Handa Shield Spiralrohre Dichtungen: Umfassende Klassifizierung und Materialführer

Handa Shield Spiralschläuche Dichtungen
Inhaltsübersicht
I. Einführung in die Handa Shield Spiralschläuche Dichtungen
Handa Shield Spiralschläuche Dichtungen sind wichtige Komponenten zum Schutz empfindlicher elektronischer Systeme vor externen elektromagnetischen Störungen oder zur Eindämmung von Emissionen aus internen Quellen. Ihr spiralförmiges Design kombiniert Flexibilität, Haltbarkeit und hohe Abschirmwirkung (SE). Die Materialauswahl wirkt sich direkt auf die Leistung in extremen Umgebungen (Temperatur, Korrosion, mechanische Belastung) aus. Dieser Leitfaden befasst sich mit speziellen Legierungen und ihren Anwendungen.
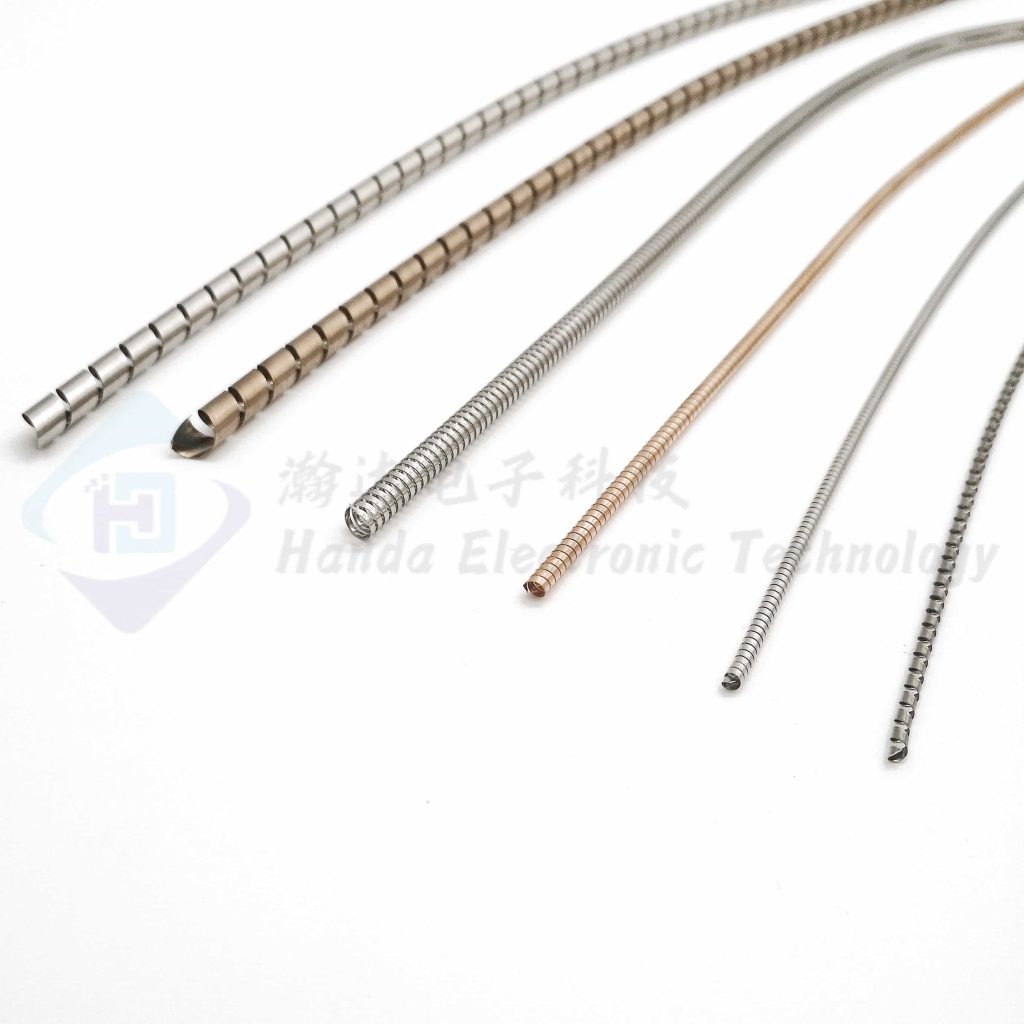
II. Spiralrohre aus rostfreiem Stahl
Rostfreier Stahl (SS) ist aufgrund seiner Ausgewogenheit von Leitfähigkeit, Korrosionsbeständigkeit und Kosteneffizienz das am häufigsten verwendete Material für die EMI-Abschirmung. Die Untertypen variieren in ihrer Zusammensetzung, um spezifische Anforderungen zu erfüllen.
1. Austenitische nichtrostende Stähle
Austenitische Stähle sind nichtmagnetische Chrom-Nickel-Legierungen mit ausgezeichneter Umformbarkeit und Korrosionsbeständigkeit.
a. SS 301
- Zusammensetzung: 16-18% Cr, 6-8% Ni, 0,15% C.
- Eigenschaften:
- Hohe Zugfestigkeit (bis zu 1.600 MPa bei Kaltverformung).
- Mäßige Korrosionsbeständigkeit (geeignet für Innenräume und trockene Umgebungen).
- Die magnetische Permeabilität nimmt mit der Kaltverformung zu.
- EMI-Abschirmung Anwendungen:
- Unterhaltungselektronik (z. B. die interne Abschirmung von Smartphones).
- Flexible Schläuche in der Robotik, wo hohe Festigkeit erforderlich ist.
- Kostengünstige Alternative zu 304 in nicht-korrosiven Umgebungen.
- Beschränkungen:
- Anfällig für Spannungsrisskorrosion in chloridreichen Umgebungen.
b. SS 304 (A2 Edelstahl)
- Zusammensetzung: 18% Cr, 8% Ni, 0,08% C.
- Eigenschaften:
- Hervorragende Korrosionsbeständigkeit gegenüber 301 (oxidationsbeständig bis zu 870°C).
- Ein geringerer Kohlenstoffgehalt minimiert die Ausscheidung von Karbid.
- Im geglühten Zustand nicht magnetisch.
- Anwendungen:
- Medizinische Bildgebungsgeräte (MRI-Räume).
- Industrielle Automatisierungssysteme, die milden Chemikalien ausgesetzt sind.
- EMI-Abschirmung für die Lebensmittelverarbeitung (FDA-konform).
- Normen: ASTM A240, MIL-DTL-32139.
c. EDELSTAHL 316/316L
- Zusammensetzung: 16-18% Cr, 10-14% Ni, 2-3% Mo, 0,03% C (316L).
- Die wichtigsten Vorteile:
- Molybdän erhöht die Chloridbeständigkeit (ideal für den Einsatz auf See/Offshore).
- Der geringe Kohlenstoffgehalt von 316L verhindert eine Sensibilisierung beim Schweißen.
- Leistungsmetriken:
- Schirmungseffektivität: 60-100 dB (1 MHz-10 GHz).
- Betriebstemperatur: -200°C bis +800°C (vakuumgeglüht).
- Anwendungen:
- Luft- und Raumfahrt Avionik (Salznebelbeständigkeit gemäß MIL-STD-810).
- Pharmazeutische Reinräume (sanitäre Passivierung).
- Instrumentierung von Kernreaktoren (Strahlung + Korrosion).
2. Ausscheidungshärtender rostfreier Stahl: SS 17-7 PH
- Zusammensetzung: 17% Cr, 7% Ni, 1% Al, 0,09% C.
- Wärmebehandlung:
- Lösungsgeglüht bei 1.040°C, dann bei 480-620°C zur martensitischen Umwandlung gealtert.
- Mechanische Eigenschaften:
- Zugfestigkeit: 1.380 MPa (gealtert).
- Hohe Ermüdungsfestigkeit.
- EMI Vorteile:
- Behält die Abschirmwirkung unter zyklischer Belastung bei.
- Magnetische Eigenschaften durch Alterung einstellbar.
- Anwendungen:
- Militärische Antennenabschirmung (Übereinstimmung mit MIL-STD-461).
- Öl-/Gassensoren im Bohrloch (H2S-Beständigkeit).
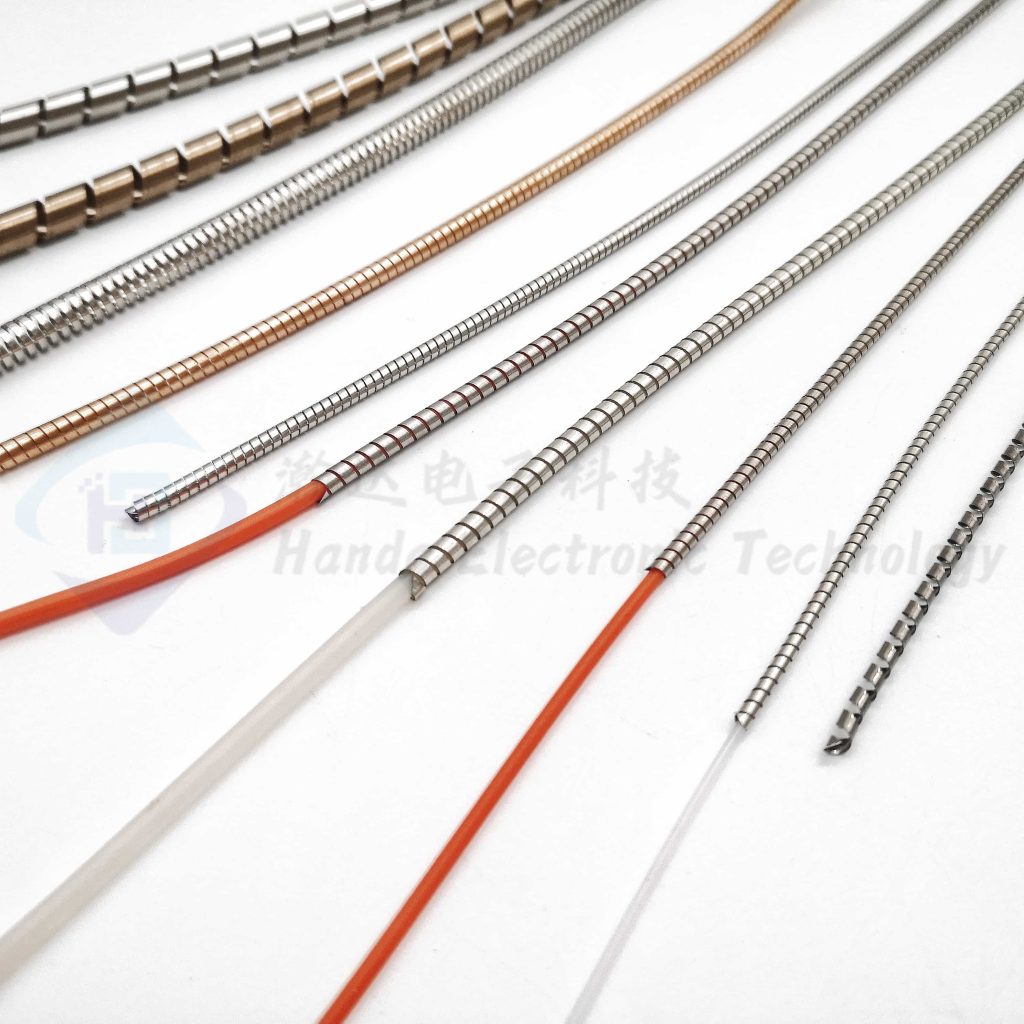
III. Titan-Spiralrohre
Titan bietet ein unübertroffenes Verhältnis von Festigkeit zu Gewicht und Biokompatibilität und ist ideal für Nischenanwendungen zur EMI-Abschirmung.
1. Kommerziell reines (CP) Titan (Grade 1-4)
- Klasse 2: Am häufigsten (0,25% O, 99% Ti).
- Leitfähigkeit: 3% IACS (niedriger als Stahl, kompensiert durch die Dicke).
- Mechanismus der Abschirmung: Reflektivität aufgrund der Oberflächenleitfähigkeit.
- Anwendungen:
- Implantierbare medizinische Geräte (MRT-Kompatibilität).
- Satellitenabschirmung (thermische Stabilität im Weltraum).
2. Titan-Legierungen (Grad 5: Ti-6Al-4V)
- Zusammensetzung: 6% Al, 4% V.
- Eigenschaften:
- Zugfestigkeit: 1.000 MPa (zweimal CP-Titan).
- Korrosionsbeständigkeit: Unempfindlich gegen Chloride und Säuren.
- EMI-Leistung:
- Wirksam bis zu 40 GHz (geeignet für 5G mmWave).
- Geringe thermische Ausdehnung vermeidet Signaldrift.
- Anwendungen:
- Elektronik für Hyperschallraketen (aerothermische Stabilität).
- Tiefsee-ROVs (hoher Druck + EMI-Abschirmung).
IV. Materialvergleichstabelle (Edelstahl vs. Titan)
Eigentum | SS 304 | EDELSTAHL 316L | 17-7 PH | Ti-6Al-4V |
---|---|---|---|---|
Dichte (g/cm³) | 7.9 | 8.0 | 7.8 | 4.4 |
Zugfestigkeit (MPa) | 505 | 515 | 1,380 | 1,000 |
Korrosionsbeständigkeit | Gut | Ausgezeichnet | Mäßig | Herausragend |
Abschirmung (dB @1 GHz) | 85 | 90 | 80 | 70 |
Kostenindex | 1.0 | 1.5 | 3.0 | 10.0 |
V. Überlegungen zur Gestaltung
- Geometrie der Spirale:
- Teilung und Überlappungsverhältnis optimieren die Flexibilität gegenüber der Kontinuität der Abschirmung.
- Die Rückfederung von Titan erfordert spezielle Wickelwerkzeuge.
- Oberflächenbehandlungen:
- Passivierung (SS): Ein Salpetersäurebad verbessert die Cr-Oxidschicht.
- Eloxieren (Ti): Dickes Oxid für Hochspannungsisolierung.
- Fügeverfahren:
- Laserschweißen für hermetische Dichtungen in Vakuumsystemen.
- Leitfähiges Epoxid für hybride Metall-Polymer-Abschirmungen.
VI. Beryllium-Kupfer (BeCu) Spiralrohre
Berylliumkupfer ist eine Hochleistungslegierung, die für ihre einzigartige Kombination aus elektrischer Leitfähigkeit, Ermüdungsfestigkeit und nichtmagnetischen Eigenschaften geschätzt wird.
1. Zusammensetzung und Benotung
- C17200 (Legierung 25):
- 1,8-2,0% Be, 0,2-0,6% Co/Ni, Rest Cu.
- Höchste Festigkeit (bis zu 1.400 MPa) unter den Kupferlegierungen.
- C17500 (Legierung 3):
- 0,4-0,7% Be, 1,4-2,2% Co, geringere Leitfähigkeit, aber bessere thermische Stabilität.
2. Wichtige Eigenschaften
- Elektrische Leitfähigkeit22-60% IACS (einstellbar über Alterung).
- Wärmeleitfähigkeit: 105 W/m-K (3x rostfreier Stahl).
- Nichtparken: Ideal für explosive Umgebungen (ATEX/IECEx).
- Ermüdungswiderstand: Hält >100.000 Biegezyklen ohne Rissbildung stand.
3. EMI-Abschirmungsleistung
- Wirksamkeit der Abschirmung: 100-120 dB (breitbandig, 10 MHz-10 GHz).
- Oberfläche: Die stromlose Vernickelung verbessert die Oxidationsbeständigkeit.
4. Anwendungen
- Luft- und Raumfahrt: Avionikabschirmung in Kampfjets (F-35 Lightning II).
- Telekommunikation: 5G mmWave-Antennen (geringer Signalverlust bei 28 GHz).
- Medizinische: MRT-kompatible chirurgische Instrumente (nicht-magnetisch).
5. Sicherheitserwägungen
- Die maschinelle Bearbeitung erfordert OSHA-konforme Kontrollen (Berylliumstaub ist giftig).
- Alternative: Phosphorbronze für risikoarme Anwendungen.
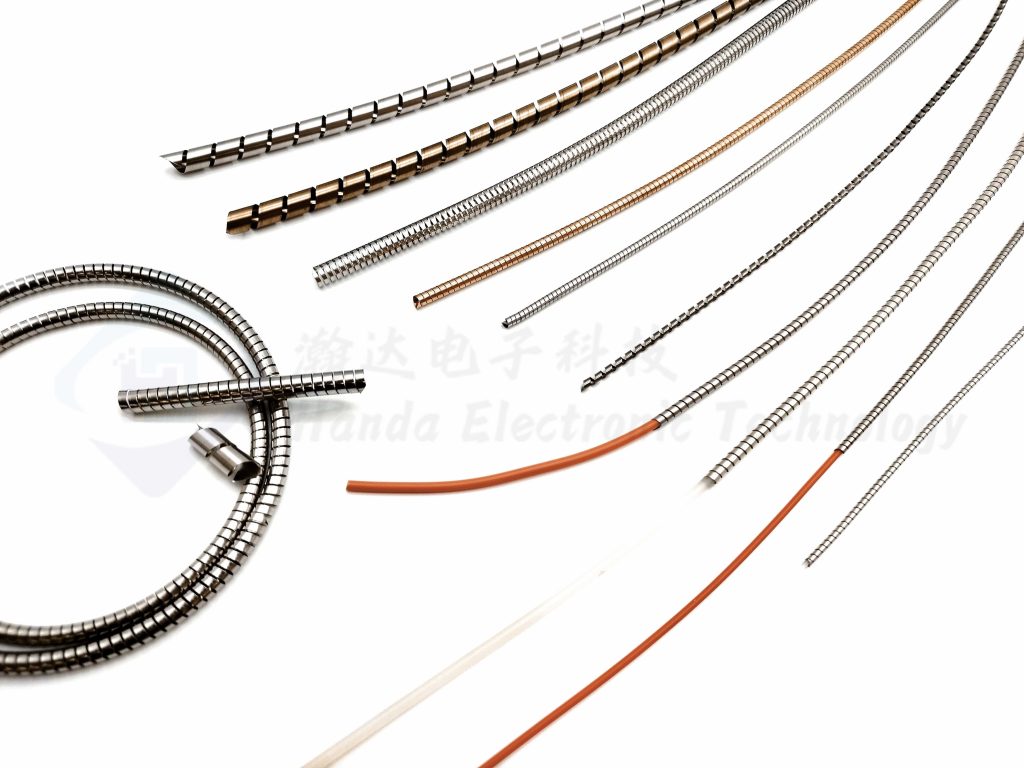
VII. Elgiloy® (Kobalt-Chrom-Nickel-Legierung)
Elgiloy ist eine Superlegierung auf Kobaltbasis mit außergewöhnlicher Korrosionsbeständigkeit und mechanischer Stabilität.
1. Zusammensetzung
- 40% Co, 20% Cr, 15% Ni, 7% Mo, 2% Mn, 0,04% C.
2. Leistungsvorteile
- Korrosionsbeständigkeit: Beständig gegen Lochfraß in Seewasser (ASTM G48).
- Temperaturbereich: -200°C bis +600°C (erhält die Elastizität).
- Magnetische Eigenschaften: Auch nach Kaltbearbeitung nicht magnetisch.
3. EMI-Abschirmung Anwendungsfälle
- Öl und Gas: Unterwasserleitungen in Sauergasbohrlöchern (H2S-Beständigkeit).
- Verteidigung: EMI-Dichtungen für Radarsysteme (MIL-DTL-83528).
- Medizinische: Implantierbare Neurostimulatoren (biokompatibel gemäß ISO 10993).
VIII. Hastelloy® (Nickel-Molybdän-Chrom-Legierungen)
Hastelloy-Legierungen eignen sich hervorragend für extreme chemische und thermische Umgebungen.
1. Gemeinsame Klassen
- Hastelloy C-276:
- 57% Ni, 16% Mo, 15% Cr, 4% W.
- Beständig gegen Salz- und Schwefelsäure.
- Hastelloy C-22:
- Höheres Cr (22%) für oxidierende Medien (Salpetersäure, Fe³⁺).
2. Vorteile der EMI-Abschirmung
- Chemische Beständigkeit: Unbeeinflusst von 98% H2SO4 bei 50°C.
- Thermische Stabilität: Betriebsbereich bis zu 1.100°C (oxidierend).
- Wirksamkeit der Abschirmung75-90 dB (abhängig von der Wandstärke).
3. Industrielle Anwendungen
- Chemische Verarbeitung: EMI-Abschirmung des Reaktors bei der HCl-Produktion.
- Energie: Brennstoffzellenstapel (Korrosions- und EMI-Schutz).
- Weltraum: Telemetriesysteme für Raketentriebwerke (Temperaturwechselbeständigkeit).
IX. Erweiterte Materialvergleiche
1. Leistungstabelle
Eigentum | BeCu C17200 | Elgiloy®. | Hastelloy C-276 |
---|---|---|---|
Dichte (g/cm³) | 8.3 | 8.9 | 8.9 |
Zugfestigkeit (MPa) | 1,400 | 1,600 | 790 |
Leitfähigkeit (% IACS) | 22 | 2 | 1.5 |
Maximale Betriebstemperatur (°C) | 400 | 600 | 1,100 |
Abschirmung (dB @1 GHz) | 110 | 85 | 75 |
2. Hybride Materiallösungen
- Kupfer-Clad-Edelstahl: Kombiniert die Stärke von SS mit der Leitfähigkeit von Cu (60 dB SE bei 0,1 mm Dicke).
- Mehrschichtige Rohre: Außenschicht aus Elgiloy + Innenschicht aus BeCu für Vibrations- und EMI-Abschirmung.
X. Prüfung und Zertifizierung
1. EMI-Normen
- MIL-STD-461G: Störaussendung (RE102) und Störempfindlichkeit (RS103).
- IEEE 299-2006: Wirksamkeit der Abschirmung von Gehäusen (10 kHz-40 GHz).
2. Umweltprüfung
- Salzsprühnebel (ASTM B117): 5.000+ Stunden für Marine-Legierungen (316L, Hastelloy).
- Thermische Wechselbeanspruchung (MIL-STD-810H): -65°C bis +150°C für Komponenten der Luft- und Raumfahrt.
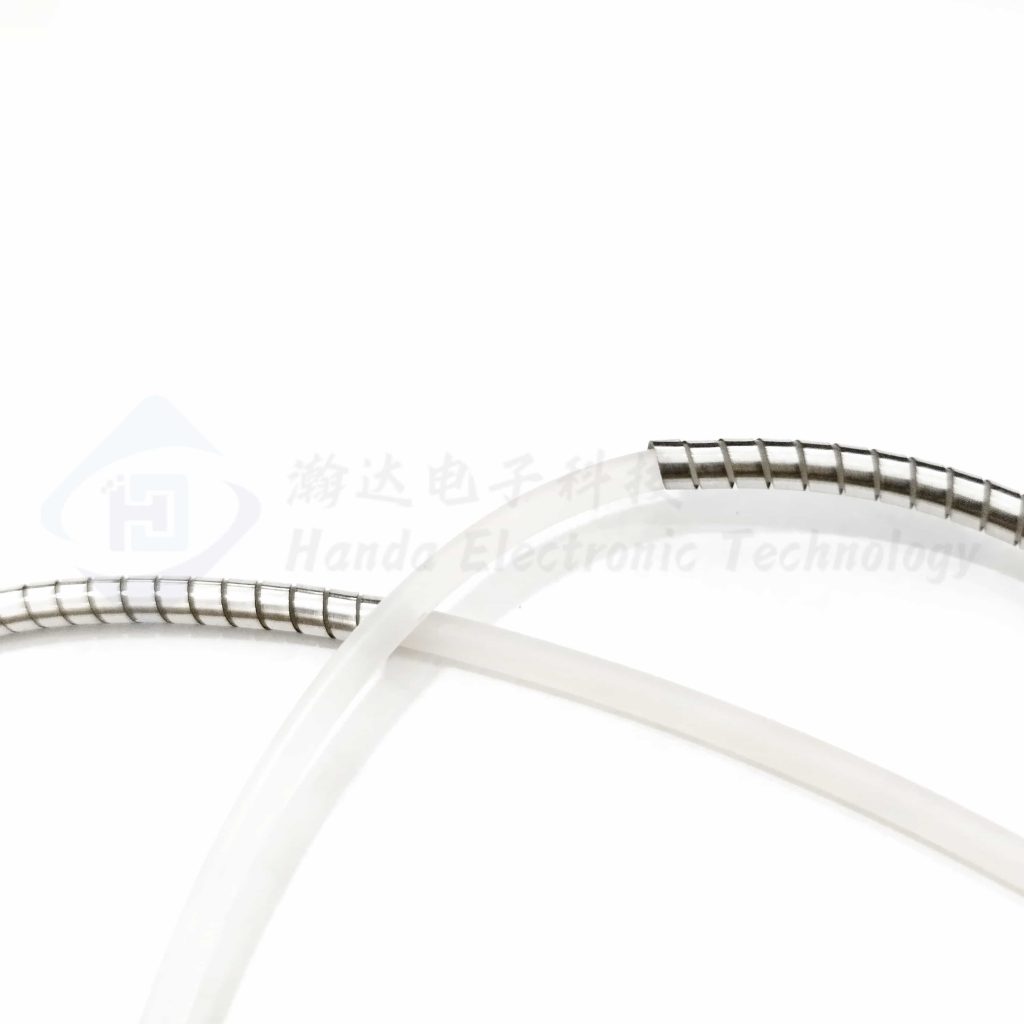
XI. Fallstudien
- Militärische UAVs: Elgiloy-Spiralrohre in Datenleitungen sind resistent gegen Sandabrieb (MIL-STD-810) und Verklemmungen.
- Herzschrittmacher: BeCu-Abschirmungen verhindern EMI von Mikrowellen und sind gleichzeitig MRI-sicher.
- 5G-Infrastruktur: Die Hastelloy C-276-Rohre in den Basisstationen widerstehen der Korrosion an der Küste.
XII. Aufkommende Trends
- Additive Fertigung: 3D-gedruckte Spiralrohre aus Inconel 718 mit Gitterstrukturen zur Gewichtsreduzierung.
- Intelligente Abschirmung: Graphen-beschichtete Röhren mit adaptivem SE durch Spannungsabstimmung.
- Nachhaltigkeit: Recycelbare Titanrohre für umweltfreundliche Elektronik (RoHS/REACH).
Schlussfolgerung
Die Materialauswahl für Handa Shield Spiralrohre und Dichtungen hängt von einem ausgewogenen Verhältnis zwischen Leitfähigkeit, Umweltbeständigkeit und Kosten ab. Während rostfreie Stähle bei allgemeinen Anwendungen dominieren, decken Legierungen wie BeCu, Elgiloy und Hastelloy Nischenanforderungen in der Luft- und Raumfahrt, der Medizin und der Chemie ab. Künftige Innovationen bei Hybridwerkstoffen und intelligenten Beschichtungen versprechen leichtere, anpassungsfähige Lösungen.