How do knitted wire mesh gaskets compare to other types of gaskets in terms of EMI/RFI shielding?
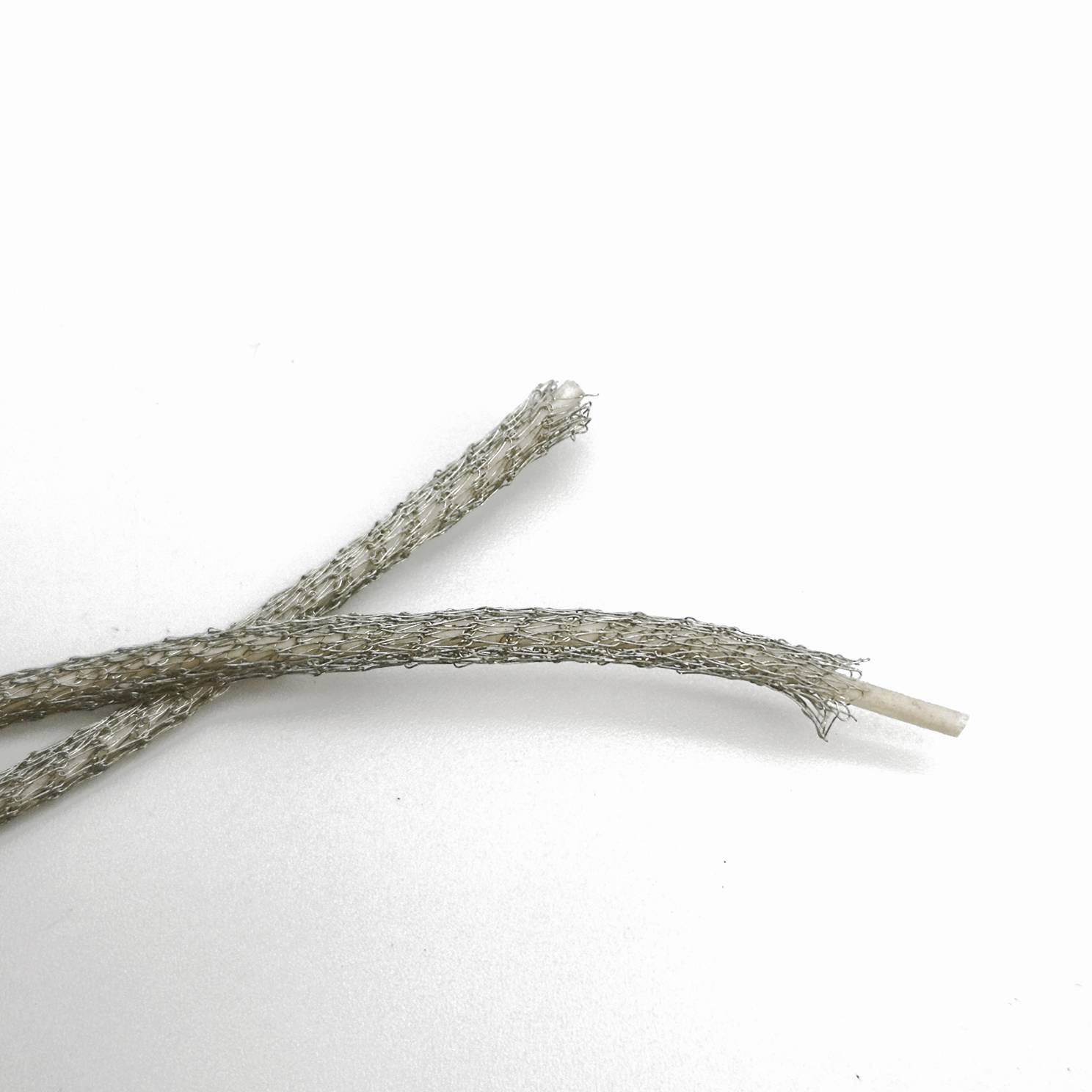
Knitted wire mesh gaskets-Handashielding
Table of Contents
Part 1: Technical Performance of Knitted Wire Mesh Gaskets in EMI/RFI Shielding
1. Introduction to EMI/RFI Shielding
Electromagnetic interference (EMI) and radio-frequency interference (RFI) are pervasive challenges in modern electronics, telecommunications, aerospace, and defense systems. Shielding solutions must attenuate unwanted electromagnetic waves to ensure device reliability, signal integrity, and compliance with regulatory standards. Among the myriad shielding technologies, gaskets play a critical role in sealing gaps and apertures in enclosures while maintaining conductivity. This section evaluates knitted wire mesh gaskets against alternatives such as conductive elastomers, metal sheet gaskets, conductive foams, and fingerstock.
2. Knitted Wire Mesh Gaskets: Design and Functionality
Knitted wire mesh gaskets are fabricated from interlocking metal wires (typically stainless steel, copper, aluminum, or Monel) in a resilient, spring-like structure. Their design combines flexibility with high conductivity, enabling them to conform to irregular surfaces and maintain continuous electrical contact under compression. Key attributes include:
- High Surface Area: The porous structure enhances shielding effectiveness (SE) by creating multiple reflection points for electromagnetic waves.
- Compression Recovery: Resilient knitting allows repeated compression without permanent deformation.
- Environmental Resistance: Metal alloys resist corrosion, temperature extremes, and chemical exposure.
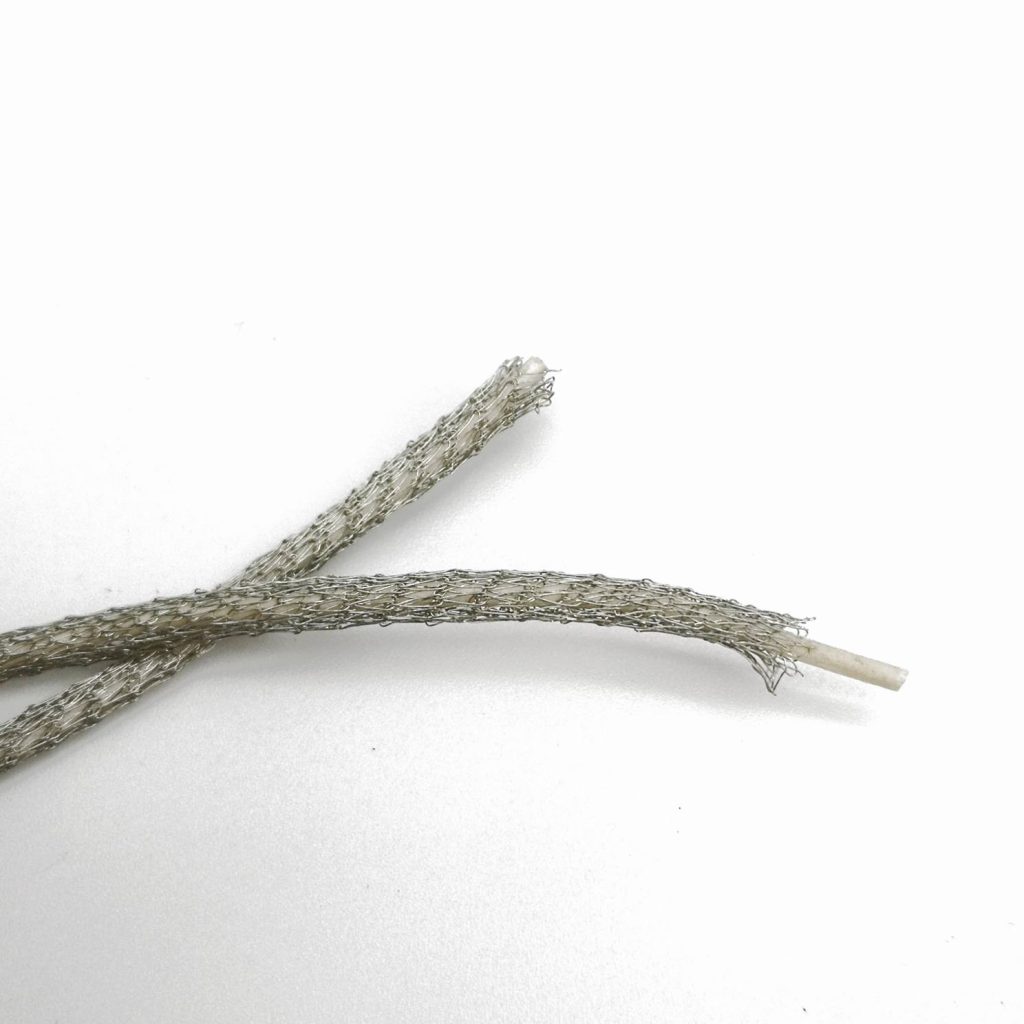
3. Shielding Effectiveness: Comparative Analysis
3.1 Conductive Elastomers
Conductive elastomers (e.g., silicone or fluorosilicone filled with silver, nickel, or carbon) offer excellent environmental sealing (IP68) but lag in shielding performance.
- Frequency Response: Elastomers exhibit frequency-dependent attenuation. Silver-filled variants perform well up to 10 GHz but degrade at higher frequencies due to skin effect limitations. Knitted mesh gaskets, with bulk metal conductivity, maintain stable SE across a broader spectrum (DC to 40 GHz).
- Contact Resistance: Elastomers require high compression forces (≥20% strain) to achieve low interfacial resistance. Knitted mesh, with metal-to-metal contact, ensures <1 mΩ resistance even at low compression.
3.2 Metal Sheet Gaskets
Solid metal gaskets (e.g., beryllium copper, tin-plated steel) provide superior SE (>120 dB) but lack flexibility. They are prone to galvanic corrosion when mated with dissimilar metals and cannot accommodate surface irregularities. Knitted mesh compensates for uneven surfaces, reducing the risk of “hot spots” or leakage paths.
3.3 Conductive Foams
Open-cell polyurethane foams coated with conductive metals (e.g., nickel-copper) are lightweight and low-cost but suffer from mechanical fragility. Compression set and particle shedding limit their lifespan in dynamic environments. Knitted mesh outperforms in durability, withstanding >10,000 compression cycles without degradation.
3.4 Fingerstocks/Fingerstrip
Fingerstock (stamped metal springs) offers high shielding and minimal compression force but is directionally dependent. Installation requires precise alignment, and sharp edges risk damaging mating surfaces. Knitted mesh provides omnidirectional shielding and is inherently forgiving of misalignment.
4. Environmental and Mechanical Durability
- Temperature Range: Knitted wire mesh operates from cryogenic (-200°C) to high temperatures (900°C for Inconel alloys), outperforming elastomers (-55°C to 200°C) and foams (-40°C to 125°C).
- Chemical Resistance: Stainless steel and Monel resist solvents, fuels, and salt spray. Elastomers degrade under prolonged UV or ozone exposure.
- Vibration and Shock: The knitted structure dampens mechanical vibrations, a critical advantage in aerospace and automotive applications.
5. Case Studies
- Aerospace: NASA employs knitted mesh gaskets in satellite housings for their radiation hardness and thermal stability.
- Medical Imaging: MRI machines use copper-knitted gaskets to shield RF noise without interfering with magnetic fields.
- 5G Infrastructure: Base stations utilize aluminum mesh gaskets for lightweight, high-SE shielding in millimeter-wave bands.
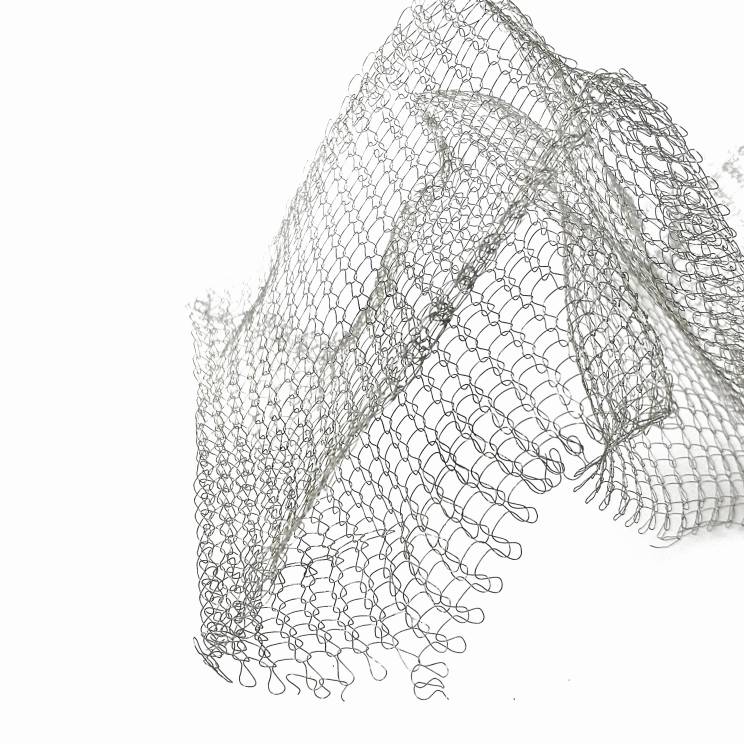
Part 2: Cost Analysis and Market Viability of Knitted Wire Mesh Gaskets
1. Cost Drivers in EMI/RFI Shielding
The total cost of ownership (TCO) for shielding solutions includes material expenses, installation labor, maintenance, and lifecycle longevity. This section compares knitted wire mesh to alternatives across these metrics.
2. Material and Manufacturing Costs
2.1 Raw Material Expenses
- Knitted Mesh: Material costs vary by alloy. Stainless steel (304/316) ranges from $20–$50/kg, while specialty alloys (e.g., titanium) exceed $150/kg. Wire knitting is labor-intensive, contributing to higher upfront costs vs. conductive foams ($5–$15/kg).
- Elastomers: Silver-filled silicone costs $200–$500/kg due to precious metal content. Nickel-coated graphite variants are cheaper ($50–$100/kg) but less conductive.
- Fingerstock: Precision stamping of beryllium copper costs $100–$300/kg, with tooling amortization adding to initial expenses.
2.2 Fabrication Complexity
Knitted mesh requires specialized CNC knitting machines, limiting economies of scale. Conductive foams and elastomers are extruded or molded, enabling high-volume production at lower marginal costs.
3. Installation and Maintenance Costs
- Knitted Mesh: Pre-cut gaskets with pressure-sensitive adhesive (PSA) simplify installation. However, custom profiles for irregular geometries incur design fees. Long-term savings arise from minimal maintenance; mesh gaskets rarely require replacement.
- Elastomers: Require precise groove designs and high compression forces, increasing assembly time. Silicone gaskets degrade over 5–10 years, necessitating frequent replacements in harsh environments.
- Conductive Paints/Sprays: Low upfront cost ($10–$50/m²) but poor durability. Reapplication every 2–3 years raises TCO.
4. Lifecycle and Reliability
- Knitted Mesh: Lifespan exceeds 20 years in static applications. Corrosion-resistant alloys avoid downtime in industrial settings.
- Conductive Fabrics: Laminated textiles degrade after 3–5 years due to flex fatigue.
- Metalized Plastics: Suffer from delamination and arc tracking in high-voltage environments.
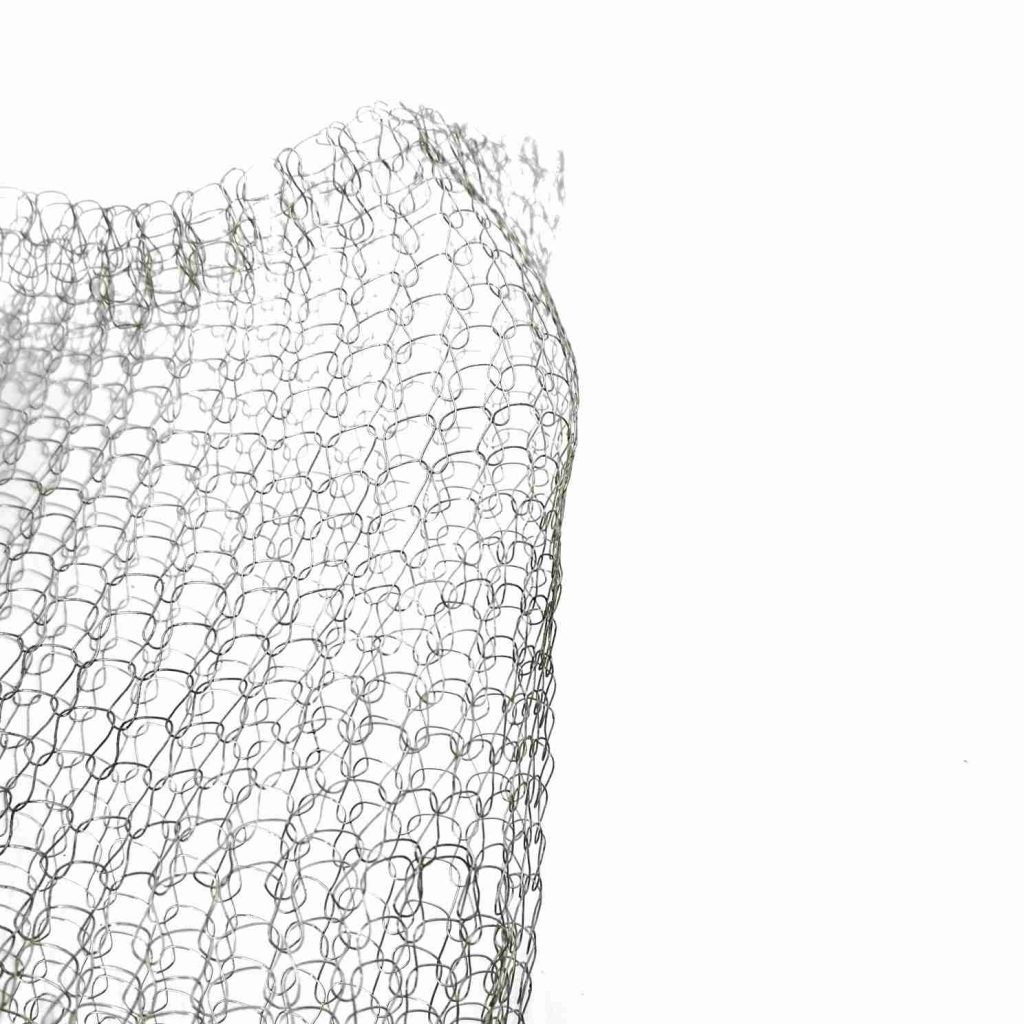
5. Market Trends and Cost Reduction Strategies
- Automation: Adoption of robotic knitting machines reduces labor costs by 30–40%.
- Hybrid Designs: Combining knitted mesh with elastomer cores (e.g., Parker Chomerics’s SOFT-SHIELD) balances cost and performance.
- Recyclability: Stainless steel mesh is 100% recyclable, appealing to eco-conscious industries. Elastomers often end up in landfills.
6. Industry-Specific Cost-Benefit Analysis
- Consumer Electronics: Conductive coatings dominate due to low per-unit costs, but knitted mesh is preferred in premium devices (e.g., military-grade tablets).
- Automotive: Knitted mesh gains traction in electric vehicles (EVs) for battery shielding, offsetting higher costs with warranty risk reduction.
- Industrial IoT: Retrofit applications favor conductive tapes, while new installations use knitted mesh for future-proofing.
7. Conclusion
Knitted wire mesh gaskets offer unmatched shielding performance and longevity, justifying their premium cost in mission-critical applications. However, conductive elastomers and foams remain viable for budget-constrained, low-frequency uses. As wireless systems advance toward 6G and terahertz frequencies, the demand for high-performance shielding will solidify knitted mesh’s role in the EMI/RFI ecosystem.