Durable and Lightweight Electrically Conductive Foam for Superior EMI Protection
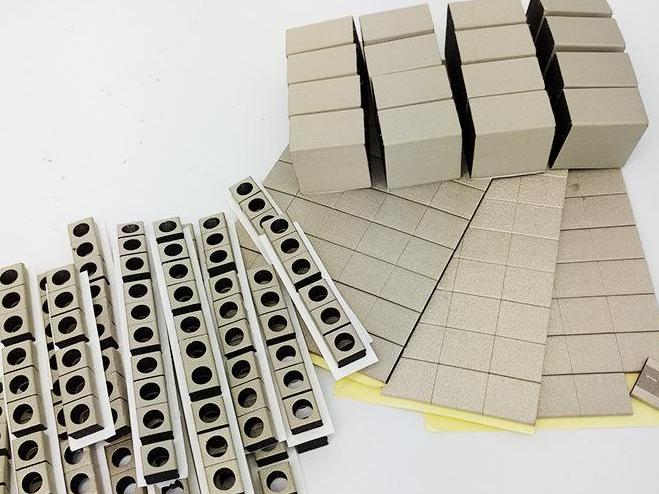
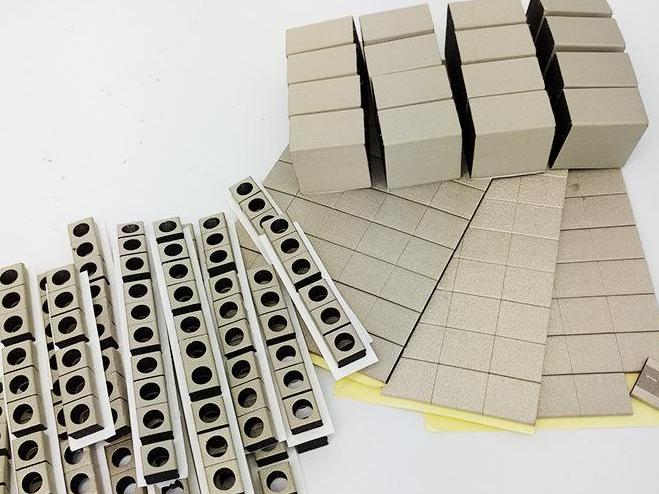
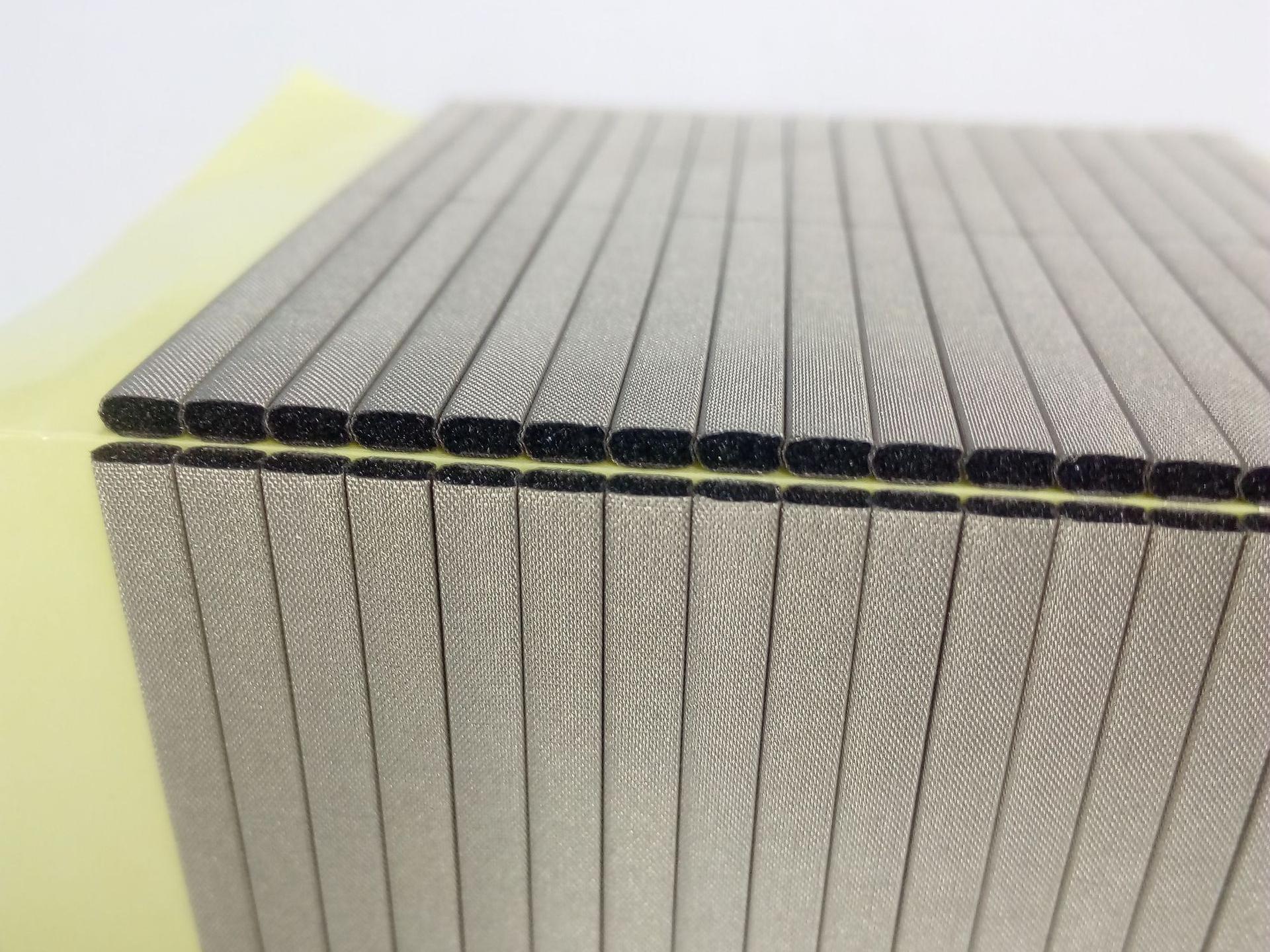
Electrically conductive foam, often described as a porous material composed of rubber matrix embedded with conductive fillers, provides the ideal combination of lightweight structure and electrical functionality. Its remarkable properties make it a valuable choice for numerous industries that require both cushioning and electrical conductivity.
Table of Contents
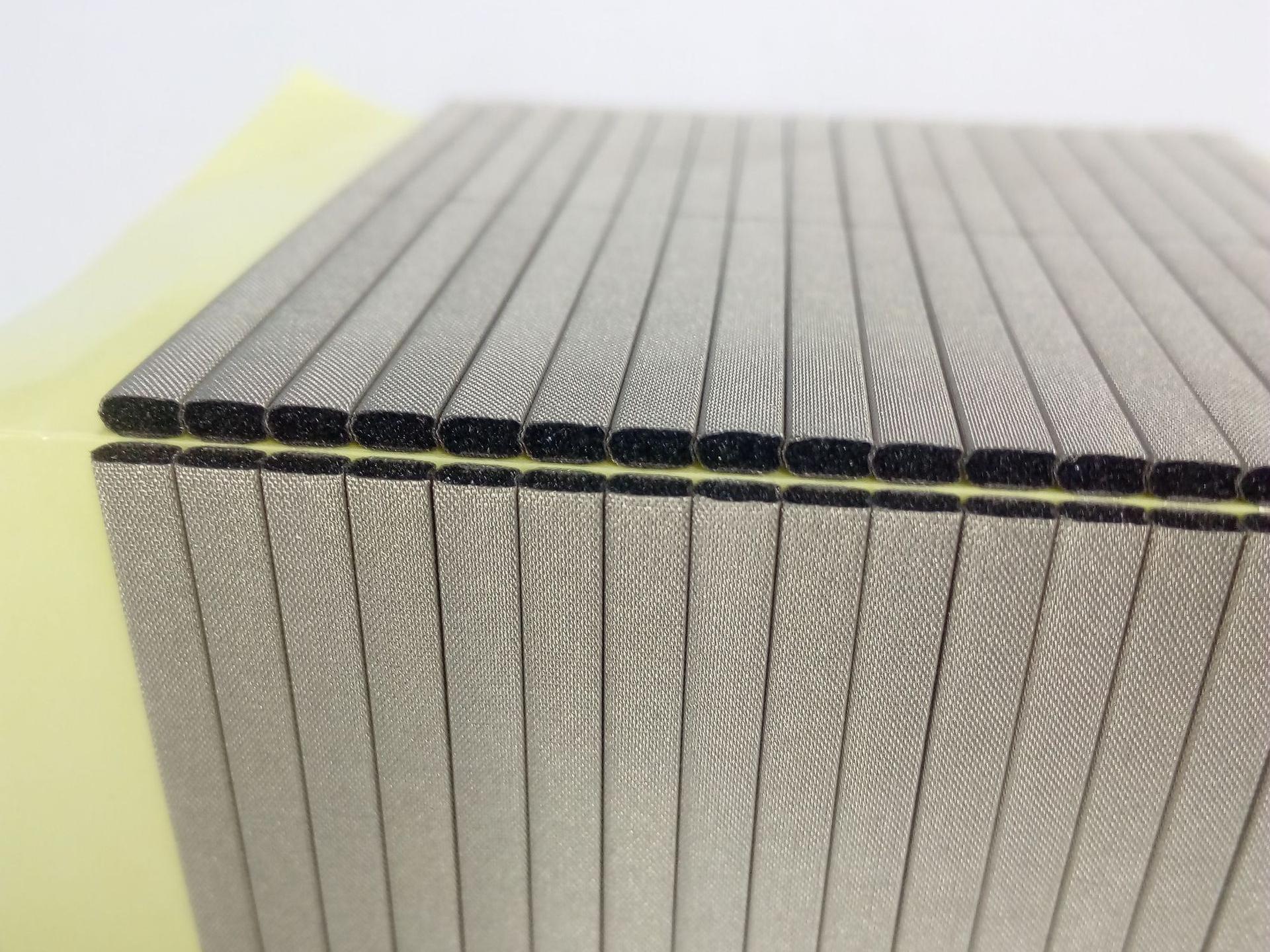
Electrically conductive foam
In modern industries, material performance and lightweight solutions are crucial for driving innovation. Among the various advancements in material science, electrically conductive foam has emerged as a highly versatile and efficient material, offering both high conductivity and the benefits of lightweight, flexible foam. Combining electrical conductivity with the characteristics of traditional foams, such as cushioning and energy absorption, electrically conductive foam is now widely used across various sectors. This article will explore the unique properties, manufacturing processes, diverse applications, and future trends of electrically conductive foam.
1. Characteristics of Electrically Conductive Foam
Electrically conductive foam, often described as a porous material composed of rubber matrix embedded with conductive fillers, provides the ideal combination of lightweight structure and electrical functionality. Its remarkable properties make it a valuable choice for numerous industries that require both cushioning and electrical conductivity. Some of the most notable characteristics of electrically conductive foam include:
Lightweight Structure
One of the primary benefits of electrically conductive foam is its lightweight nature. The foaming process significantly reduces the material’s density, making it lighter than solid rubber or metals. This characteristic is crucial for applications where weight reduction is essential, such as in automotive and aerospace industries. By incorporating gas bubbles into the material, foam maintains the necessary strength and resilience but at a much lower weight, enhancing efficiency and reducing the load on mechanical systems.
High Elasticity and Flexibility
Electrically conductive foam retains the flexibility and elasticity typical of rubber materials, even with a high foam ratio. This ensures that the foam can absorb shocks and vibrations effectively, making it suitable for applications such as impact protection, cushioning, and sealing. Despite its lightweight nature, the foam remains flexible enough to conform to different shapes, ensuring a snug fit in various applications.
Excellent Thermal and Acoustic Insulation
The porous structure of electrically conductive foam also endows it with excellent thermal and sound insulation properties. In applications where noise reduction or temperature control is necessary, conductive foam provides an effective barrier. For instance, it can be used in soundproofing panels for the construction industry or insulation pads for electronic components. Its ability to insulate both heat and sound contributes to improved energy efficiency and comfort in various settings.
Chemical Resistance
Another significant advantage of electrically conductive foam is its resistance to chemicals. Depending on the base rubber material used, the foam can be formulated to withstand exposure to harsh chemicals, oils, and other aggressive substances. This makes it an excellent choice for use in industrial environments, particularly in sectors like manufacturing, marine applications, and chemical processing.
Energy Absorption and Shock Resistance
Due to its porous structure, electrically conductive foam is particularly adept at absorbing energy. It can compress under impact or pressure, absorbing and dissipating the energy rather than transmitting it to the rest of the system. This property makes it highly effective in packaging applications, cushioning fragile electronics, or as a protective layer in automotive or industrial machinery.
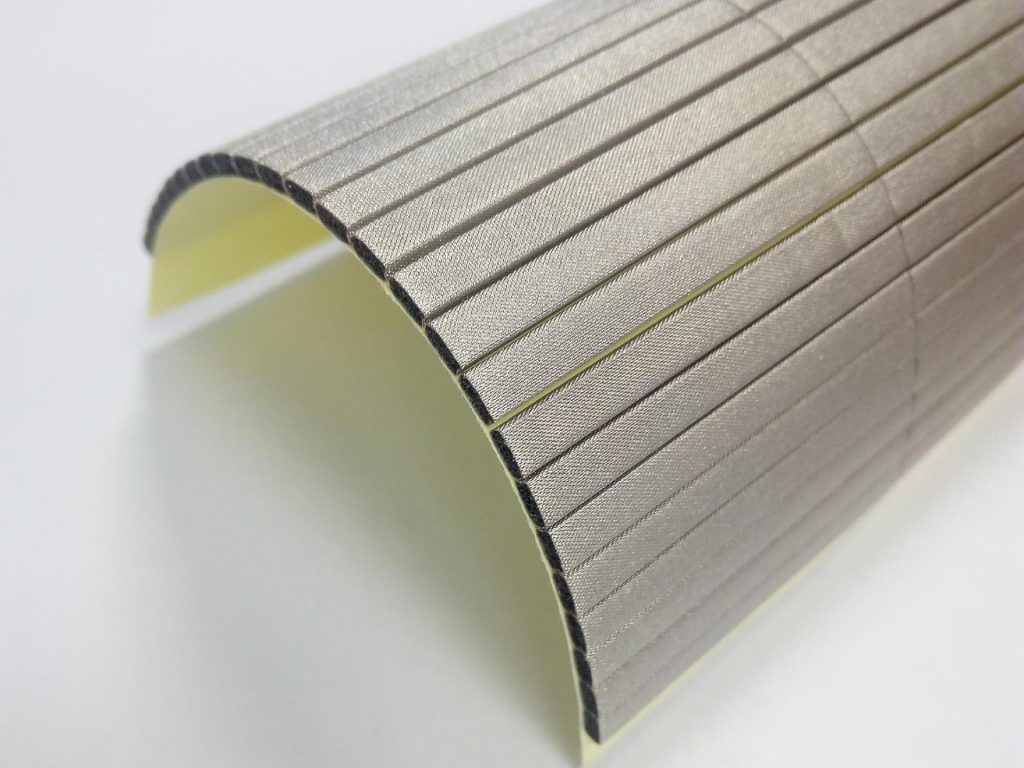
2. Manufacturing Process of Electrically Conductive Foam
The production of electrically conductive foam involves multiple precise steps, from selecting the base materials to processing the foam into the desired shape and form. Below is a detailed breakdown of the manufacturing process:
Material Selection
The manufacturing of electrically conductive foam begins with the selection of the base rubber matrix, which serves as the foundation for the foam. Common rubber matrices include natural rubber, nitrile rubber, silicone rubber, and neoprene. Each of these materials offers distinct properties that make them suitable for specific applications. For instance:
- Natural Rubber: Known for its elasticity and resilience, often used in automotive and heavy-duty applications.
- Nitrile Rubber: Excellent chemical resistance, commonly used in environments where exposure to oils and chemicals is expected.
- Silicone Rubber: High temperature and weather resistance, ideal for use in extreme environments, including electronics and aerospace.
Conductive Fillers
To achieve electrical conductivity, conductive fillers are incorporated into the rubber matrix. These fillers are typically materials such as carbon black, graphite, carbon nanotubes, or metal powders (e.g., copper or aluminum). The type and concentration of filler used determine the foam’s conductivity, and careful control of this aspect is essential to ensure that the foam meets the specific conductivity requirements of its intended application.
Foaming Agent and Process
A foaming agent is added to the rubber mixture to create the foam’s structure. Foaming agents can be classified into two types: chemical foaming agents and physical foaming agents.
- Chemical Foaming Agents: These agents release gas when exposed to heat or chemical reactions, causing the material to foam. Chemical agents often create fine, uniform cells in the foam, contributing to better insulation and cushioning properties.
- Physical Foaming Agents: These agents rely on physical processes like gas injection or heat to produce bubbles within the material. The foaming process involves heating the rubber mixture, causing the foaming agent to release gas, resulting in a cellular structure.
Mixing and Refining
After adding the foaming agent and conductive fillers, the rubber mixture is thoroughly blended. This step ensures uniform distribution of all components, including the conductive fillers, throughout the matrix. This stage is critical to achieving consistent foam properties, such as uniform conductivity and desired elasticity.
Molding and Forming
Once mixed, the rubber mixture is placed into molds or extruded into the desired shape. Different molding processes can be used, including:
- Extrusion: The mixture is forced through a mold, creating continuous shapes such as sheets or tubes.
- Compression Molding: The mixture is placed into a mold and subjected to heat and pressure, forming the foam into a specific shape.
- Injection Molding: The material is injected into a mold cavity, allowing for more complex shapes and finer details.
Post-Treatment and Curing
After molding, the foam is subjected to a curing process that solidifies the material, ensuring its final shape and stability. The foam is then cooled, shaped as necessary, and may undergo additional processes like cutting, grinding, or coating to meet specific application requirements.
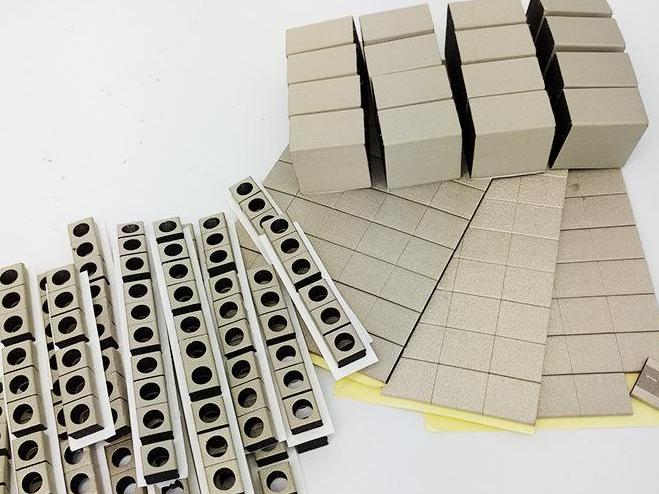
3. Applications of Electrically Conductive Foam
Electrically conductive foam’s unique combination of electrical conductivity, cushioning, and insulating properties makes it suitable for a wide range of applications across various industries. Below are some of the key areas where electrically conductive foam is used:
Automotive Industry
In the automotive sector, electrically conductive foam is widely used for a variety of purposes, from noise reduction and insulation to electrical shielding. For example:
- Seals and Gaskets: Conductive foam is used in door seals, windows, and gaskets to prevent electromagnetic interference (EMI) and provide a waterproof and dustproof seal.
- Seat Cushions: The foam’s shock absorption properties improve passenger comfort while providing electrical insulation in certain automotive components.
Aerospace and Defense
In the aerospace and defense industries, electrical conductivity is crucial for preventing EMI, which can interfere with sensitive systems and electronics. Electrically conductive foam is used to protect onboard electronic systems from external interference, as well as in sealing and cushioning applications within spacecraft and defense equipment.
Consumer Electronics
As the demand for smaller, more efficient electronic devices grows, the need for conductive foam in consumer electronics has expanded. It’s commonly used in:
- Smartphones and Tablets: Conductive foam is used in the protective casings and cushioning for electronics, absorbing shocks and reducing the risk of damage from drops or impacts.
- Laptops and Computers: Foam is also used to provide thermal management, preventing overheating of sensitive components and offering electrical conductivity for EMI shielding.
Medical Devices
In medical devices, electrically conductive foam can be employed to provide EMI shielding, protect sensitive instruments, and act as an insulator. Medical imaging devices, monitors, and diagnostic equipment often rely on conductive foam to maintain optimal functioning and prevent interference from external electrical signals.
Packaging
One of the most common uses for conductive foam is in packaging fragile electronics or equipment. The foam provides superior cushioning, absorbing impacts during shipping, and protects the components from static electricity. It is especially useful in packaging high-tech items like circuit boards, microprocessors, and optical sensors.
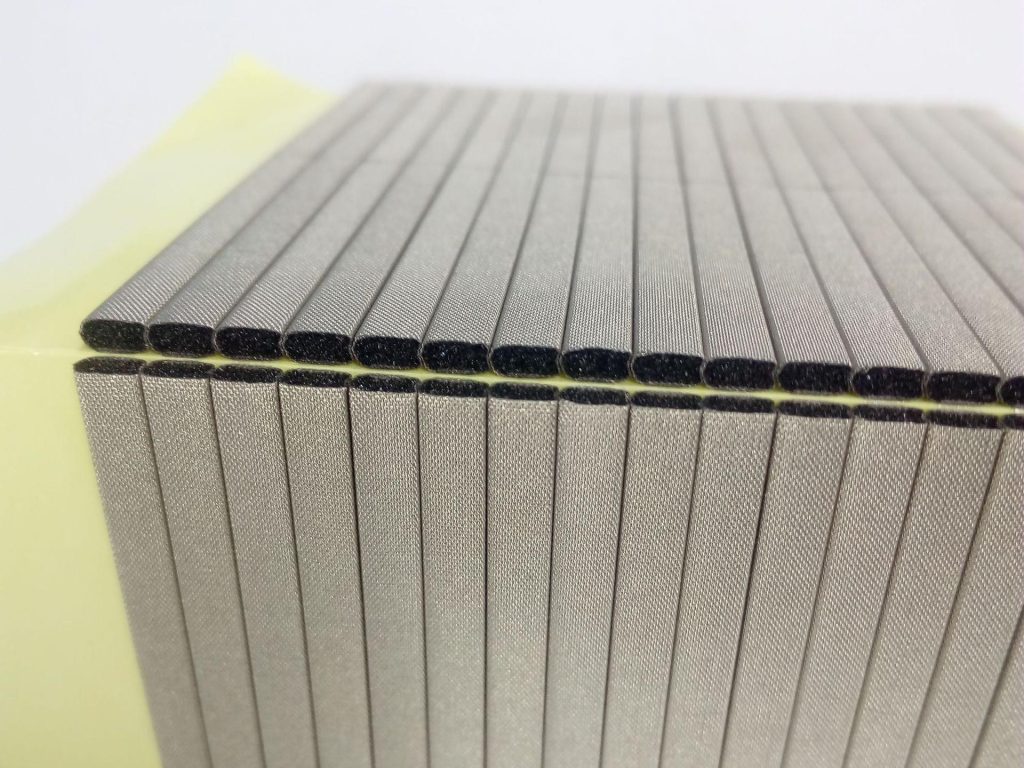
4. Emerging Trends and Future of Electrically Conductive Foam
As technology continues to advance, the demand for high-performance, multifunctional materials is increasing. Electrically conductive foam is expected to evolve in several key areas:
Development of High-Performance Materials
Future developments in conductive foam will focus on improving its heat resistance, mechanical strength, and chemical resistance. Materials with enhanced properties will be needed to withstand extreme conditions in industries like aerospace, automotive, and defense, where reliability and durability are paramount.
Sustainability and Eco-Friendly Solutions
As industries strive to reduce their environmental impact, there will be a growing emphasis on sustainable materials. Electrically conductive foam manufacturers are exploring eco-friendly alternatives to traditional synthetic rubbers and foaming agents. Research into biodegradable conductive foams and recyclable materials could lead to environmentally friendly solutions that meet both performance and sustainability criteria.
Integration with Smart Technologies
The integration of conductive foam with sensor technology could lead to the development of smart materials that not only provide shielding and insulation but also monitor system performance and provide feedback. These “smart” foams could have self-healing properties or adapt to changing environmental conditions, offering enhanced functionality and longer lifecycles.
Customization and Advanced Manufacturing Techniques
With advancements in 3D printing and other additive manufacturing methods, the production of custom electrically conductive foams will become more accessible. This will enable manufacturers to design foams tailored to specific requirements in terms of shape, density, conductivity, and elasticity. Custom solutions will become increasingly important for niche applications across industries.
5. Conclusion
Electrically conductive foam represents a cutting-edge solution that combines the best of lightweight foam with electrical conductivity. Its unique properties make it indispensable in industries that require both impact protection and electrical shielding. With its diverse applications and ongoing innovations, conductive foam is set to play a critical role in the future of electronics, automotive, medical devices, and packaging. The continued evolution of this material, driven by advanced manufacturing techniques, eco-friendly considerations, and smart technology integration, ensures that electrically conductive foam will remain a key enabler of high-performance, lightweight, and efficient products in the coming years.
As industries continue to push the boundaries of technology, the demand for advanced materials like electrically conductive foam grows, particularly in sectors that require both lightweight properties and high-performance electrical shielding. A key player in providing these solutions is Handa Shielding, a leading manufacturer of high-quality EMI shielding products. Their expertise in creating precision-engineered components, including conductive foams and other shielding materials, ensures that manufacturers can meet the most stringent demands for electromagnetic interference (EMI) protection. With a commitment to innovation and quality, Handa Shielding stands at the forefront of the materials revolution, helping industries build safer, more efficient products for the future.
You May Also Like
-
EMI tapes, EMC foils, conductive textiles & half conductive non-woven
Copper foil tape
Copper foil tape 1. Introduction to Copper Foil Tape2. Properties of Copper Foil Tape3. Types of Copper Foil Tape4. Applications of Copper Foil Tape4.1. Electromagnetic Interference (EMI) Shielding4.2. Grounding Applications4.3. Static Discharge Protection4.4. Printed Circuit Board (PCB) Applications4.5. Stained Glass......
-
EMI tapes, EMC foils, conductive textiles & half conductive non-woven
Mu-ferro/mu-metal foil
1. What is Mu-Ferro Foil?2. Composition of Mu-Ferro Foil3. Magnetic Properties of Mu-Ferro Foil4. Applications of Mu-Ferro Foil4.1 Electromagnetic Interference (EMI) Shielding4.2 Magnetic Field Shielding4.3 Transformer and Inductor Design4.4 Aerospace and Defense Applications5. Advantages of Mu-Ferro Foil6. Challenges and Considerations7.......
-
Fingerstrips
PCB/SMD spring finger contacts
Spring finger contacts 1. Basic Concepts2. Application Scenarios2.1 Consumer Electronics 1. Basic Concepts Spring finger contacts, also called "spring fingers" ,serve as connectors between PCBs and SMDs (Surface Mount Devices). They are typically employed where frequent insertion and removal or......
-
EMI/EMC Shielding | RFI Shielding | EMI Gaskets
RF/EMI Shield Spiral Gasket
Handa spiral tubes https://www.handashielding.com/request-a-quote.html Material Properties of Handa Spiral TubesEMI Shielding Performance in Various FrequenciesPerformance in Humid and Corrosive EnvironmentsApplications Across IndustriesInstallation and Maintenance ConsiderationsConclusion and Future Outlook Handa spiral tubes are known for their remarkable performance in EMI shielding......
-
EMI/EMC Shielding | RFI Shielding | EMI Gaskets
RF/EMI Shield Spiral Gasket
Spiral shielding gaskets are essential components in various industrial applications, providing electromagnetic interference (EMI) shielding while ensuring reliable sealing. Their effectiveness, however, can be compromised in corrosive environments, making it crucial to enhance their corrosion resistance. This article explores the......