Electrical Conducting Canted Coil Springs
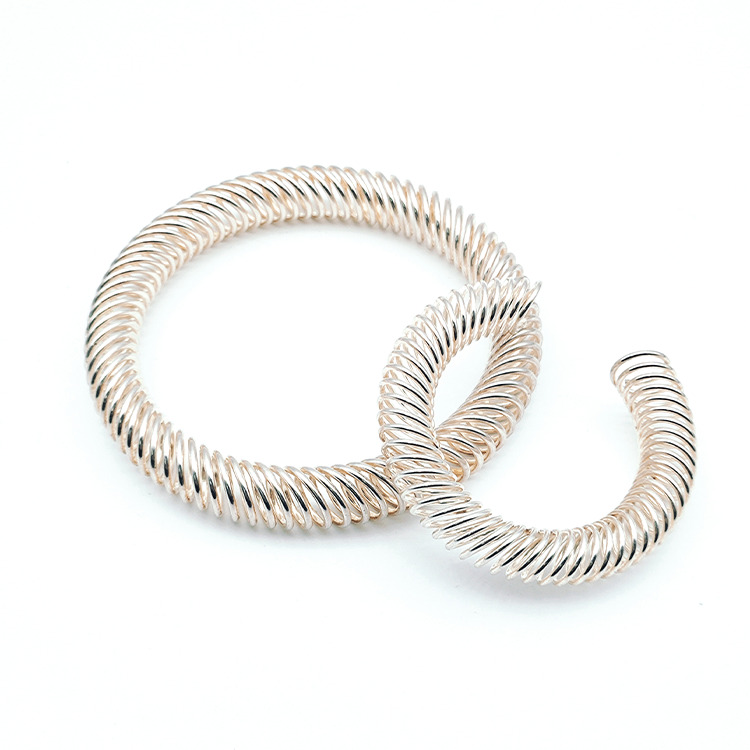
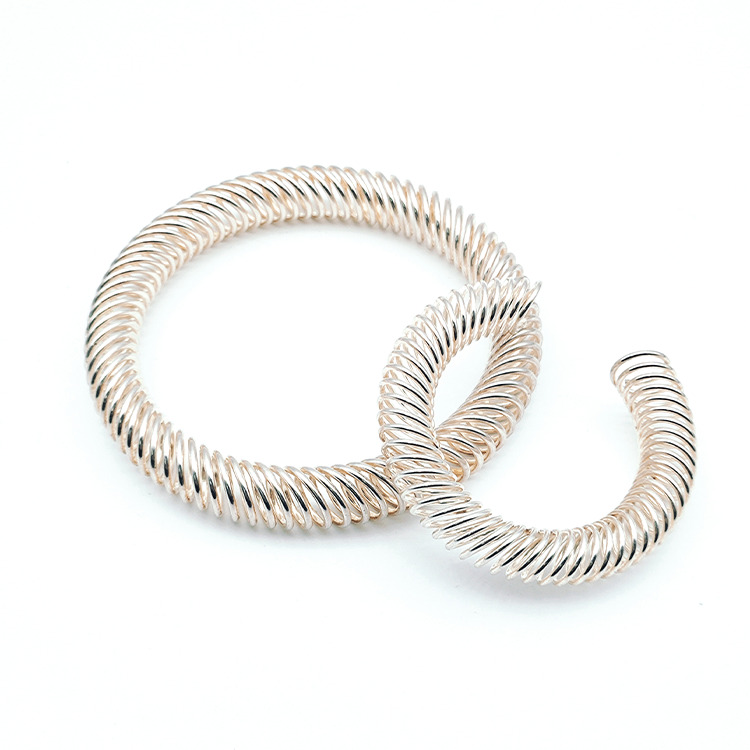
Electrical Conducting Springs, such as the Handa Shielding Spring® canted coil spring are springs specifically designed to conduct electrical current while providing mechanical support. Made from highly conductive materials such as copper alloys or stainless steel, these springs facilitate the flow of electricity through electronic and electrical systems.
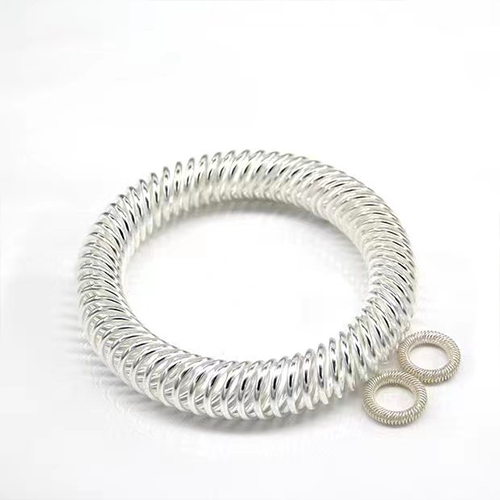
Electrical Conducting Springs
In the fields of electrical and mechanical engineering, electrical conducting canted coil springs have emerged as pivotal components due to their unique blend of electrical conductivity and mechanical robustness. This article provides an in-depth examination of canted coil springs, focusing on their design, performance, applications, and customization. By understanding these aspects, engineers can better utilize these springs to enhance the performance and reliability of their systems.
Table of Contents
The Essence of Electrical Conducting Canted Coil Springs
Electrical conducting canted coil springs are distinguished by their angled coil configuration, which sets them apart from traditional springs. This design feature enables a compact footprint, allowing for the management of more power in less space while maintaining cooler operating temperatures. The coil’s angled arrangement not only optimizes space but also improves heat dissipation. This is particularly advantageous in applications where heat management is crucial, as it minimizes heat rise and ensures a consistent, reliable electrical connection even under shock and vibration.
The design of electrical conducting canted coil springs involves winding a wire into a helical shape and then angling it slightly. This results in a spring that can handle a variety of current levels—high, medium, and low—over extended periods. The design’s resilience to heat and mechanical stress makes it ideal for environments where reliability and performance are critical.
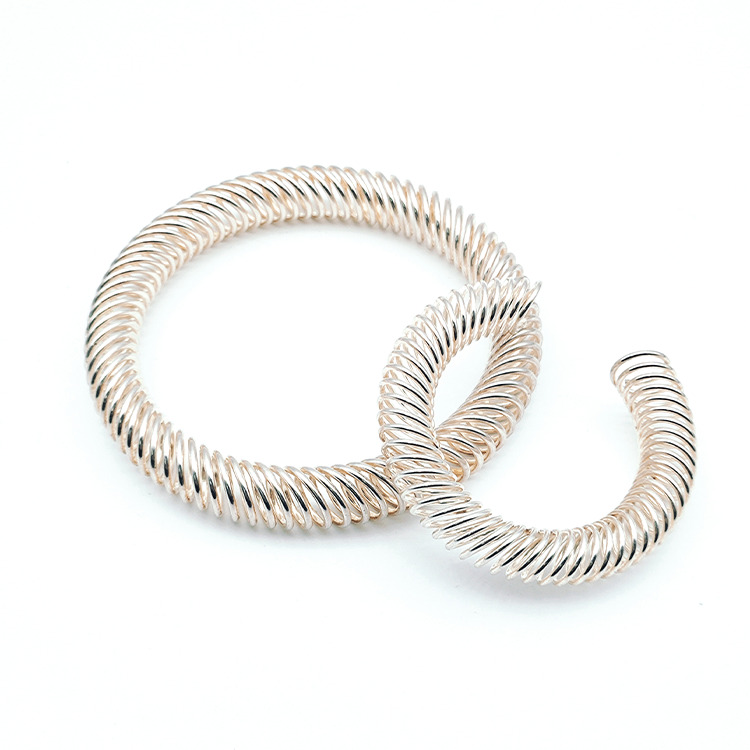
Versatile Applications
Canted coil springs are known for their versatility and can be utilized in various configurations:
- Housing-Mounted Configurations: These springs are commonly used in devices where they are mounted within a housing. This configuration is beneficial in applications requiring stable electrical connections and reliable mechanical performance within a confined space.
- Piston-Mounted Configurations: In piston-mounted applications, electrical conducting canted coil springs provide effective electrical conducting and mechanical connecting capabilities. Their ability to handle dynamic forces and maintain contact under movement makes them suitable for piston-based systems.
The design flexibility of canted coil springs allows for the incorporation of grooves with various profiles, including rounded, flat, or “V”-shaped bottoms. This customization caters to specific application requirements, whether for electrical conducting or grounding in static or dynamic environments. The versatility ensures that canted coil springs can be tailored to meet the demands of diverse applications.
Performance Factors
Several key design factors influence the performance of canted coil springs:
- Wire Material: The choice of wire material significantly impacts the spring’s performance. Common materials include copper alloys and stainless steel, each offering a unique combination of mechanical and electrical properties. Copper alloys are often chosen for their excellent conductivity, while stainless steel provides durability and corrosion resistance.
- Diameter and Coil Height: The diameter of the wire and the height of the coils affect the spring’s mechanical properties, including its force and flexibility. Precision in these dimensions ensures that the spring can handle the required loads and maintain its shape under stress.
- Spring Force: The spring force is a critical parameter, determining the amount of force the spring can exert. Engineers must carefully calculate this force to ensure that the spring meets the specific needs of the application.
- Plating Thickness: For applications requiring enhanced conductivity or protection against corrosion, plating with metals such as silver may be applied. The thickness of the plating affects both conductivity and resistance to environmental factors.
Canted coil springs are designed to manage continuous current ranges, resist compression set, and compensate for misalignment and tolerance variations. This capability makes them ideal for applications that require both electrical conducting and mechanical connecting.
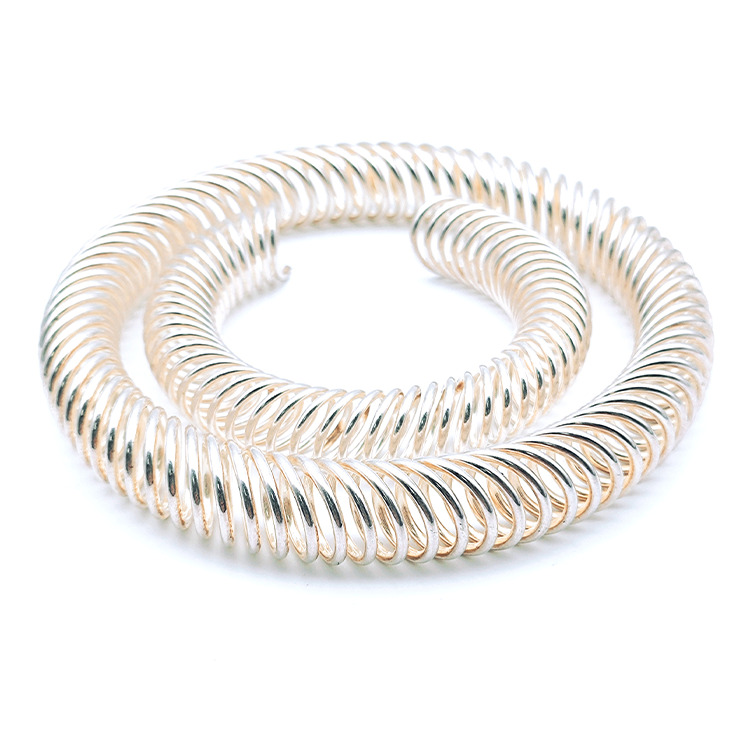
Material Choices
The materials used in electrical conducting canted coil springs are selected for their ability to provide a balance of mechanical strength and electrical conductivity:
- Copper Alloys: Copper alloys are commonly used due to their excellent conductivity. They are suitable for many applications without additional plating, though they may not always offer the required level of corrosion resistance.
- Stainless Steel: Stainless steel provides durability and resistance to corrosion, making it suitable for more demanding environments. It is often used in combination with other materials to enhance performance.
- Plated Materials: For enhanced performance, especially in humid or corrosive environments, plating with metals such as silver can be applied. Silver plating increases conductivity and provides additional protection against corrosion. Protective coatings are also applied to silver-plated contact elements to enhance their resistance to environmental factors.
Customization and Availability
Canted coil springs can be customized to meet the specific needs of various applications. They are available in non-welded lengths of various sizes, accommodating both simple and complex groove configurations. Welded rings are available from 2.51 mm ID, providing additional flexibility in design.
Given the unique requirements of each application, there is no standard size or type for electrical conducting canted coil springs. Instead, manufacturers maintain a database of commonly-requested diameters and cross-sections for streamlined customization. This approach ensures that engineers can obtain springs tailored to their specific needs without compromising performance.
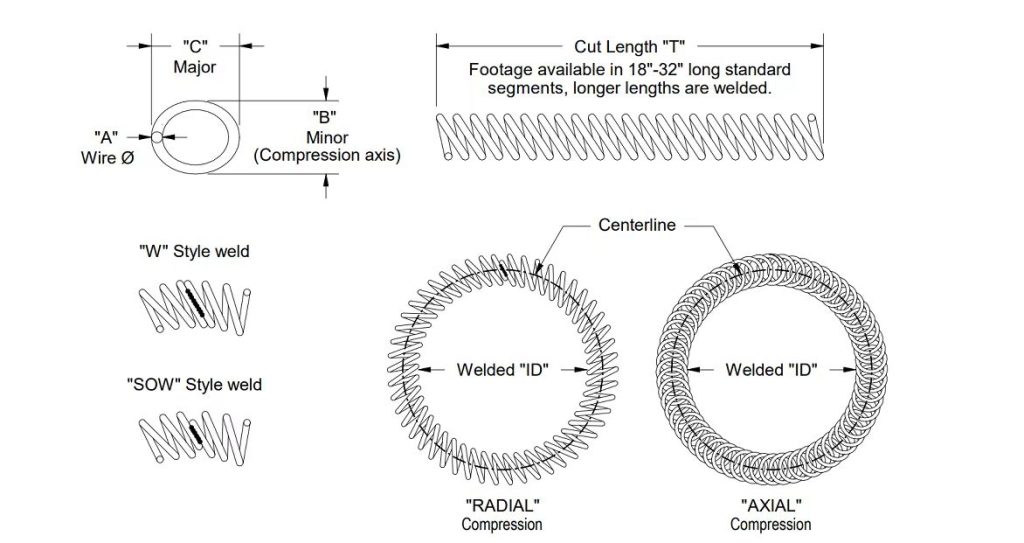
Orientation and Design
The orientation of the coils in a electrical conducting canted coil spring can be either axial or radial, depending on the application:
- Axial Orientation: In axial springs, the coils are oriented along the axis of the spring. This configuration is often used for face-mounted installations, where the spring needs to provide consistent force along its length.
- Radial Orientation: Radial springs have coils oriented perpendicular to the axis of the spring. This design is typically recommended for housing or piston-mounted configurations, where the spring needs to exert force in a radial direction.
The choice between axial and radial orientation allows for optimization of the force direction in the design, ensuring effective, long-term service.
Conclusion
Electrical conducting canted coil springs represent a sophisticated solution for both electrical and mechanical applications. Their unique design offers a blend of performance, versatility, and customization, making them suitable for a wide range of applications. By understanding the design principles, material choices, and performance factors, engineers can leverage canted coil springs to enhance the performance of their equipment. These springs help reduce size, weight, and system complexity while ensuring reliable, long-term service. As technology continues to advance, canted coil springs remain a valuable asset in the pursuit of efficient and effective engineering solutions.
You May Also Like
-
EMI tapes, EMC foils, conductive textiles & half conductive non-woven
Conductive aluminium tape
Aluminium foil, a widely recognized material in both household and industrial applications, is particularly valued for its role in electromagnetic shielding. This article delves into the properties, applications, and considerations surrounding the use of aluminium foil for electromagnetic shielding. Its......
-
EMI/EMC Shielding | RFI Shielding | EMI Gaskets
Fingerstrips
Introduction to Contact Finger Springs Contact finger springs are crucial components in the field of electronics and electrical engineering. They play a pivotal role in ensuring reliable electrical connections in a wide array of devices and systems. Understanding these components......
-
Shielding Gasket Solutions and Materials
Knitted wire mesh gaskets
Knitted metal wire mesh gaskets are engineered using fine metal wires, typically stainless steel or other conductive alloys, that are knitted or woven into a mesh structure. This design enables the gaskets to conform closely to mating surfaces, providing a......