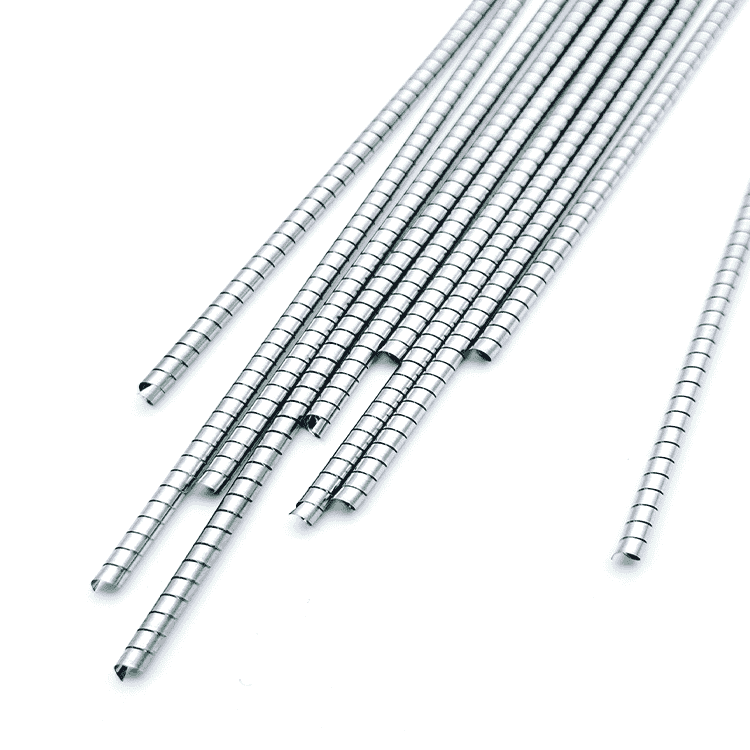
EMI shielding spiral tube gaskets are typically constructed from materials that offer both electrical conductivity and mechanical flexibility. These gaskets are designed to create a secure seal between surfaces, preventing electromagnetic waves from penetrating and interfering with electronic operations. However, in environments where moisture, chemicals, or extreme temperatures are present, the materials used in these gaskets can corrode, leading to failure in performance.
EMI (Electromagnetic Interference) shielding spiral tube gaskets are critical components in many electronic and industrial applications, designed to protect sensitive equipment from electromagnetic interference while also maintaining structural integrity in challenging environments. One of the primary concerns with these gaskets is their susceptibility to corrosion, which can compromise their effectiveness and longevity. This article explores strategies to enhance the corrosion resistance of EMI shielding spiral tube gaskets, focusing on material selection, surface treatments, design optimization, and maintenance practices.
Table of Contents
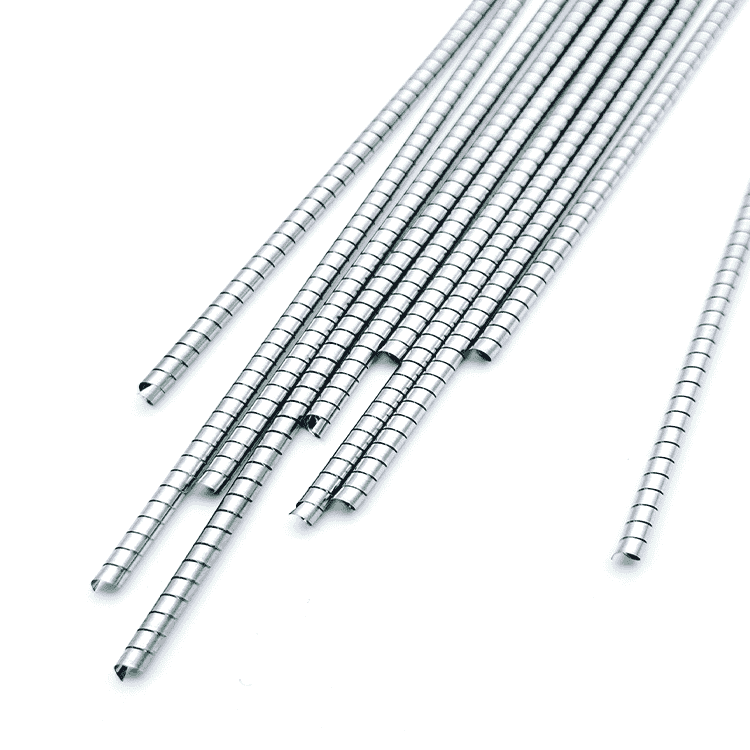
EMI Shielding Spiral Tube Gaskets
Understanding EMI Shielding Spiral Tube Gaskets
EMI shielding spiral tube gaskets are engineered to create a reliable seal between two surfaces, preventing electromagnetic waves from penetrating and interfering with the operation of electronic devices. They are typically made from conductive materials that offer both mechanical flexibility and electrical conductivity. However, the presence of moisture, chemicals, or extreme temperatures can lead to corrosion, undermining their effectiveness. Thus, enhancing corrosion resistance is essential for ensuring their longevity and performance.
Functionality and Importance
EMI shielding spiral tube gaskets serve multiple functions, including:
- Electromagnetic Shielding: They block unwanted electromagnetic radiation, preventing signal interference.
- Environmental Sealing: They protect against dust, moisture, and other contaminants.
- Mechanical Stability: They maintain structural integrity under various operating conditions.
In sectors such as aerospace, telecommunications, and medical devices, the reliability of these gaskets is paramount. Corrosion can compromise not only the gasket itself but also the devices it protects, potentially leading to costly failures and repairs.
Material Selection
The selection of materials is fundamental to enhancing the corrosion resistance of EMI shielding spiral tube gaskets. Choosing the right materials can significantly impact the durability and performance of these gaskets in adverse environments.
Stainless Steel Options
Stainless steel is a popular choice for EMI shielding spiral tube gaskets due to its mechanical strength and corrosion resistance. Among the various grades of stainless steel, 316L stainless steel is often recommended for applications in saline or humid environments. This alloy contains molybdenum, which provides excellent resistance to pitting and crevice corrosion.
Benefits of 316L Stainless Steel
- High Corrosion Resistance: The addition of molybdenum enhances resistance to chlorides and other corrosive agents.
- Strength and Durability: 316L maintains its mechanical properties even in high-stress conditions.
- Ease of Fabrication: This stainless steel can be easily formed into complex shapes, making it ideal for intricate gasket designs.
Corrosion-Resistant Alloys
In addition to stainless steel, other corrosion-resistant alloys can be beneficial. Inconel and Hastelloy are high-performance materials engineered to withstand extreme conditions. They provide excellent protection against a wide range of corrosive substances, making them suitable for highly demanding applications.
Advantages of Using Corrosion-Resistant Alloys
- Extended Lifespan: These materials can endure harsh environments that would rapidly degrade standard materials.
- Versatility: Suitable for a variety of applications, from aerospace to chemical processing.
- Thermal Stability: They maintain performance at high temperatures, ensuring reliability in extreme conditions.
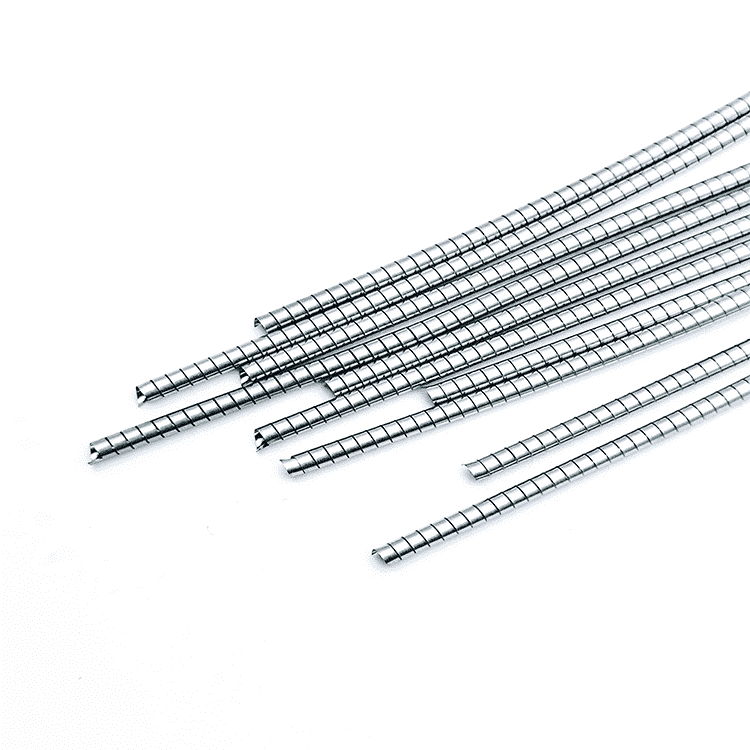
Surface Treatments
Surface treatments significantly enhance the corrosion resistance of EMI shielding spiral tube gaskets. By applying protective coatings or treatments, manufacturers can create barriers that prevent corrosive agents from affecting the base material.
Electroplating
Electroplating involves depositing a thin layer of a more corrosion-resistant metal onto the surface of the gasket. Nickel plating is particularly effective, as it improves resistance to salt spray corrosion, making it ideal for marine and coastal applications. Other metals, such as chrome or gold, can also be used depending on specific environmental requirements.
Advantages of Electroplating
- Improved Corrosion Resistance: A thin layer of nickel or chrome can significantly extend the service life of the gasket.
- Enhanced Aesthetic Appeal: Electroplating can provide a shiny, appealing finish.
- Low Friction: Electroplated surfaces often exhibit reduced friction, which can improve the performance of the gasket.
Passivation
Chemical passivation is another effective method to enhance corrosion resistance. This process creates a thin, protective oxide layer on the surface of stainless steel, which minimizes the penetration of corrosive agents. Passivated surfaces are less likely to rust or corrode, ensuring longer-lasting performance.
Benefits of Passivation
- Increased Durability: Passivated surfaces resist corrosion better than untreated materials.
- Improved Cleanliness: The passivation process helps to remove contaminants that can lead to corrosion.
- Cost-Effective: This treatment is relatively inexpensive compared to other surface enhancement methods.
Protective Coatings
Applying protective coatings can further enhance corrosion resistance. Options such as epoxy resins, polyurethane, or Teflon can provide an additional physical barrier against moisture and corrosive gases. These coatings can be particularly effective in preventing direct contact between corrosive agents and the metal substrate.
Advantages of Protective Coatings
- Enhanced Physical Barrier: Coatings can prevent moisture and chemicals from reaching the base material.
- Customizable: Different coatings can be tailored to meet specific environmental requirements.
- Thermal and Chemical Resistance: Many coatings can withstand high temperatures and a variety of chemicals.
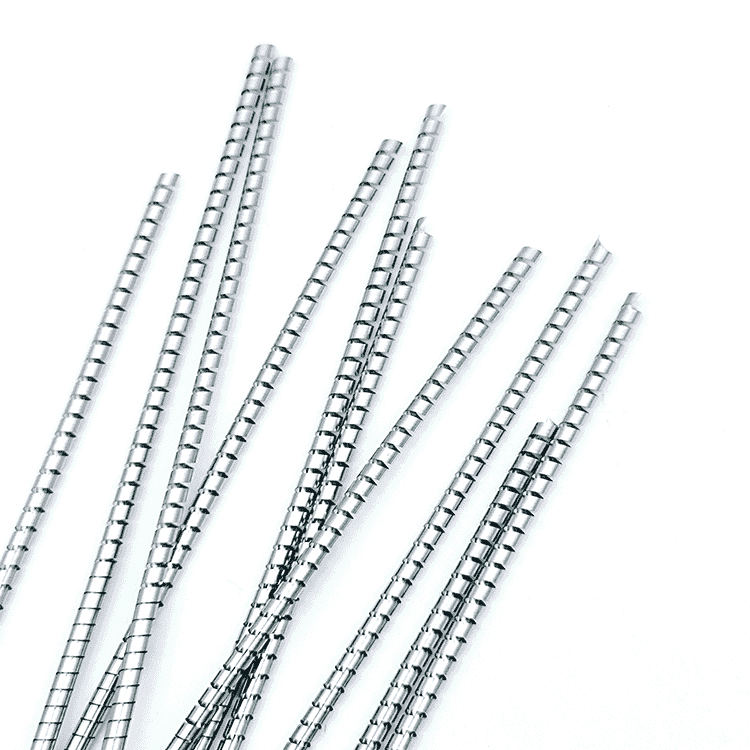
Design Optimization
Optimizing the design of EMI shielding spiral tube gaskets can contribute to improved corrosion resistance. A thoughtful approach to design can minimize the potential for corrosion to occur.
Sealing Design
Ensuring a proper seal at the interfaces of the spiral tube gasket is vital. The use of additional sealing rings or adhesives can help prevent moisture and corrosive gases from infiltrating the system. A well-designed gasket will fit tightly and distribute mechanical stress evenly, reducing the likelihood of corrosion at stress concentration points.
Importance of Sealing Design
- Prevention of Infiltration: A tight seal reduces the risk of corrosive agents entering the system.
- Enhanced Performance: Proper sealing improves overall gasket effectiveness.
- Increased Lifespan: Effective sealing can prolong the life of both the gasket and the equipment it protects.
Structural Design
The geometric shape of EMI shielding spiral tube gaskets should be carefully considered. Reducing sharp edges and points where stress can concentrate minimizes the risk of corrosion. Rounded designs help distribute stress more evenly, enhancing the overall durability of the gasket.
Benefits of Structural Design Optimization
- Reduced Stress Concentration: Optimized designs help minimize areas susceptible to corrosion.
- Improved Mechanical Performance: A well-structured gasket will perform better under varying loads.
- Longevity: Enhancing structural integrity can significantly extend the service life of the gasket.
Environmental Testing
Conducting environmental adaptability tests, such as salt spray tests or humidity exposure tests, provides valuable insights into the gasket’s corrosion resistance. These tests simulate harsh conditions and can help identify potential weaknesses in the design, allowing for necessary adjustments before production.
Value of Environmental Testing
- Early Detection of Weaknesses: Testing can reveal design flaws that may lead to corrosion.
- Verification of Performance: Results from tests confirm the gasket’s effectiveness under expected operating conditions.
- Continuous Improvement: Insights from testing can inform future design iterations.

Composite Materials
Combining stainless steel with other materials can yield superior corrosion resistance. Composite materials, such as those incorporating corrosion-resistant plastics or ceramics, can enhance the overall performance of EMI shielding spiral tube gaskets. These composites leverage the strengths of different materials to achieve better resistance to environmental stressors.
Advantages of Composite Materials
- Enhanced Performance: Composites can outperform traditional materials in specific environments.
- Weight Reduction: Using lightweight composite materials can reduce overall equipment weight.
- Cost Efficiency: While initial costs may be higher, the long-term benefits can outweigh the investment.
Maintenance and Care
Regular maintenance is essential for prolonging the life of EMI shielding spiral tube gaskets and ensuring optimal performance. Implementing a routine inspection and cleaning schedule can significantly enhance corrosion resistance.
Inspection
Routine inspections should focus on identifying early signs of corrosion, such as discoloration or surface pitting. Early detection can prevent more extensive damage and prolong the gasket’s lifespan.
Importance of Regular Inspection
- Preventative Action: Identifying issues early can lead to prompt repairs or replacements.
- Cost Savings: Regular inspections can reduce the need for costly emergency repairs.
- Operational Reliability: Maintaining the integrity of the gasket ensures continuous protection against EMI.
Cleaning
Maintaining clean surfaces is crucial for preventing corrosion. Regular cleaning to remove dirt, moisture, and corrosive residues can help maintain the integrity of the gasket. Using mild detergents and soft brushes effectively removes contaminants without damaging the surface.
Benefits of Regular Cleaning
- Enhanced Lifespan: Clean surfaces are less prone to corrosion.
- Improved Performance: Reducing contaminants enhances the gasket’s effectiveness.
- Safety: Maintaining cleanliness can prevent accidents related to equipment failure.
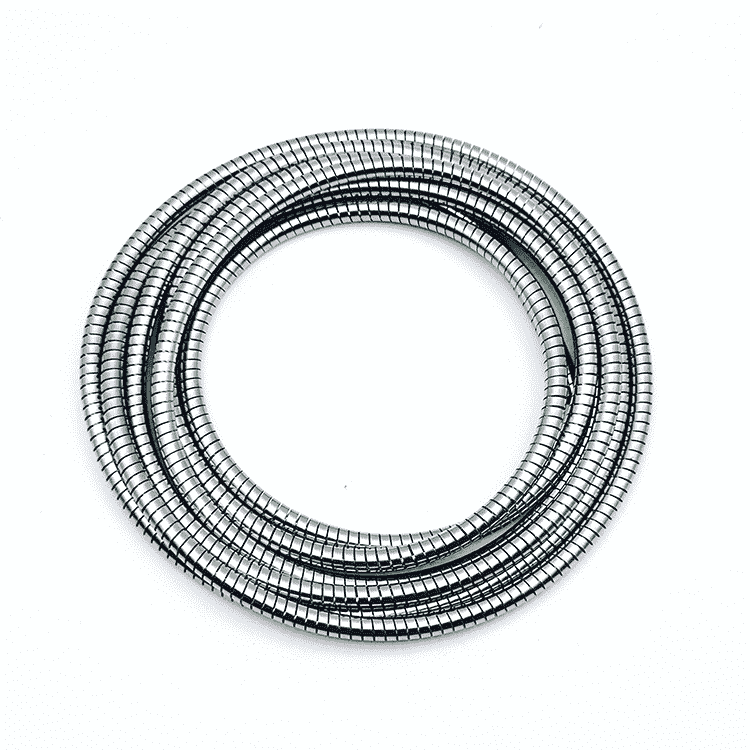
Conclusion
EMI shielding spiral tube gaskets are vital components in protecting electronic devices from electromagnetic interference. Enhancing their corrosion resistance through careful material selection, effective surface treatments, optimized design, and regular maintenance is crucial for ensuring their longevity and performance. By implementing these strategies, manufacturers can create durable, reliable gaskets that withstand harsh environmental conditions while providing effective EMI shielding.
As industries continue to demand more from their materials, the importance of advanced corrosion resistance techniques will only grow. With ongoing innovations in materials science and engineering, the future of EMI shielding spiral tube gaskets looks promising, offering enhanced protection and performance for critical electronic applications.
You May Also Like
-
Shielding Gasket Solutions and Materials
Electrically conductive foam
Electrically conductive foam is an innovative material designed to combine the softness, flexibility, and compressibility of traditional foam with the ability to conduct electricity. This unique combination of properties makes conductive foam ideal for a variety of industries where both......
-
Handa Canted Coil Springs
Electrical conducting springs
conductive contact finger springs /conducting canted coil springs The Challenge of Maintaining Reliable ConductivityConductive Contact Finger Springs: A Reliable SolutionConsistent Force Across Wide Deflection RangeMultiple Contact Points for Reliable ConductivitySuperior Conductive PropertiesEfficient Heat ManagementEMI/RF Shielding CapabilitiesSupporting SWaP (Space, Weight, and......
-
Fingerstrips
Beryllium-copper fingerstrips series
https://www.handashielding.com/contact-us.html Handa Beryllium-Copper Fingerstrips/Fingerstocks with a variety of benefits Introduction to Handa Beryllium-Copper Fingerstrips/FingerstocksOverview of Beryllium-Copper as a MaterialKey Features of Handa Beryllium-Copper Fingerstrips/FingerstocksApplications of Handa Beryllium-Copper Fingerstrips/FingerstocksAdvantages of Using Handa Beryllium-Copper Fingerstrips/FingerstocksInstallation and Best PracticesConclusion Introduction to Handa Beryllium-Copper......
-
EMI/EMC Shielding | RFI Shielding | EMI Gaskets
Handa Shielding offers various types of shielding products. These products come in different shapes and materials, and they each have their own unique function. In this article, we will take a look at the EMI shielding aspect and explore the......
-
EMI/EMC Shielding | RFI Shielding | EMI Gaskets
Handa Endur Shield is a premium electromagnetic interference (EMI) and radio frequency interference (RFI) shielding solution designed to safeguard sensitive electronic equipment from external interference. As the world becomes increasingly reliant on electronics, particularly in critical industries like telecommunications, aerospace,......