An Overview of Conductive materials
Conductive materials play a crucial role in numerous industries due to their ability to facilitate the free flow of electrons, thereby conducting electricity efficiently. These materials are characterized by their low resistance to electrical currents, allowing for the seamless transmission of electrical charges. Here’s a closer look at some common conductive materials and their applications:
Table of Contents
Examples of Conductive Materials
1. Metals
- Silver: The best conductor of electricity. Used in high-performance electronics, connectors, and specialized applications where maximum conductivity is crucial.
- Copper: Widely used due to its good conductivity and lower cost. Common in electrical wiring, motors, and transformers.
- Gold: Known for its resistance to corrosion and good conductivity. Used in connectors, switches, and high-end electronic devices.
- Aluminum: Lightweight and moderately conductive. Used in power transmission lines and some electronic components.
- Steel: Generally less conductive than copper or aluminum, but used in electrical applications where strength is needed, such as in electrical cables and grounding systems.
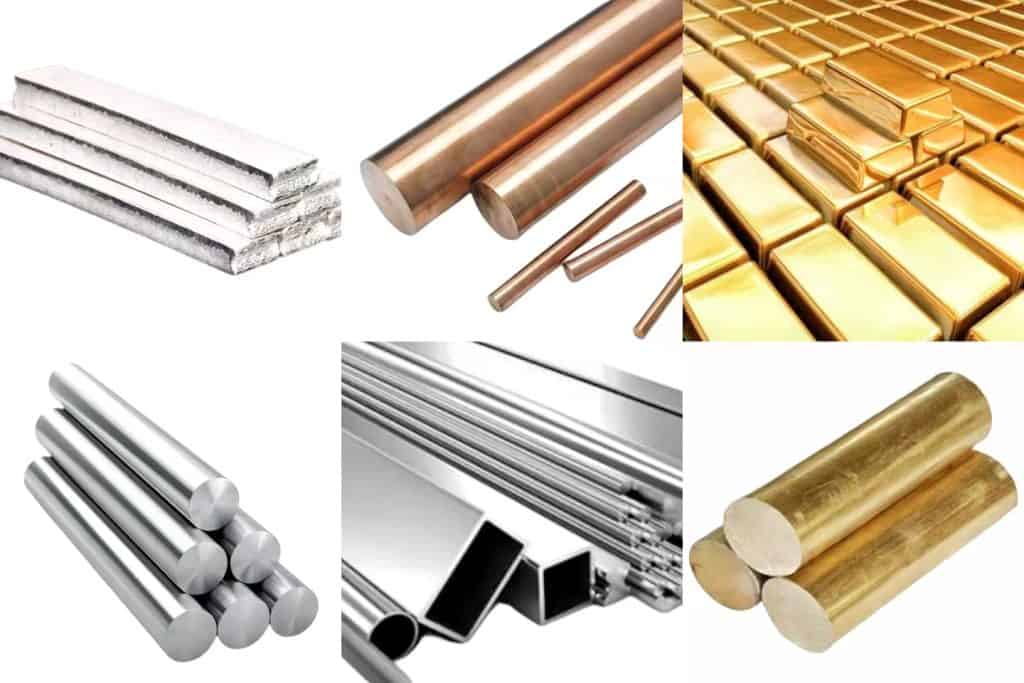
2. Alloys
- Bronze: An alloy of copper and tin, less conductive than pure copper but still used in some specialized applications like connectors and electrical contacts.
- Hardened Copper: A modified form of copper with enhanced mechanical properties, used in situations where both high conductivity and strength are required.
3. Non-Metals
- Graphite: A form of carbon with high electrical conductivity, used in electrodes, batteries, and as a lubricant in electrical contacts.
4. Solutions and Gases
- Salt Solutions: Water mixed with salts like sodium chloride conducts electricity well due to the movement of ions.
- Mercury: A liquid metal that conducts electricity, though it’s toxic and less commonly used due to health and environmental concerns.
- Hydrogen: While not a solid conductor, in its ionized form (plasma), it can conduct electricity effectively. It’s not commonly used in this form for practical electrical applications.
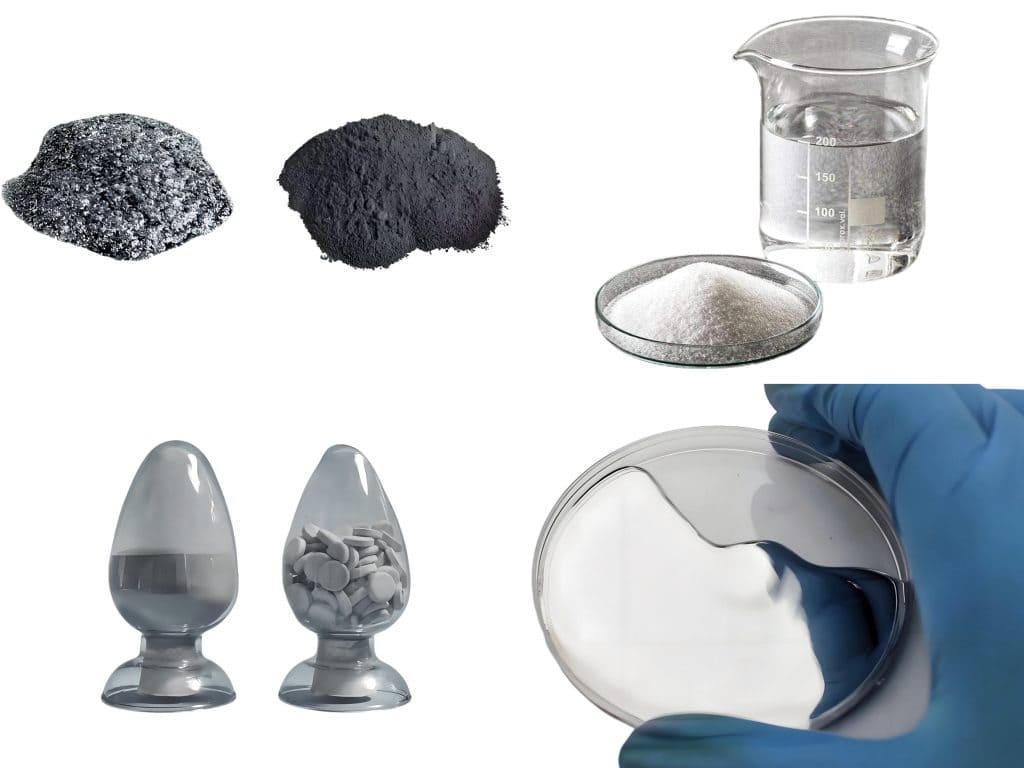
Characteristics of Conductive Materials
- Low Resistance: They offer no resistance to electric currents, ensuring their free circulation.
- Free Flow of Electrons: They allow the free flow of electrons between particles, facilitating electricity conduction. Copper is often used as a reference for measuring and comparing other materials’ conductivity levels.
- High Number of Free Electrons: This characteristic facilitates the transmission of charge from one object to another.
- Atomic Structure: Their atomic structure allows electricity to flow without requiring a large amount of energy for the passage of electrons between atoms.
- Malleability: These materials are highly malleable, meaning they can be shaped without breaking.
- Wear Resistance: They have high resistance against wear and can withstand exposure to extreme conditions, such as high temperatures, without significant degradation.
- Insulating Layer: Some materials have an insulating layer to prevent the electric current from coming into direct contact with surfaces where it’s used domestically or industrially.
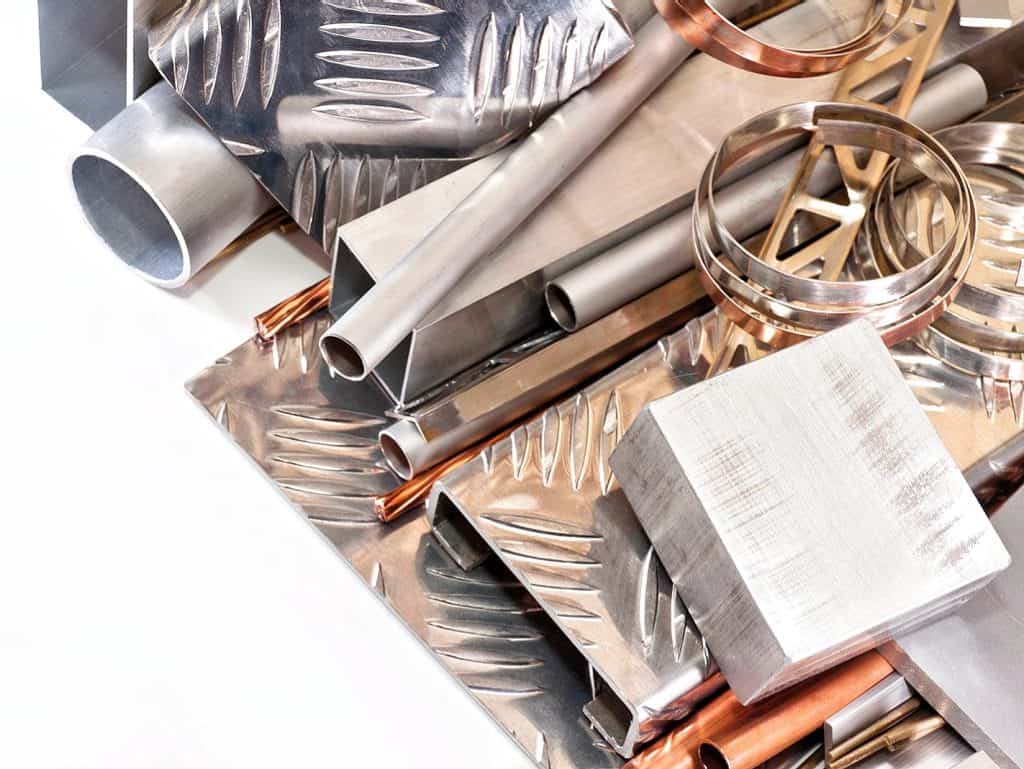
Applications of Conductive Materials
1.Electronics Manufacturing
- Printed Circuit Boards (PCBs): Conductive materials, often in the form of copper traces, are essential for creating the pathways that carry electricity through PCBs. Without these conductive paths, electronic devices would not function.
- Sensors: Many sensors rely on conductive materials to detect changes in physical quantities such as light, heat, motion, moisture, etc., converting these changes into electrical signals.
- Integrated Circuits (ICs): ICs, the building blocks of modern electronics, require conductive materials to create the intricate patterns of transistors, capacitors, and resistors that enable digital processing.
2.Energy Generation and Storage
- Solar Cells: Solar panels use conductive materials to collect sunlight and convert it into electricity. The conductive layers within solar cells facilitate the movement of electrons generated by photons.
- Batteries: Batteries depend on conductive materials to transport ions between electrodes, storing and releasing energy. Lithium-ion batteries, for example, use conductive electrolytes to enable the flow of lithium ions.
- Wind Turbines: Wind turbines use conductive materials in generators to convert wind energy into electrical energy. The rotating blades generate electricity, which is then transmitted via conductive wires.
3.Communication Technologies
- Antennas: Antennas in wireless communication systems use conductive materials to transmit and receive radio waves. The design of antennas relies heavily on the properties of conductive materials to optimize signal reception and transmission.
- Cables and Connectors: High-speed data transmission requires conductive materials in cables and connectors to minimize signal loss and ensure reliable data transfer rates.
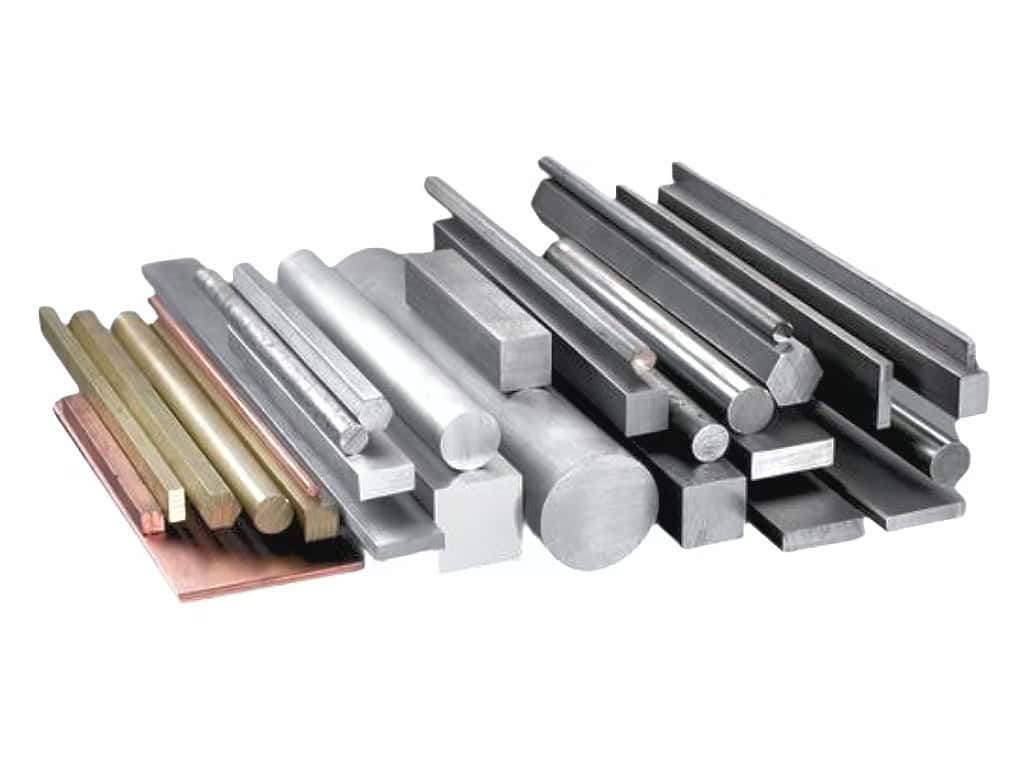
4.Aerospace and Defense
- Electrical Wiring: Aerospace and defense applications use conductive materials for electrical wiring within vehicles and equipment. These materials must withstand harsh conditions, including extreme temperatures and vibrations.
- Shielding: Conductive materials are used to shield electronic components from electromagnetic interference (EMI) and radio frequency interference (RFI),such as Handa fingerstrips and EMI shielding springs.
5.Medical Devices
- Implantable Devices: Implantable medical devices, such as pacemakers and insulin pumps, use conductive materials to safely transmit electrical signals to the body. These materials must be biocompatible and durable.
- Diagnostic Equipment: Diagnostic imaging equipment, such as MRI scanners, utilizes conductive materials in their construction to manage magnetic fields and electrical currents.
In conclusion, conductive materials are essential for the operation of countless electronic and electrical devices, thanks to their unique properties that allow for the efficient conduction of electricity. Their widespread use underscores the importance of understanding and selecting the right conductive material for specific applications based on factors like cost, conductivity level, and environmental conditions.